Between 1760 and 1840, the first industrial revolution moved from hand production to using steam and waterpower.
From around 1871 -1914, the second industrial revolution came about due to the prolific building of railroads and factory electrification. It was also the start of telecommunication networks that allowed for faster transfer of idea sharing and led to the first modern production lines.
The third revolution was digital at the end of the 20th century with the invention of computers. Operators could programme them to carry out and run repetitive mechanical tasks, hugely increasing production and reducing labour costs.
We are now at the beginning of the 4th industrial revolution, also called digital manufacturing, the Industrial Industry of Things (IIoT) and Industry 4.0. So, what do the changes hold for business and the workforce?
What are the challenges for Industry 4.0?
As with any revolution, there will be political, economic, organisational and social challenges to overcome. Political: joined-up regulation and legal issues. Economical: high-cost implementation benefiting first world countries. Organisational: reliability, security and safety, protection of IP and training of the workforce and social: Privacy concerns and surveillance mistrust, reluctance from the current workforce due to fear of change and job security.
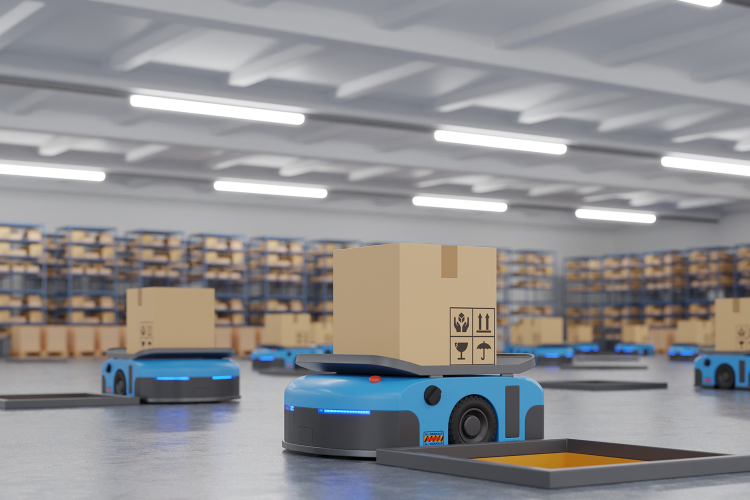
The latest revolution brings automation for data exchange - advanced human-machine interfaces with communication in real-time. Combine this speed with big data and digital processing platforms for greater operator transparency. The operator will identify and optimise the overall task and allow the system components autonomy by monitoring itself. This ability gives tremendous flexibility where machines predict failure modes and correct or plan maintenance before it even happens. With downtime reduced and overall efficiency going up, and the continued reduction of the labour force, companies will see significant cost savings. However, the workforce will be wary and concerned with the loss of jobs. In every automation project in the history of the industrial revolution, some jobs will become obsolete; however, new jobs created from innovation would require different skillsets, and people would require retraining.
What would this look like?
There are enormous opportunities for all areas but let's look at what tomorrow's factory might look like.
Machine Learning
Autonomous Mobile Robots (AMR) would work on different routes on different days and adapt themselves to change their path depending on the demand in warehousing and intralogistics. They have an array of sensors to allow them to navigate around each other and the human workforce. Also, should they need maintenance, the AMR's will self-diagnose and visit the workshop for preventative or critical upkeep.
Smart factory
Industry 4.0 encompasses the idea of the "smart factory", which adopts Cyber-Physical Systems. CPS is where a computer-based algorithm controls a mechanism and is linked with the Internet of Things, where equipment embedded with sensor technology has the sole purpose of exchanging data over the internet. Examples of CPS are self-driving cars or drones that are virtually aware of their surroundings. Instead of warehouses and factories unloading deliveries with a flow chain carried out by people, a lorry would supply the precise quantity of raw material, determined by automated data collection. Products are developed and tested digitally. The smart factory will operate from delivery to end product with minimal supervision.
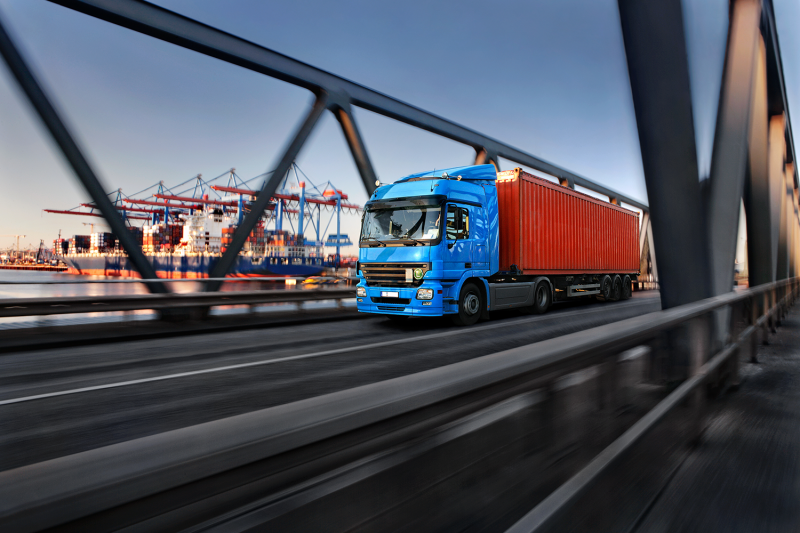
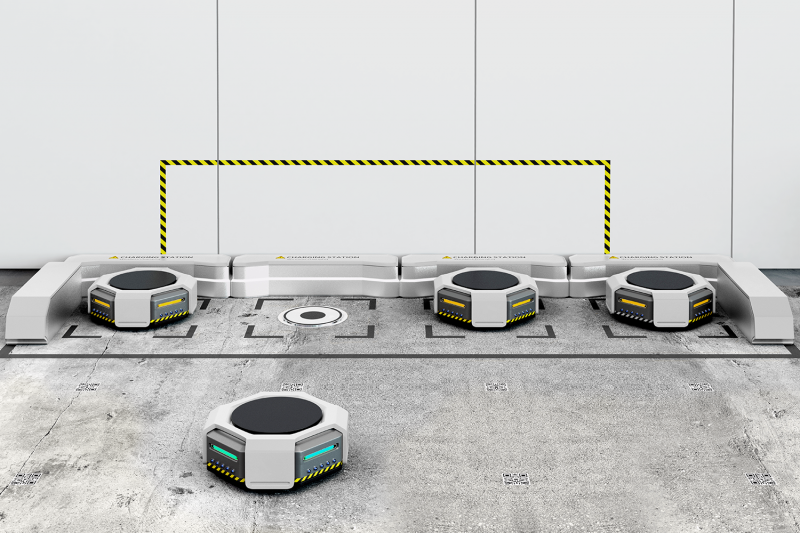
Our customers are often at the forefront of industry transformation, and it is our challenge to design and manufacture products to keep driving innovation.
To offer AGV and AMR designers maximum freedom, the maxon Group has developed an entire range of compact and modular motors. These IDX drive solutions meet the most demanding requirements: offering 20% higher performance than current solutions on the market.