- When talking about resolution: Keep in mind the difference between the number of pulses per channel (counts per turn, cpt) and the number of states (the quadcounts)!
Positioning: Resolution and accuracy.
The required positioning resolution of the application dictates the encoder resolution to be selected. A well-tuned system can maintain the position within 1 encoder state (quadcount). Hence, the encoder resolution in quadcounts (states) should at least correspond to the maximum permissible positioning error. Depending on the response time of the system, a higher encoder resolution should be chosen in order for the controller to detect deviations faster and counteract quicker.
- Observe: It’s not only the resolution of the encoder that influences accurate and dynamic positioning and speed control. It’s the reaction of the system as a whole. The response time may be limited by current and voltage restrictions of power supply and controller, by the sampling rate of the control loop, by mass inertias, friction variation and mechanical play.
Signal jitter – particularly if large compared to the nominal state width of the encoder – reduces the accuracy in terms of repeatability that can be achieved. In this respect, direct sensing optical encoders have advantages over interpolated magnetic encoders. Direct sensing larger optical encoders also have advantages concerning the absolute accuracy. Their Integrated Non-Linearity (INL) is very small.
Rule #1: Encoder for Positioning
Recommendation: Select an encoder with number of pulses higher than 360° divided by the required angular position accuracy; i.e. a number of states that is 4 to 10 times higher. For positioning, select an encoder with Line Driver (differential signal).
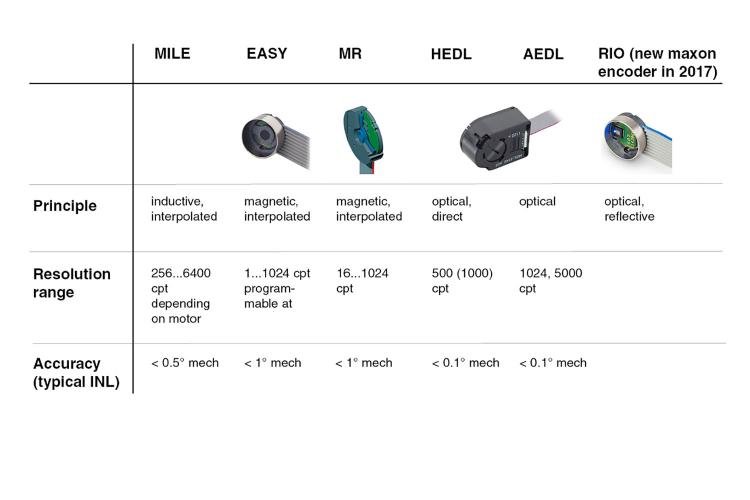
Table 1: Relative accuracy and resolution range of selected maxon encoder types.
Rule #2: Encoder for High Precision Positioning
Select optical encoders with Line Driver for high-precision positioning. They have a higher resolution, less jitter and a lower INL than interpolated magnetic encoders.
Mechanical transformation
A very high accuracy in positioning is difficult to achieve with mechanical transformation and the associated play. Therefore, high resolution encoders only make sense on direct drive applications. Very often, high precision positioning not only requires a high number of states but also a high absolute accuracy. Optical encoders have here advantages, both due to a high resolution and a low INL.
Drive systems with mechanical transformations such as gearheads or lead and ball screws do not require a high encoder resolution. The resolution of the encoder mounted on the motor will be multiplied by the gear reduction. Similarly, on a screw with 5 mm pitch a moderate encoder resolution of 512 quadcounts (128 cpt) will result in a theoretical position accuracy of the nut of about 10 microns. That’s often much less than the mechanical play in the coupling and the nut and the accuracy of the screw thread.
Rule #3: Encoder for Positioning with Mechanics
Select a magnetic encoder with Line Driver and with a moderate or low number of states. The mechanical reduction will increase the resolution. Due to the mechanical play you will not be able to benefit from a high precision optical encoder.
Absolute encoders
Incremental encoders measure only changes in position and require a homing procedure for absolute position reading. Homing procedures are typically performed at low speeds, taking time that is not available in some applications. In multi-axis systems - for example in kinematically complex robotic applications with mechanically interdependent axes - homing could cause collisions and damage. In such cases, absolute encoders can be used as an alternative to incremental models. After being switched on absolute encoders provide the actual position directly (without a homing procedure) within one motor turn (single turn) or multiple turns (multi turn).
In industrial applications, absolute encoders with a serial interface ((SSI, Biss-C, …) are often used transmitting the actual position as a bit-stream. A total of only six lines is sufficient for the supply voltage, data transmission and synchronization of the transmission timing.
For single-turn absolute encoders, one axis revolution is coded in N steps. The coding repeats when rotating more than 360°. Typical resolutions are 12-bit (4096 positions) and more per revolution. In multi-turn absolute encoders, the numbers of revolutions are additionally coded and stored in the same bit stream. Multi-turn encoders are required when the number of measurement steps of a single-turn encoder is not sufficient, for instance for longer paths.
A classic application with absolute encoders is the tracking mechanism of solar installations. Homing with an incremental coder would be too time consuming, as the speeds used for such installations are very slow. For all types of flow regulators, filling systems and conveyor equipment, it is important to know the flow rate exactly from the very first moment. A homing procedure would mean an uncontrolled flow of material. Additional applications with absolute encoders are robotics, handling machines and positioning of machine tables, spotlights and other stage elements. The maxon positioning controllers (EPOS, MAXPOS) support the use of many variants of absolute encoders.