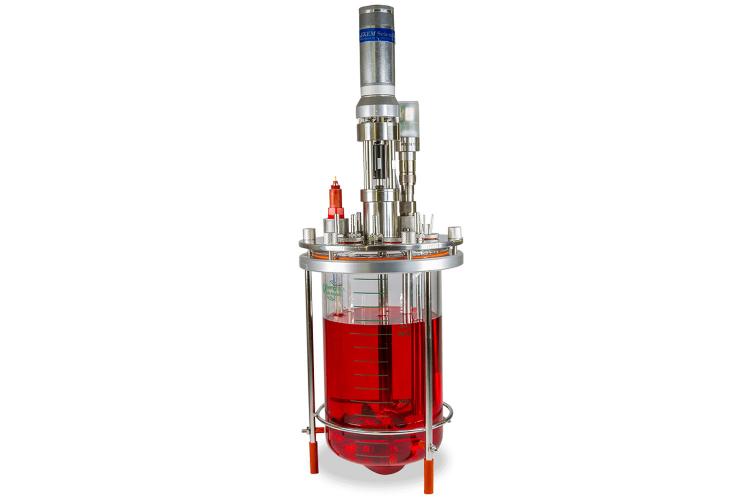
Figure 1: The AES bioreactor provides a range of controlled capabilities meant to automate cell culture production.
Bioreactors are designed to provide a wide range of activities based on the needs of individual applications. The small-scale AES (Oceanside, CA) bioreactor is a cell culture system that provides a wide range of controlled capabilities meant to automate cell culture production (see Figure 1). The glass reactor is reusable and autoclavable, ideal for early-stage research, product development, and commercial applications. Stainless steel components and a head plate provide a longer life cycle use for the benchtop system. Control hardware and software are 21 CFR Part 11, GMP/GLP and ISA-88 compliant to satisfy a wide range of regulatory requirements.
The company has been designing and manufacturing systems for the life sciences industry for over ten years. Their systems are used as the first step in drug analysis and evaluation for a variety of biotechnological applications. The company has designed and manufactured benchtop units from 2- to 15 liters in size. Each system is able to create an ideal environment for a wide range of cell lines and organisms—and supports high cell density processes. Integrated pH and DO control and 4 gas MFC control enables adjustment of the gas environment inside the reactor to suit a broad array of application needs. Typical applications include bacterial and mammalian product cell line systems. These bioreactors can be used as a platform for solera, seed train, perfusion, or N stage batch and fed-batch operations
Each benchtop unit is designed with a streamlined externally housed quad-pump that saves valuable workspace whether used in the lab or in a commercial environment. As part of an automated process, the industrial controller enables remote process monitoring and control wherever network access is available. An intuitive user interface makes the unit easy to operate, and easy for the user to monitor and adjust all processes that are running on the bioreactor cell culture system at any time.
The AES systems provide users with a modular control layer that integrates quickly and easily with an existing distributed control system. Online adjustments, historization, and system information is presented remotely through a networked computer or local human machine interface. In addition, all control software code is transparent and open protocol, which provides users with the freedom to make modifications and provide updates as needed.
Oxygen is continually monitored and the speed of the motor changed to facilitate a controlled oxygen level set by the user. Typically, the BLDC motor runs between a 100 and 300 rpm range. When the bioreactor is used with higher density cultures, such as bacterial fermentations, speeds can reach over the 1200 rpm range. In this case, the company incorporates a maxon brushed motor that provides the system the higher torque needed for such applications.

The mixing impeller relies on a high-tech brushless DC motor (BLDC) and gearbox designed and manufactured by maxon (see Figure 2). The motion components are fitted with an integrated encoder and placed inside an IP rated enclosure. All of these precision motion components are then inserted into the agitation shaft and connected to the mixing impeller. An additional feedback loop to the control system is used to maintain proper temperature and oxygen infusion, which is used to respirate the mammalian cells.
Conclusion
When working with highly sensitive equipment such as the AES bioreactor, users need to feel secure that the system will perform to their standards. The advanced design and manufacturing that goes into every maxon motor further provides the precision and extended life cycle required by users. Combine the integration of the proper motion system along with the high-quality design of the other bioreactor components and users have access to one of the more stable desktop units available on the market.