Deep-sea drilling. Mars rovers. Insulin pumps. Formula 1 cars. Surgical robots. Hand prosthetics. This is only a small selection from the thousands of applications in which maxon’s drive systems provide their power, precision, and robustness. However, before our DC motors, gearheads, sensors, and controllers are supplied to the customer, they have to withstand an array of abuse. During the development phase, we push our products to the maximum limits.
For example: extreme cold and heat
The biggest enemy of the drive system in a Mars rover is the cold: On the planet, temperatures can drop to -130 °C. In contrast, the Solar Orbiter, a space probe that ESA is building on, will have to withstand temperatures of up to +500 °C during its journey towards the sun.
In our test lab, we test and stress motors in temperature test chambers. Repeated temperature cycling is also performed to simulate the behavior of the drives under conditions with extreme temperature fluctuations.
For example: shock and vibration
In airplanes our motors are subjected to constant vibrations during flight. During each landing or in the event of strong turbulence, they also suffer mechanical shocks. However, that’s still nothing compared to the unpleasant conditions awaiting systems in the drill heads of the extractive industry or in space.
In our modern test systems, we can analyze the potential damage that such stresses can cause (e.g. accelerations of up to 4,000 g – ideal for developing drive systems that will be sent on a journey through space).
Not all our drive systems have to withstand spaceflights with shock load and vibrations at freezing temperatures. Nevertheless: Our catalog products are also subjected to extensive qualification tests during the development phase.
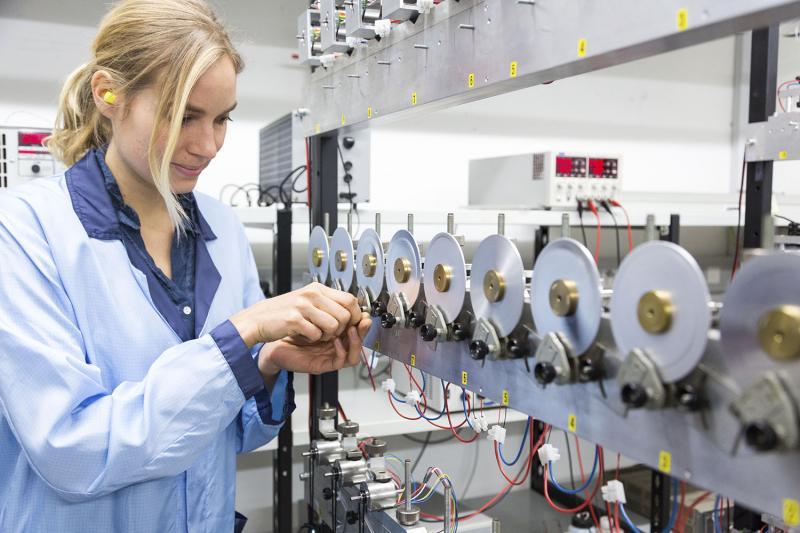
Our catalog products are subjected to extensive qualification tests.
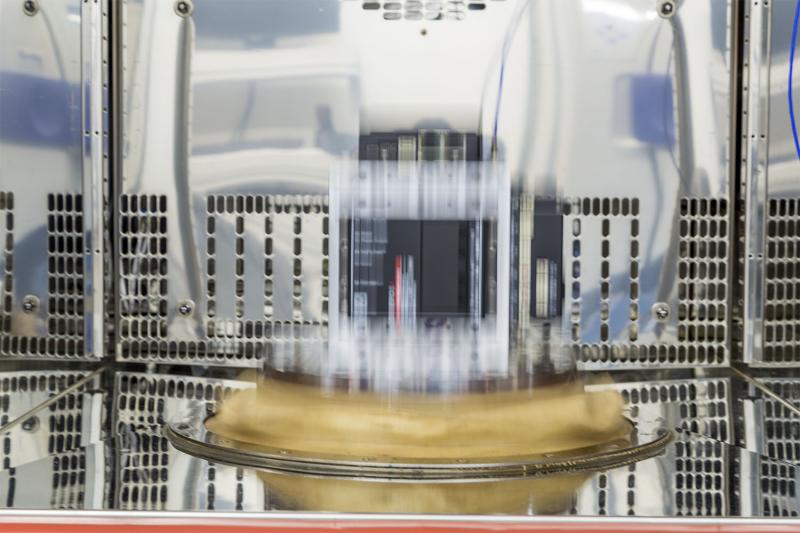
In our modern test systems, it is possible to generate vibrations with frequencies from 5 to 5000 Hz.