For applications that demand extreme torque and power output, smooth back drivability, longest life, and highest efficiency in the smallest volume.
Exceptional POWER in a compact design
maxon’s new product family GPX UP (Gear Planetary X-series Ultra Performance) is now available as a standard product offering and a selectable planetary gear type for a configurable X-drives assembly. The “best of class” UP complements maxon’s existing X-drive gearhead family, offering variants for different cost and performance objectives.
· GPX A (metal planetary pins - standard)
· GPX C (ceramic planetary pins – increased torque and life)
· GPX LN (reduced noise)
· GPX LZ (reduced back-lash)
· GPX HP (high power – increased torque capacity)
· GPX UP (Ultra performance – smooth back-drivability & maximum efficiency)
maxon would like to thank the Space and Aerospace industries for presenting demanding design challenges, which, in turn, pushed us to develop viable solutions. The result is the GPX UP series planetary gearbox.
The UP’s wide range of performance improvements offer new opportunities for the most demanding applications, be it Rovers on Mars or cutting-edge surgical robots.
Initially, design concepts for the UP were developed for the space projects ‘ExoMars’ (ESA's Mars project) & NASA’s 'Mars 2020’. These Rovers required extreme torque & power, and the highest efficiency possible for a lifetime of use, while being exposed to the most extreme environmental conditions known. In the end, the “UP” gearbox is a commercially available advanced gearbox design for extreme application requirements.
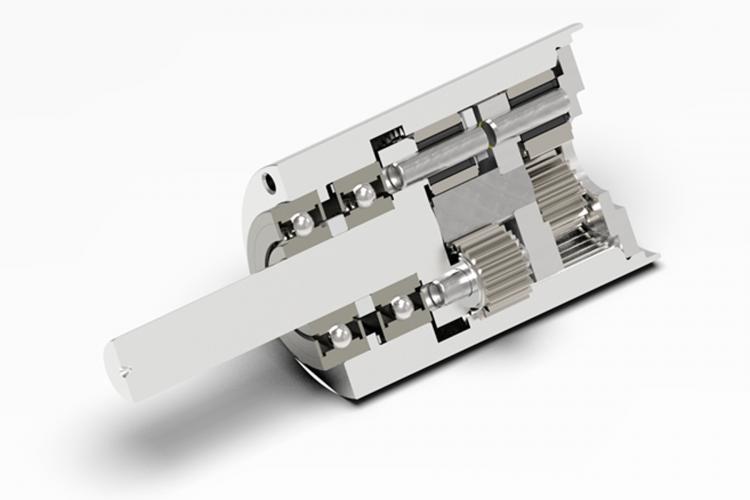
One of the great advantages of this new gearbox design is its exceptional high efficiency (ratio of output power/input power). Significantly reducing the friction in any mechanical system naturally leads to an optimized overall drive system. In a traditional planetary gear, the planet wheels/gears rotate on greased steel or ceramic pins (a simple plain bearing). However, in the UP-gearbox construction, this frictional interface is replaced with needle bearings. This innovation transitions the planet gear-to-pin contacting surfaces from a ‘sliding friction’ to a superior ‘rolling friction’. The result is planetary wheels that rotate on smooth-running bearings increasing efficiency, dramatically lowering generated frictional heat energy and prolonging lubricant life.
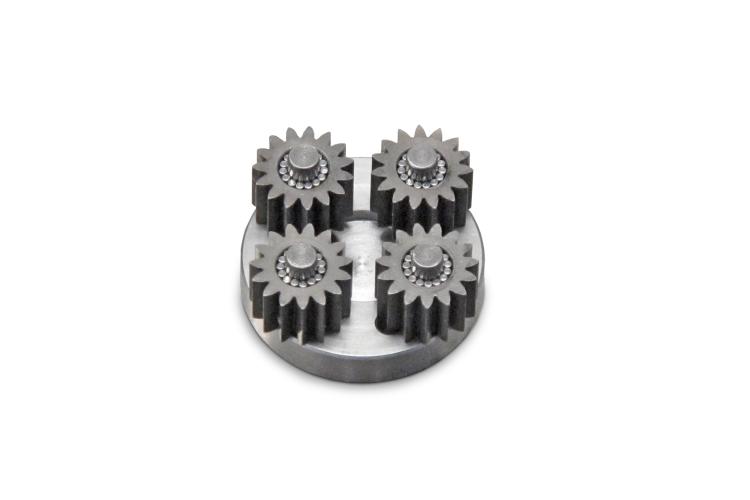
The maximum efficiency of the GPX32 UP (3-stage construction) is approximately 90% compared to a standard construction gearhead & equivalent gear ratio, which only achieves ~70%. This is an efficiency gain of ~20%. See figure Fig. 3.
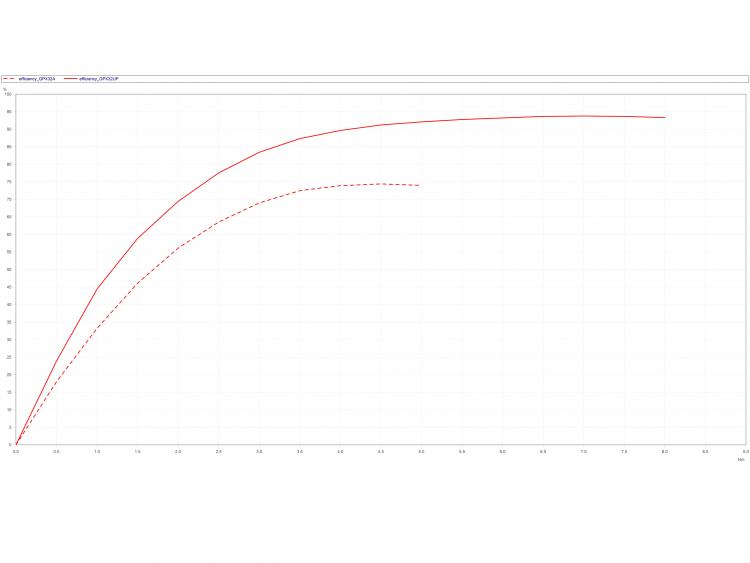
If the same motor & controller are affixed to the UP gearbox vs a traditional planetary gearbox, the increased efficiency results in a motor + gearbox assembly capable of producing 30% more torque and power at output. Or, put another way: the same output power will require 23% less input power from the drive. As a result of the reduced input torque need, a brushed motor is less taxed and worn, which equates to a longer lasting brush system and overall greater lifetime of the motor. Also, this allows a motor to operate in a more efficient area of the efficiency vs. torque curve or allow use of a smaller/lighter motor and associated control electronics. This can be an advantage to both weight and cost. With improved gearbox and motor efficiency, the entire assembly allows battery applications the longest possible run times. No need to recharge the battery - the assembly is still running.
Longer Gearhead Service Life
Significantly longer gearhead life is possible with the UP mainly because of the dramatically reduced friction between the planetary wheel ID and axle it rides on. At the same time heat generation from operating the gear is noticeably reduced because there is less heat friction being created and emitted. In applications where temperatures should not exceed a certain threshold level (ex. medical hand pieces) the UP provides an ideal solution.
The longevity of the lubricant plays an important role in terms of wear & tear on the gearhead's mechanical components. The greater the thermal stress, the more quickly the lubricating properties are lost. This, in turn, is quickly followed by abrasive behaviors in the mechanical system. The abraded metal particles lead to agglutination of the lubricant, potentially resulting in a breakdown in its lubricating ability. In the GPX UP, the frictional interfaces are replaced with bearings minimizing generated heat. In turn, the lubricant is kept healthy and the life of the gearbox is tested to be 11x greater than comparable competitor models.
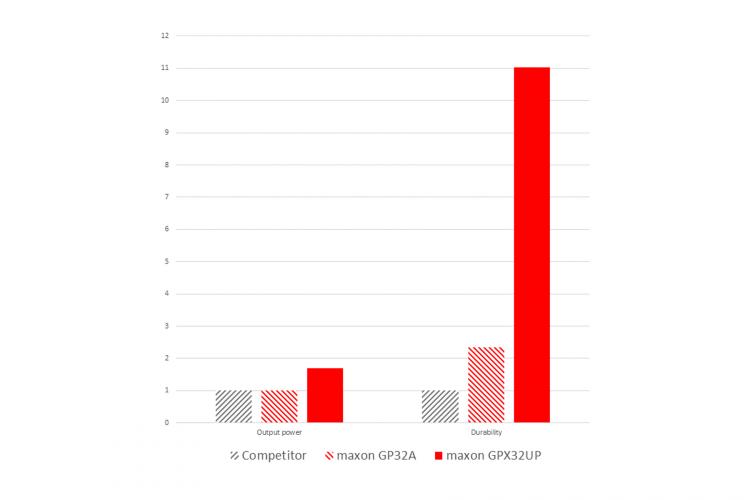
The new GPX UP improves output specifications over traditional planetary designs but also provides a viable solution to the haptic or force-feedback applications. The incorporation of needle bearings in the design provide high efficiency and smooth turning planet gears making the UP a perfect choice for applications that require smooth and repeatable back-drivability or turning the shaft from the output side of the gearbox. The torque feedback provided thru the GPX UP to the motor on the input side of the gear is consistently proportional to the load and quantifiable. Traditionally-built planetary gearheads cannot guarantee smooth back-drivability or consistent load interpretation through the gearbox because of fluctuating efficiency, altering tolerance stack-ups within internals of the gearbox (gearbox to gearbox), and potential cocking of planet gears. The UP resolves all these issues
Back-drivability in haptic devices:
In electronic flight control (Fly-by-Wire), the pilot's steering movements are not transferred to conventional mechanical or hydraulic actuators but rather transmitted electronically—the essential varying force feedback or “feel” is provided by a motor assembly in the control column of the joystick. This haptic generating motor assembly must contain a gearbox capable of both smooth back drivability and simultaneously generating torque/force based on the position of the joystick.
A similar approach is employed in cutting-edge surgical robots performing minimally invasive-, micro- and tele-surgeries (Fig. 5). Here it is critical that the doctor performing the surgery dynamically feels instantaneous equivalent forces as are being exerted by the performing surgery-robot, some distance away. The criticality of a smooth back driving gearbox within the motor assemblies for both the surgeon and surgery robotic consoles cannot be overemphasized. The UP delivers this functionality, even for gear ratios requiring 2 or 3 planetary stages. A traditional gear that has uneven or “sticking” back drivability is unusable and introduces noise to the mechanical system. The UP is an optimized haptic gearbox where torque cleanly passes through the gearbox either from the input or output sides of the gearbox, resulting in a superior haptic experience, mechanical system, and overall surgical robot.
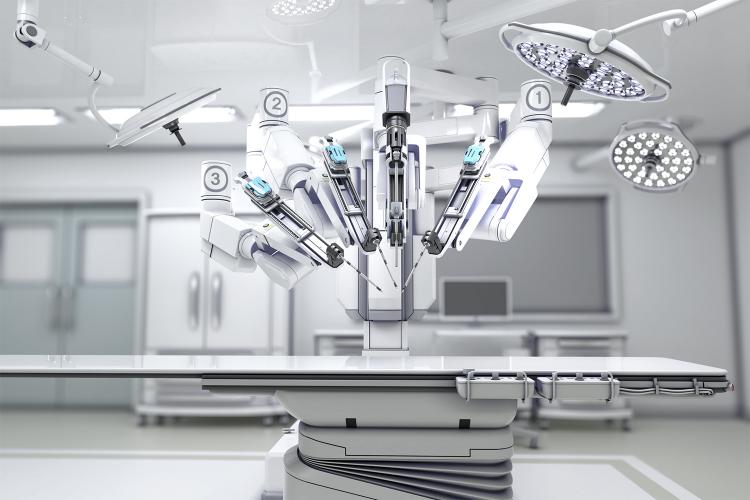
Ultra Performance GPX gearheads from maxon are already available in diameters 22, 32, 42 mm; and like all 'X-series' products they are customizable and orderable online. Currently, maxon in Sexau/Germany is working on the launch of the 10 & 8 mm diameter gears. In the future, the product series will expand to the full range of 8 mm to 58 mm diameters.
In summary, the new GPX UP planetary gearbox provides break-thru improvements to higher power and continuous/peak torque output, unsurpassed efficiency, unrivaled service life, less heat generation or cooler running, as well as, true smooth back drivability - even in a multistage gearhead. When you consider all the attributes only two words remain: “Ultra Performance”
Author: Peter van Beek, Sr Sales Engineer, maxon USA, Taunton, MA