What is it all about?
The project which will be realized in cooperation with the YEP is an active rear wheel steering system (RWS) for a Formula Student Electric race car. Thus, two independent actuators integrated in the rear tie-rods set a steer angle of the rear wheels up to 3° per side. This helps to improve both the handling and the overall driving stability of the car.
How does it work?
The actuator itself is based on an electric driven spindle drive, which converts the rotational movement into a linear movement. To gain enough actuating power, a 200W Maxon EC-4pole motor is fitted to the RWS. A Maxon GP 32 C planetary gear is connected to the motor to provide enough torque. It drives the spindle nut through a belt drive. The power is supplied via the internal 24V LV-electrical system of the race car. To set the right steer angle, two Maxon EPOS2 position controls together with Maxon HEDL encoders are used, whereas the race car’s internal controls calculate the needed steer angle.
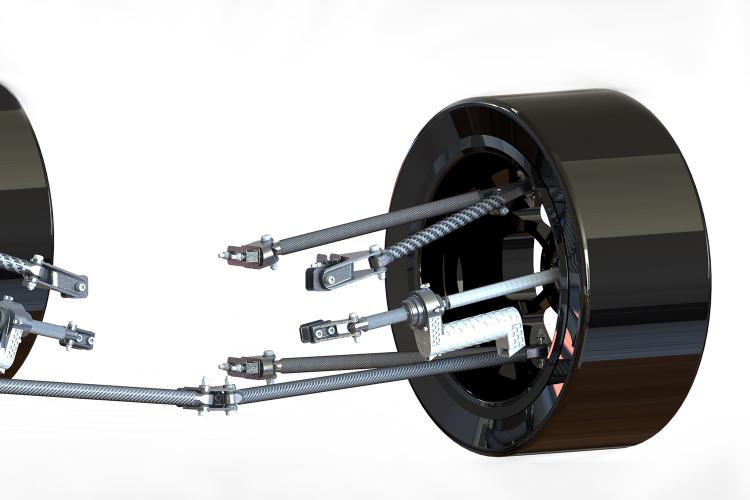
Why Maxon?
As the RWS will be fitted in a race car there are three big issues the designer has to cope with:
Firstly, the electric components have to have enough power to set the desired steer angle in every driving situation. Secondly, the components have to be light and compact, as Formula Student is a design competition where low weight is almost everything. Thirdly, the system has to work reliably. The rear wheel steering system’s safety relevance is very high in terms of handling stability. Failures may have fatal consequences. For that it is important to have electrical components which fit together.
Maxon provides all three of that: The motors are powerful and compact, the range of gearboxes available is wide and they do have position controls and sensors especially made for their motors. There may not be any compatibility problems within the used components. That makes Maxon kind of unique and helps finishing projects successfully.