People who have gone through a stroke or traumatic brain injury often lose the use of one of their arms. A variety of physical therapy methods that are used, such as motor-skill exercise; range-of-motion therapy; and mobility training that incorporates aids such as canes, walkers, and braces. Myomo, a medical robotics company located in Boston, Massachusetts, has developed a myoelectric orthosis (powered brace) that is motorized to help patients use their impaired hand and arm again.
Myoelectrics is a technology that uses sensors to recognize and measure the electrical signals generated by muscles as they are contracted. These sensors, also known as electrodes, sit on the skin and use a specially designed controller to detect even the slightest muscle contraction. The controller triggers motor activation to correspond to the user’s intended movement. Using an array of sensors and motors, individuals can control multiple features simultaneously, such as those in the elbow and hand of Myomo’s powered brace.
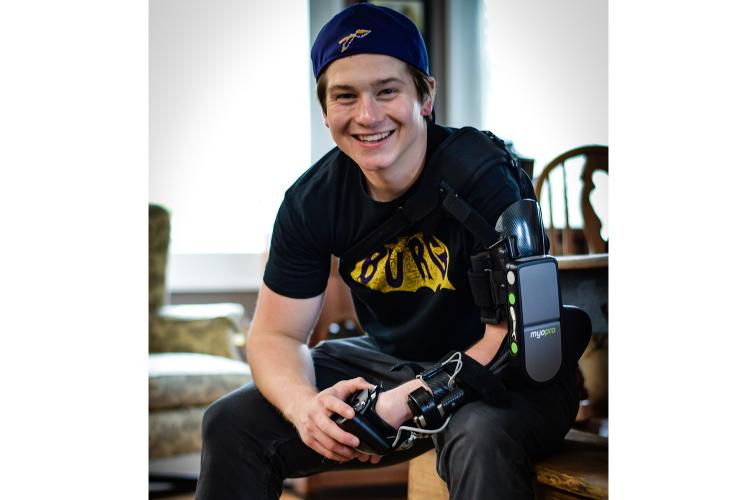
Providing mobility without adding strain to the rest of the body is important.
People who have gone through a stroke or traumatic brain injury often lose the use of one of their arms. A variety of physical therapy methods that are used, such as motor-skill exercise; range-of-motion therapy; and mobility training that incorporates aids such as canes, walkers, and braces. Myomo, a medical robotics company located in Boston, Massachusetts, has developed a myoelectric orthosis (powered brace) that is motorized to help patients use their impaired hand and arm again.
Myoelectrics is a technology that uses sensors to recognize and measure the electrical signals generated by muscles as they are contracted. These sensors, also known as electrodes, sit on the skin and use a specially designed controller to detect even the slightest muscle contraction. The controller triggers motor activation to correspond to the user’s intended movement. Using an array of sensors and motors, individuals can control multiple features simultaneously, such as those in the elbow and hand of Myomo’s powered brace.
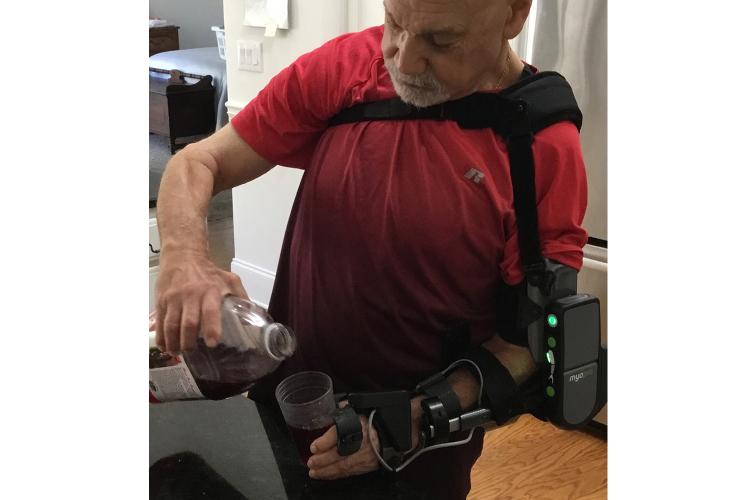
Figure 1: The MyoPro 2+ enables users to live more independently through the use of medical robotics.
The main goal of the company and its products is to re-enable a person who has lost the use of an arm by allowing users to regain as much function as possible in their arms and hands, allowing them to live more independently. Everyday activities such as pulling on one’s pants or shirt, holding a cup of yogurt with one hand while spooning the yogurt with the other hand, or holding a dinner plate while dishing out a meal are ways in which a normal life can be accessible again (see Figure 1).
Unlike replacing a limb, a common approach for an amputee, a motorized brace adds additional weight to the body. This means that an important design goal of the company’s MyoPro® 2+ myoelectric orthosis is to minimize weight while maintaining high performance output.
During the design and development process, the company was tasked with optimizing the power capabilities of the brace with its overall weight so that the wearer didn’t have to carry any more additional weight around than necessary, reducing shoulder and neck strain. Early in the design of the MyoPro 2+ Powered Orthosis, the company decided to use two precision motors designed and manufactured by maxon precision motor. The MyoPro 2+ operates by reading the weak electromyographic (EMG) signals directly from the surface of the patient’s skin without the need for implants. The weak signals activate the miniature maxon motors to move the arm and hand as intended by the user, with no electrical stimulation necessary.
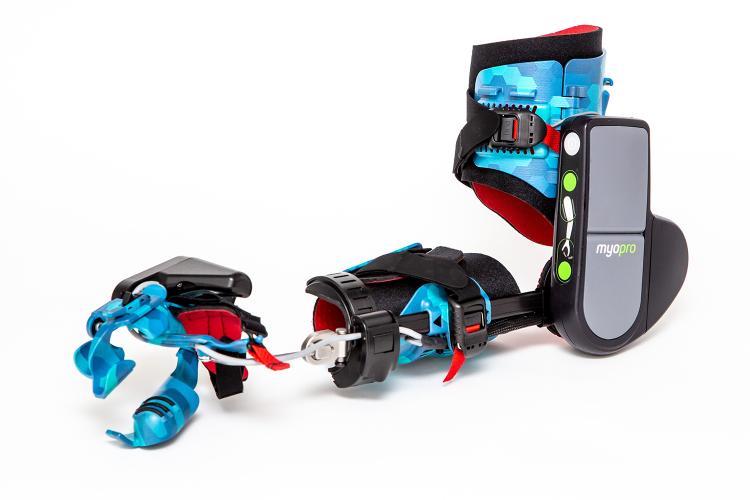
Figure 2: With a focus on comfort and lightweight, the MyoPro 2+ uses highly efficient, compact motors and controller technology.
The elbow joint on the powered brace is moved using the maxon DCX19 motor, which offers high power density, high efficiency, and smooth operation. These motors are available in a broad range of sizes from 6-35mm. Precious metal or graphite brushes and ball or sintered bearings. Along with the motor, the MyoPro 2+ incorporates maxon’s low-noise planetary gearhead to provide quiet operation to keep the brace as unobtrusive as possible during everyday activities (see Figure 2).
For hand operations, the patient’s index and middle finger are paired together for movement. This provides additional stabilization and gripping support. The motor used is the maxon RE13, which is also interfaced with a planetary gearhead. RE13 motors are known for their energy-efficient DC operation, providing over 90 percent efficiency. As with other maxon motor lines, these motors are offered in various sizes delivering a range of torque and speed requirements to the user.
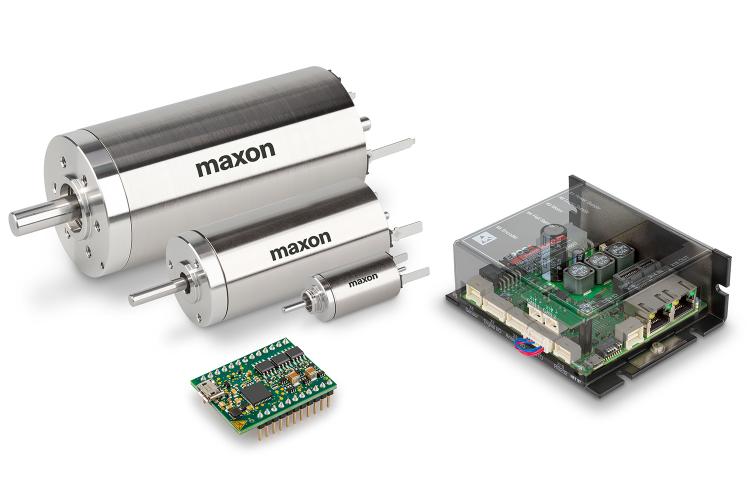
maxon’s DCX brushed motors and EPOS and ESCON positioning controllers are readily available online.
During the prototyping stages for the MyoPro 2+, Myomo uses maxon’s EPOS 50/5 and ESCON 24/2 controllers as a flexible design platform to measure and tune the operation of the brace. Once the motor characteristics are correctly
aligned and offer the right operational functions and specifications, the company integrates its own lightweight circuit board using the control parameters developed during prototyping. The circuit board’s smaller, more compact, and lighter weight allows the company to fit the control unit near the elbow joint without getting in the way of arm movement.
The MyoPro is recommended by physical and occupational therapists, prescribed by a physician, and delivered by orthotics and prosthetics professionals on a case-by-case basis. Currently, the Myopro 2+ is the only marketed medical device that can restore an individual’s ability to perform the activities of daily living, such as feeding themselves, carrying objects, and doing household chores. Some patients have been able to return to work, while others learn to live independently, reducing the costs relative to additional care and rehabilitation.