1. Logistics
An essential component of the goods cycle, logistics brings together a wide range of stakeholders. Transport, warehousing, product design and primary packaging, handling, outer packaging... In an economy that is increasingly centered around the exchange of goods, logistics operations need to be agile and efficient. The efficiency levels of logistics and the supply chain have become decisive factors in companies’ competitiveness. And the use of AGVs and AMRs (autonomous mobile robots) is becoming vital in this context. These autonomous vehicles have the advantage of offering major potential to transform logistics chains. They also represent a strategic interest for efficiency gains.
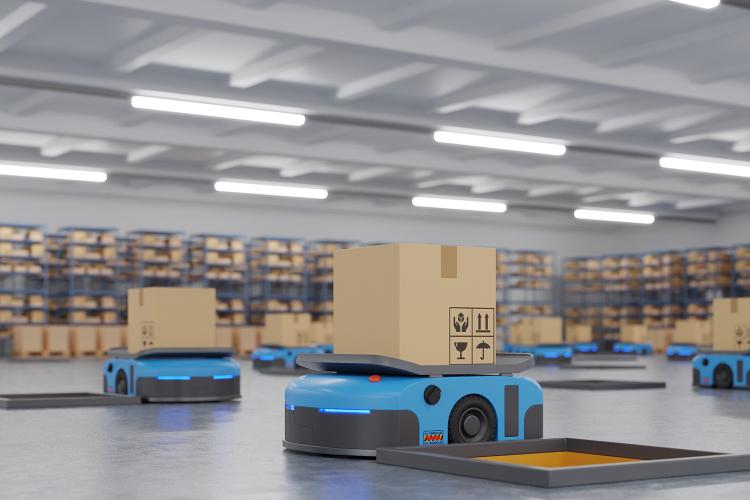
Moving goods, helping with order preparation and even managing inventories: equipped with powerful sensors and artificial intelligence, AGVs are now able to perform many tasks within warehouses. Their compact size in particular addresses the challenges posed by e-commerce. There is a need for faster order processing in this booming sector. Consumers are demanding: 24-hour delivery is becoming the norm. To achieve this, proximity to large cities is essential. But, the closer a company moves to an urban area, the higher the rents are per square meter. Therefore, most logistics companies tend to opt for high-rack storage solutions. In order to evolve in this confined environment, the manufacturers of AGVs must therefore offer compact and functional robots which are able to move vertically and carry heavy loads.
- See also : The 5 key points when motorizing an AGV
Choosing a compact motorization is therefore essential for meeting the challenges of the sector. With a diameter of just 56 mm, the IDX motor perfectly addresses the challenges relating to performance and compact size – which are crucial factors in the logistics and intralogistics sector.
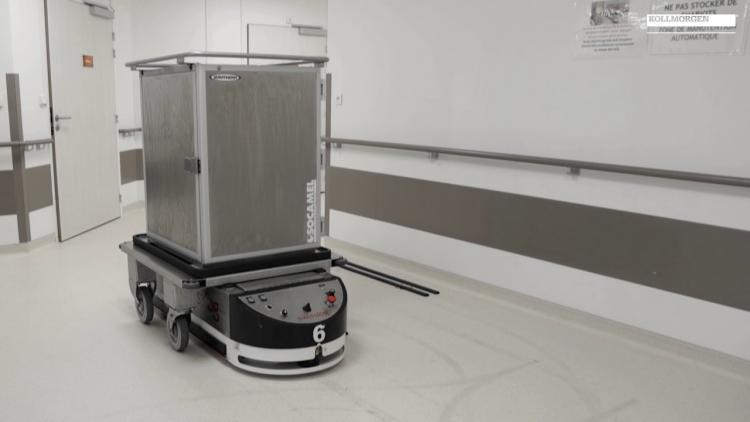
2. Medical industry
To make the lives of health care staff easier and completely avoid the risk of contamination in the event of an epidemic, AGVs are also deployed in hospitals. Capable of transporting meals, laundry or waste, and even delivering medication to patients, robots are also proving useful for moving heavy loads. During the Covid-19 crisis, many hospitals across the world have called upon their services. In Italy, robots were able to collate information on patients’ state of health, while the Navy Firefighters Battalion in Marseille acquired an AGV featuring a decontamination module.
However, the hospital sector did not wait for this global pandemic before harnessing the potential of AGVs. Since 2012, Nantes University Hospital has been using cobots to deliver fifty or so flexible endoscopes per day in intensive care units and endoscopy departments as well as operating theaters. Capable of taking the elevator and moving autonomously around the corridors, these robots collaborate with humans, traveling around 1,400 km each year and transporting more than 25,000 endoscopes. This was a worthwhile investment for the University Hospital, which also values the high level of security provided by the locked cupboards on these AGVs. The drive systems in these machines must be network-connected to ensure they can undergo remote maintenance while also offering a level of IP protection, since they come into regular contact with disinfectants.
The maxon IDX motor with integrated electronics is ideal for all of these applications. It is compact and offers high performance as well as standard IP65 protection.
3. Transport
Although the automotive and aeronautical industries have suffered as a result of the recent coronavirus crisis, AGVs are still drivers of the transport sectors and are key to boosting productivity in these sectors.
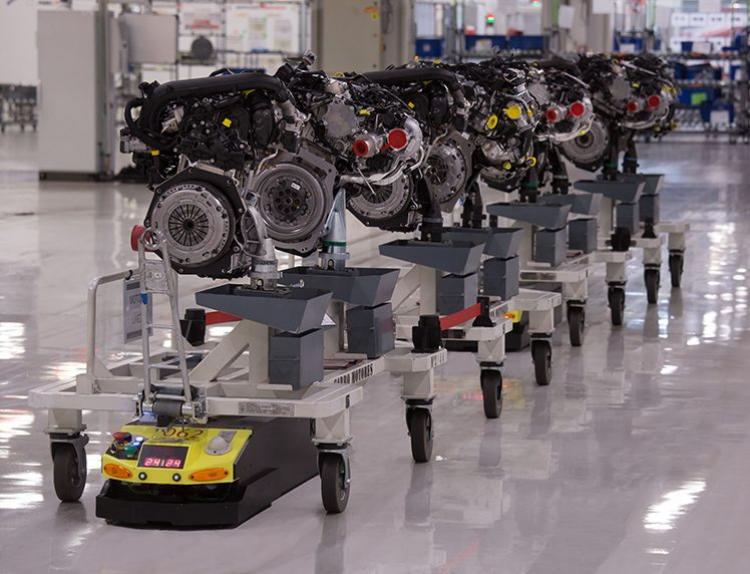
-
Automotive
The first automated guided vehicles were developed in the 1950s for the automotive industry. Seventy years later, this historic sector is still a growth area for AGVs. Electric, hybrid and thermal engine cars… In an industry which must increasingly expand its options while adapting to customers’ changing opinions, flexibility is key – now more than ever. It has even become a strategic challenge. Although the assembly line model instituted by Ford proved worthwhile in the past, it does not allow companies to easily adapt to changes in production. So it's out with Ford's assembly line and in with a modular assembly system, where AGVs have a pivotal role to play.
This was the choice made by car manufacturer Audi at its factory in Bavaria, where the assembly line has been replaced by assembly stations with two or three operators. Placed on an AGV, the vehicle is transported from one station to the next during the assembly process. The AGV chooses the optimal route based on an algorithm. The entire process is synchronized from a control room where all the production data are analyzed. By deploying the modular assembly system, the Audi Group is expecting to see a double-digit increase in productivity.
Audi is by no means alone. The automotive industry is brimming with push robots, shelving pullers, autonomous lifting carts and other smart mobile shelving systems which are capable of turning over when they are empty to reveal the correct parts to the workers. Now equipped with a multitude of sensors, cameras, radars and laser detectors, AGVs move around car manufacturing plants and make the workers’ lives easier.
With the aim of making huge time and space savings, the PSA Peugeot-Citroën Group has also adopted AGVs in its production chains. Perfectly integrated into the LEAN production system, these autonomous guided vehicles are able to load up in the logistics zones before returning to the assembly line, where the operators take care of assembling a sub-unit, such as the engine build-up.
For the last few years, the automotive industry and the big marketplaces have also seen the development of crawler AGVs, which are able to slide underneath a cart or underneath a rolling cabinet, before grasping it via a hook system and moving it. The crawler AGV effectively addresses the challenges of restricted spaces, as it can move into more confined spaces by optimizing the length of the AVG and that of the cart.
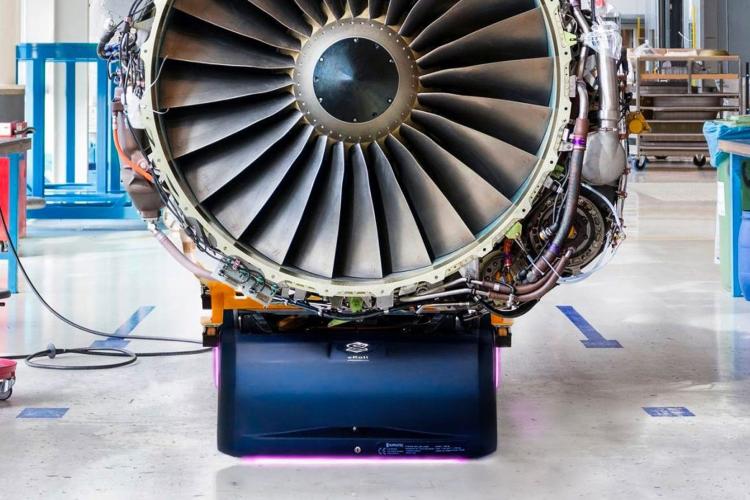
-
Aeronautical industry
Modernizing the industrial system, supporting competitiveness, meeting the challenges of production ramp-ups… Similar to the automotive industry, aeronautical companies have incorporated automation in their assembly lines through the use of AGVs. Airbus recently commissioned a highly-automated digital assembly line for the fuselage structures of its A320, A321 and A321R aircraft. In this high added-value sector, autonomous guided vehicles enable the transportation of heavy loads such as fuselage parts, although other, more innovative projects are also being implemented.
In order to speed up processes and avoid unfavorable body positions, which can cause problems for the technicians, the industrial integration network of Vinci Energies, Actemium, has developed a solution for automating the inspection of aircraft engine assembly. Perched on an AGV, this robot is able to compare the digital reference model with the completed assembly.
In terms of maintenance, robots are very useful for detecting the exact origin of a breakdown or a malfunction. Thalès DMS France uses an AGV that is able to move autonomously underneath an aircraft while emitting electromagnetic waves. Using this AGV, a mechanic can check the parameters in the cabin and analyze sensor damage in order to schedule different maintenance operations.
As for design, the BA Systems Group has developed Asimov, a cobot that is able to perform assembly operations inside an aircraft structure. Designed for assembly of the Airbus A380, this AGV knows how to position itself correctly in order to accurately print the form and the reference of the part that is to be assembled by the operator.
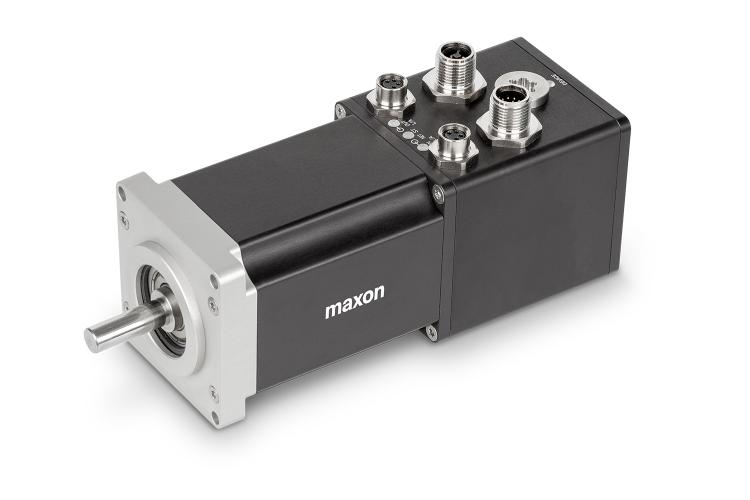
From logistics and aeronautical engineering to the medical industry, there are huge development opportunities for AGVs. In order to meet the challenges of these sectors, you must be able to offer vehicles with compact and powerful drive solutions which are also easy to maintain. Bearing in mind these requirements, the teams at maxon have developed IDX, a range of motors which are modular, safe and easy to configure, to satisfy all of your drive needs.
To find out more about the IDX, visit idx.maxongroup.com