maxon motor evolves more and more from a supplier of components to a provider of system solutions. Components to be understood as motors, gearheads, encoders, as well as speed and position controllers. As a system, we consider complete drive solutions in the sense of mechatronic units and subsystems, which are integrated into a larger context. The focus shifts from the individual components used towards the main functionality to be fulfilled.
The starting point is a customized component, more precisely a flat motor. For improved heat dissipation, the rotor is perforated and a special cable and connector is required for the connection to the customer-made motor drive electronics. The precise purpose of the motor and its mechanical and electrical interfaces are unknown at the beginning. Only after a closer look provided by the customer it becomes clear that the motor drives a geared robotic joint. Strongly limited space associated with a correspondingly complex mounting of the existing solution and required additional functionalities are good reasons for an integrated system solution.
Mechanical requirements
· Low speeds and high torques call for a geared motor
· Motion range at gear output: approx. 120°
· Blocking of the joint in case of power failure (holding brake)
· Possibility to release the blocking. System may not be self-blocking.
· Cables to pass through the joints
Electrical and electronical requirements
· Driver for the brushless motor (including commutation, current and speed control)
· Communication with higher level master control
· Angular sensor for motor and gear output, position information to be sent to master
All this happens in the context of limited, predefined dimensions and weight. In addition, emissions (temperature, vibrations, and audible noise) must be kept low. Powered by batteries, the system should work energy-efficiently. And of course, costs must be considered as well.
This list of requirements is a showcase for the aspects to think through when pursuing an integrated solution. Only an intense and open communication between customer and system integrator can clarify these aspects.
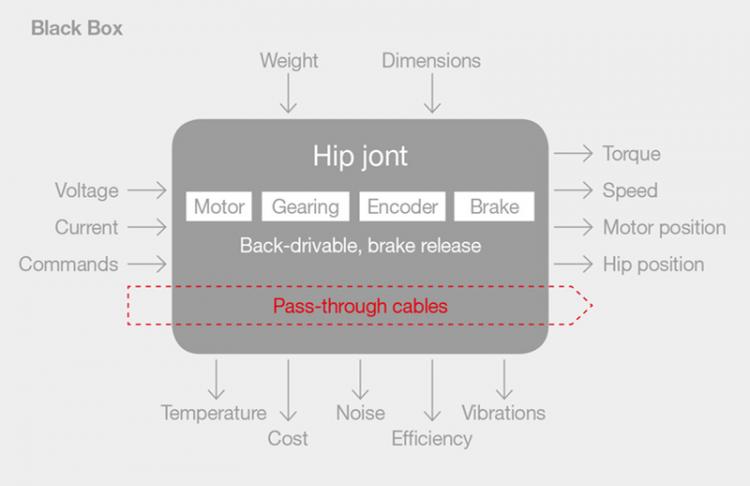
System delimitation
The first question to answer: What should be part of the system? Where can reasonable system boundaries be set considering the functionality to achieve? How does the system environment, how the mechanical, electrical interfaces look like? How is information exchanged and how does the end user communicate with the complete system?
When developing complex systems, people with different knowledge background and different points of view are involved. How can communication be set up in an optimum way in order to have all persons to understand the same and to strive for the same goals? A black box consideration as sketched above may help. A top-down approach, which does not get lost in details, is also reasonable. Another aspect often ignored when dealing with complete systems: How can the needs of the end user be taken into account?
Specifying systems
The trigger for a system development may contain important hints for the formulation of the objectives to reach. Is it a new development? Is it about improving an existing solution? Why is the existing solution unsatisfactory? The basis for a specification is always a situation analysis: What is it really about? How does the system context look like? It is important to formulate the catalog of objectives neutrally, i.e. not implying a solution. In the example above, the required blocking upon power failure might also be obtained by a self-blocking gear and not only by a holding brake.
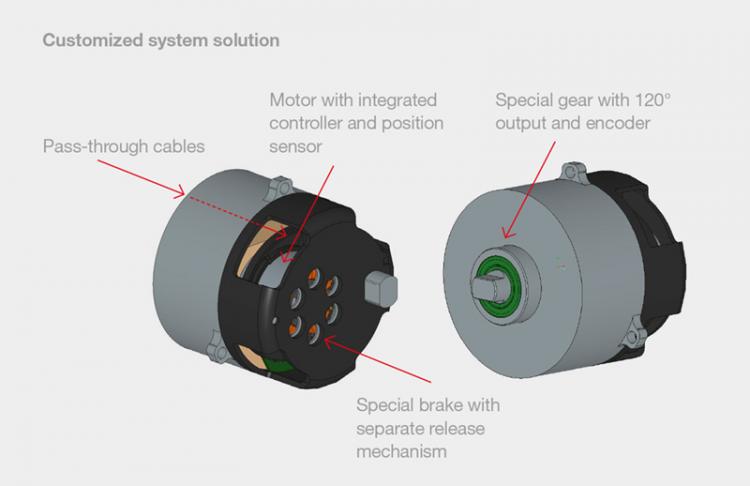
Solutions
The catalog of objectives serves as a basis to develop different solutions, which have to be judged by their suitability. Possible solutions often resort to existing products. In this context, I mention the design of the maxon product platform in recent years. It allows to resort to existing and proven components during system development, which in addition can be customized rapidly. All this minimizes the technological, time, and economic risks.
maxon systems appear most of the time in a mechatronic context combining mechanical and electrical components: drive mechanics, actuators, sensors, controllers. Software becomes more and more important, for instance in the form of controller firmware or of a computer program controlling a complete plant.
When relating different solutions, ascertain that apples are compared with apples. For example for the customer, the costs for an integrated system have to be balanced not only to the costs of individual components but also to the costs for interfaces and mounting.
Economic boundary conditions
An integral component of the situation analysis is the question, if and when a new design pays off. What quantities can be expected in which time period? Realistic market estimations are necessary. It must defined if the non-recurring engineering and tooling costs shall be part of the product price or if they are paid separately. Basically, a net present value calculation (NPV) can serve for the economic decision to start a project. However, additional criteria are strategic fit considerations and a risk analysis.
In summary, besides the aspects presented here, follow the steps and procedures as explained in the textbook „ Selection of high-precision microdrives “.
By the way
The proposed solution for the robot hip joint consists of the originally selected motor, however, with integrated electronics based on the maxon ESCON controller platform and combined with a special gear. Motor and gear positions are delivered by integrated encoders. A specially designed holding brake acts directly on the rotor and is located in the compact housing. For the customer, the mounting of this integrated system is much simpler and faster compared to the existing solution made of single components.