Dynaflo, Inc., designer and manufacturer of OEM diaphragm vacuum pumps and compressors, Dynaflo, has a history of creating custom solutions to meet the needs of highly specific applications. The company addresses every challenge by analyzing a range of elements including size, output, power consumption, material needs, and whatever else is important to provide the solution that delivers the greatest benefit to the user.
While engaging in a new application to help with prosthetic limb attachment—primarily for leg attachment—they first checked to see if any of their existing vacuum pump platforms would work. Often, they are able to make minor adjustments to a previous design that will solve the problem at hand. For this application, the company created a new design, their 2000 series vacuum pump, which provides the highest vacuum levels currently available from a diaphragm pump of its size (see Figure 1).
Generally, Dynaflo products are designed to maximize efficiency using up to 60 percent less power than leading competitors. They do this through a number of proprietary approaches, one of which is to incorporate low wear components such as high-quality bearings, specially formulated and processed materials, and standard and semi-custom DC brushless motors that provide extremely high performance for long life cycles.
Since the pumps designed by the company are oil-less the devices operate without risk of contamination. The unique design of the pumps themselves take advantage of the company’s distinctive approach whereby the diaphragm is bent rather than stretched. This strategy minimizes the force required to displace the diaphragm, maximizes its efficiency, and reduces the power needed for operation. This combination of benefits was ideal for the prosthetic limb attachment application.
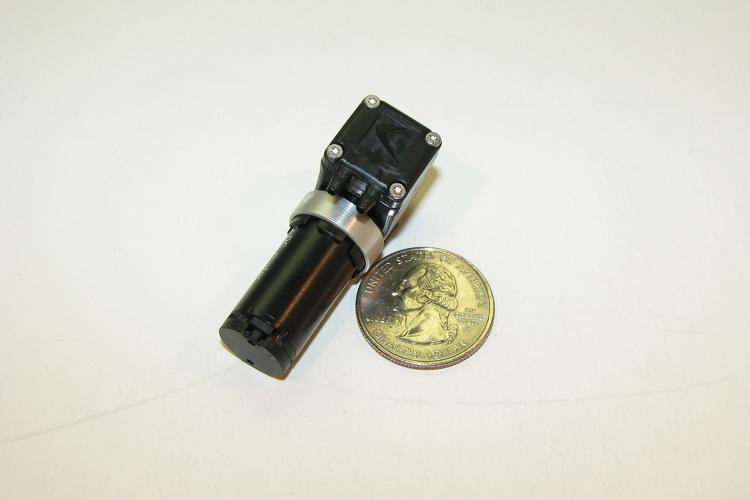
Figure 2: Used to hold prosthetics on—employing vacuum instead of belts and straps—the Dynaflo pump needed to start operating while under load
Although some prosthetics interface with a locking pin and prosthetic sock or cushion, many still incorporate straps and belts which are cumbersome to attach as well as to maintain snugness over time. Plus, the materials used often cause scraping and chafing of the leg where attached. The solution was to provide a suction-based attachment system. Since Dynaflo didn’t have an off-the-shelf unit that came close to the needs of the application, they decided to create a completely new product from scratch. The miniature diaphragm vacuum pump design that the company’s engineering team came up with required a number of key specifications in order to work properly (see Figure 2).
A major concern for the team was how to keep the prosthetic on without losing even partial vacuum while in use. This potential situation could result in the limb coming off unexpectedly, and likely causing harm to the patient. To solve this problem, the team knew that the pump had to be able to start up while under load. In order to do this, the motor used for the pump had to deliver very high torques whenever necessary. The pump was also challenged to reach -27 Hg in a few seconds. Add to these requirements that the pump needed to be small, at less than a half-inch in thickness, and final design parameters became very specific and difficult to achieve.
The Right Motor
The engineering team at Dynaflo selected the maxon RE16 motor to power its pump (see Figure 3). RE motors are precision brushed DC motors that incorporate ironless windings and precious metal commutation along with rare earth magnets to assure precise control whereby the current draw was proportional to the torque requirements of the application. The motor solution for the pump provided more than 90 percent efficiency while delivering the fine rotary motion needed for proper operation.
The motors use graphite brushes at 2.5 watts of power. The RE13 has a 13mm diameter and has a nominal torque rating of 1.44 mNm and can operate at speeds up to 10,600 rpm. The RE series motors from maxon were literally the only motor available for such a sensitive and important application. Dynaflo was able to incorporate the motor into their design with relative ease. In addition, the RE motors was a low noise solution.
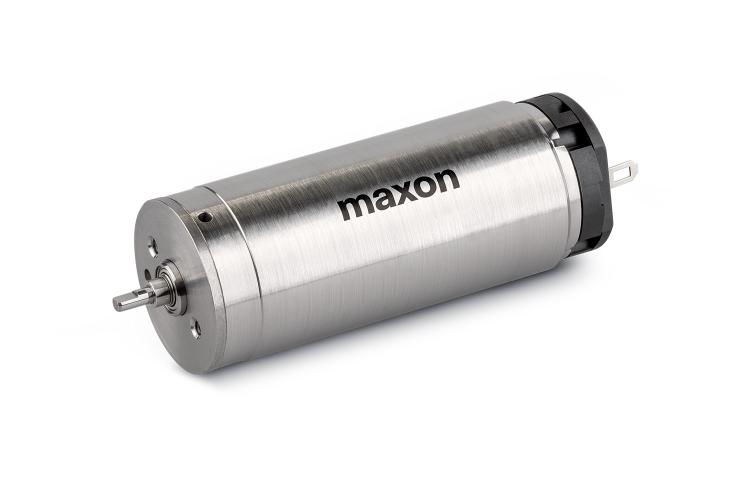
Figure 3: The RE16 designed and manufactured by maxon offered the torque needed to start the vacuum pump while under load.
Based on maxon’s technical expertise and attention to design and manufacturing details, the motors provided the pump application with long life cycles. This was particularly advantageous because the company required a motor that would help with the serviceability of the pump over the long haul. Given that the bulk of the cost of the pump was in the motor, it was important that the company was able to refurbish the pump while re-using the motor. The long life of the maxon motor has allowed Dynaflo to update and refurbish thousands of pumps with a new head and valve and be put back into service using the same motor.
Conclusion
The pump used in the prosthetic leg attachment application relied on the right motor for proper operation. Creating a vacuum in such close proximity of a human body can generate a potentially harsh condition if done improperly. The Dynaflo team of engineers were careful to select and use the right components to produce a safe and serviceable vacuum pump that would last for years. This resulted in a product that was easy to use and easier to implement by the end user.