Motors operated at the rated torque limit can get very hot. In continuous operation the winding can reach 155° resulting in a housing temperature of some 120°C. No surgeon would like to operate with a hand-held tool not even at half of that temperature. Neglecting friction, there are two main sources of power losses – and hence heating – in motors.
Joule power losses
The Joule power losses are linked to the current, i.e. the required torque load. As it is well known, these losses increase with the square of the current. High currents close to the nominal value will result in temperatures unbearable for humans to touch; running the motor at currents of about half the nominal current results in moderate temperatures (typically below 50°C) that matches the sensitive human skin.
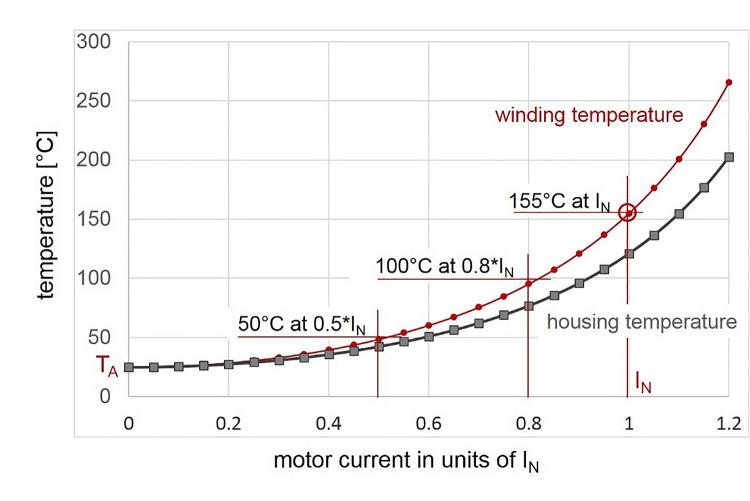
For motor selection, this essentially means: go for an oversized motor! Be aware however, that we consider here continuous operation where the maximum temperatures will only be reached after some 10 minutes. In hand-held tools one usually has intermittent operation that can expand to 30 minutes and more. The heating is according to RMS average load including dwell times.
Iron losses
The iron losses are related to speed. Eddy current losses increase with the square of speed, heating up the motors simply when rotating - even in no-load condition. In hand-held tools, this can be a problem for grinders and drills that operate at several ten-thousand rpm. Such high speed motors need special design precautions to limit eddy current heating. Typically, they are made with a low number of magnetic poles, a slotless winding, ultra-thin back iron foils made of special low hysteresis materials. The maxon ECX SPEED series for instance combines these features.
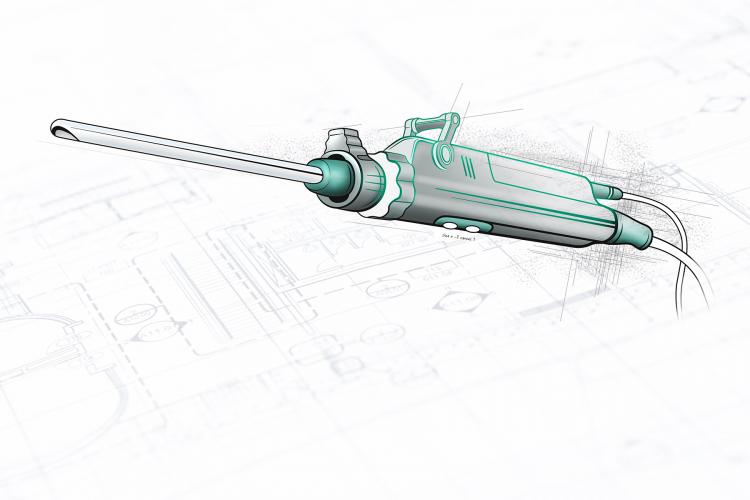
Medical shavers are used by surgeons for operations on knee or shoulder joints, where they remove tissue and cartilage neatly and accurately.
PWM driver and inductance
It turns out that heating is not only a question of torque, speed and design but also of the driver. Recently, a customer complained about the high temperature (80°C and more) of his motor even when driven at no-load conditions. Upon investigating the case, we found out that the driver and the supply voltage had a major effect.
Slotless windings have a very low inductance resulting in a very low electrical time constant (see my other blog on inductance). The current will react very fast; that’s good for dynamic behavior. However, when driven with pulse-width modulated (PWM) power stage (as most controllers do) the motor current is able follow these rapid voltage changes giving rise to a considerable current ripple. Be aware that the PWM voltage and the current ripple have no effect on the mechanical response of the motor. The motor reacts according to the average current and voltage values.
The current ripple peaks, however, heat up the motor. Counter-measures for minimizing the current ripple are:
- Reducing the supply voltage of the PWM driver if possible by the speed requirements of the application.
- Increasing the PWM frequency to allow less time for the current ripple to build.
- Adding an extra inductance – a motor choke - in series to the motor lines in order to increase the electrical time constant and to dampen the current reaction.
maxon controllers take the low inductance of maxon motors into consideration. They work at high PWM frequencies of 50 to 100 kHz and are equipped with sufficient additional inductance for most motors.
The customer heating problem was easily resolved just by replacing the old over-dimensioned controller with a new ESCON controller. The ESCON solution was made for lower power with a larger built-in inductance and operates at a higher PWM frequency than the old controller. The largest effect on temperature, however, was gained by reducing the supply voltage close to the minimum value needed.
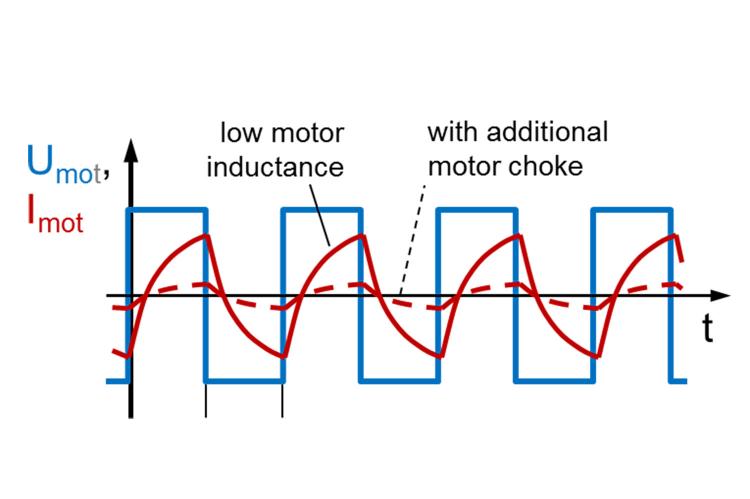