Up to 2500 g – it is hard to imagine the enormous forces that act on an object under this kind of acceleration. Or in this case, on a maxon motor drive system. For comparison, an astronaut experiences gravitational acceleration of around 3 g to 4 g during launch. The average maximum in aerobatics is 8 g.
Let’s get back to Earth though. In the maxon motor development lab in Obwalden (Switzerland), motors and gearheads are very thoroughly tested. The laboratory has all kinds of technical equipment, such as vacuum chambers, various climate-temperature systems, and a mechanical impact tester. This last unit generates the extreme g-values mentioned above to test the motors’ impact resistance. The device was purchased specifically for maxon HD (heavy duty) motors. Currently, the drive systems for the ExoMars mission – or to be more precise, the motor-gearhead combinations for the wheel drives of the rover – are being tested.
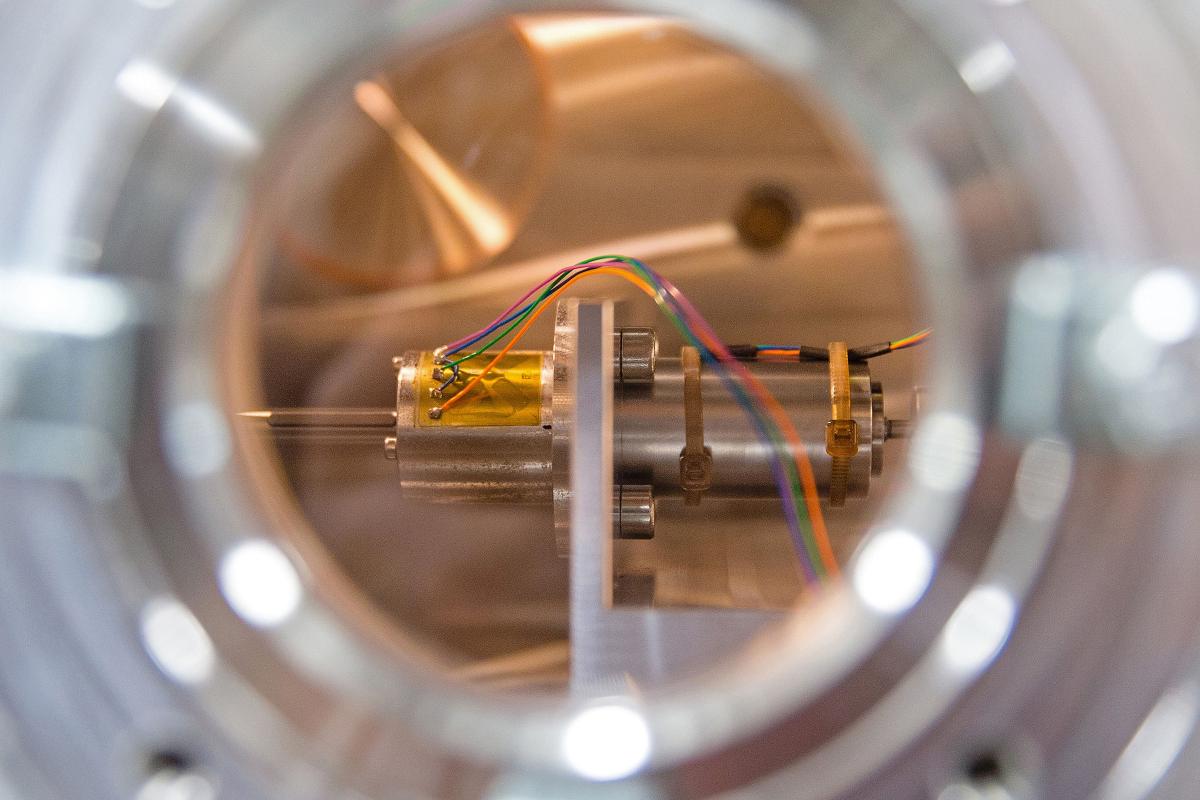
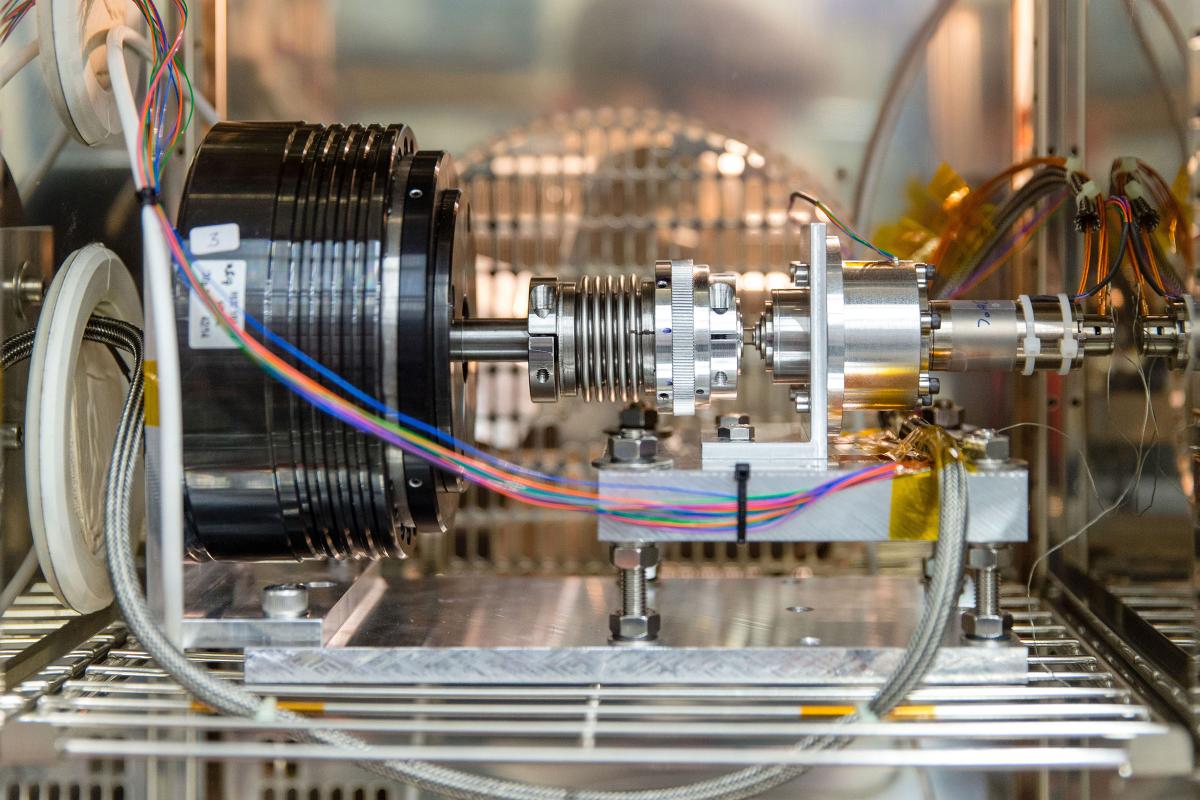
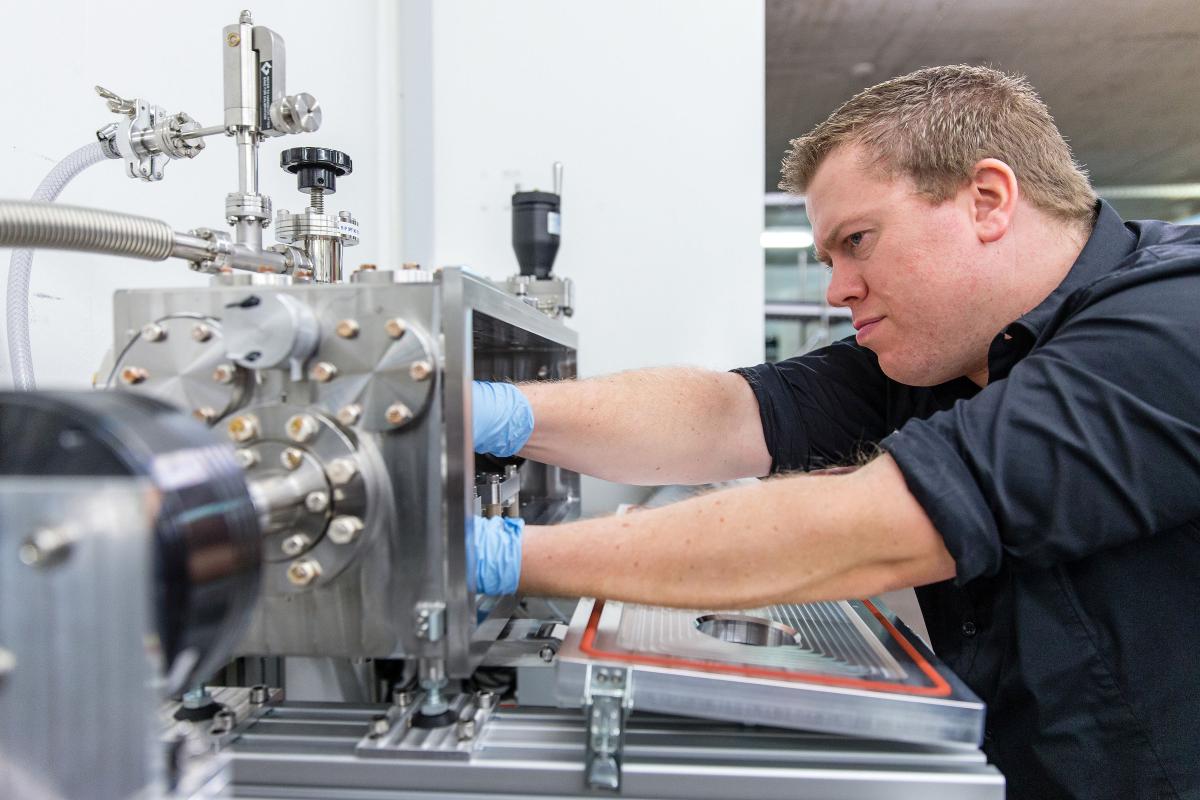
Two years and longer service life
The laboratory itself is already impressive. The endurance testing room even tops it, with its endless rows of racks, all loaded with different motors and controllers. The service lives of more than a thousand motors are tested here. Some drives run for more than 20,000 hours. The tests are checked almost daily by the laboratory’s development engineers.
Oil immersion for motors
Some motors are immersed in oil baths of up to 200 ° C a particularly hard test. These are maxon HD drives that have been developed specifically for operation in oil. With slight modifications, they can also be operated in air at 200 ° C. One field of application is deep drilling. Only HD drive systems are able to withstand the high temperatures, extreme pressures, and strong vibration in this environment. Continuous testing is critical to ensure that these drives work flawlessly at depth.
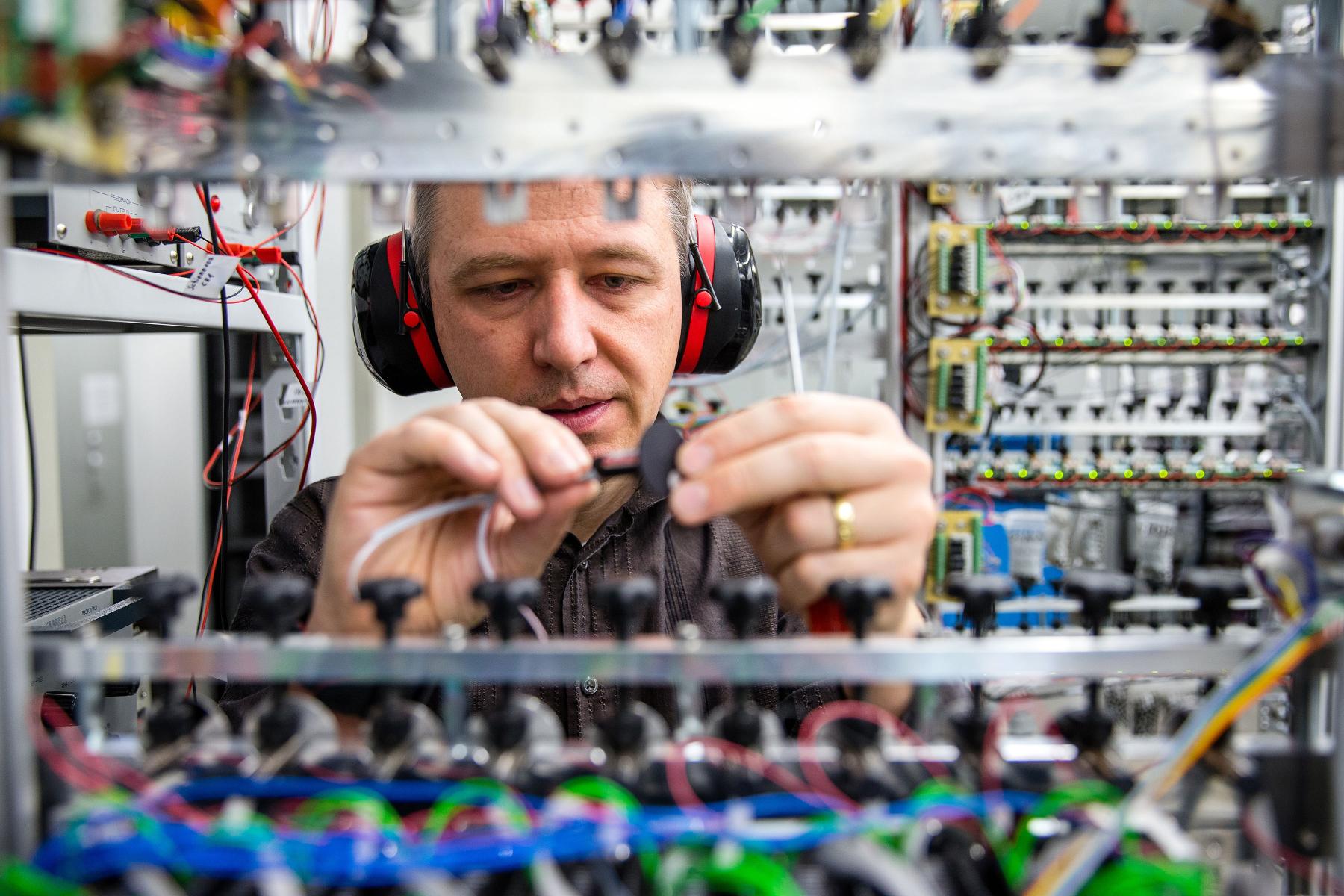
The robust maxon motors are also suitable for use in the aerospace industry. The lab therefore has a vacuum chamber capable of simulating the characteristically thin Mars atmosphere, in addition to generating high vacuum. “In the chamber, the motors are exposed to exactly the same environmental conditions as on the surface of Mars. This is the only way we can guarantee to the customer that our drives are going to work flawlessly in this remote location”, explains Nico Steinert, development engineer at maxon motor. The high vacuum unit with its futuristic appearance was built specifically for the ExoMars mission. It is used to test the motors and gearheads that will be used on Mars in 2018. The chamber is able to generate pressures of < 10–6 mbar and temperatures between –150 and +200 ° C.
The in-house development lab enables maxon motor to thoroughly test its drive systems to detect and remedy potential problems early on. The development of our drive systems is thus an ongoing strive for even more excellence, and quality is guaranteed at all times.