Vision Robotics Corporation (VRC) and its subsidiaries develop robotics systems for a wide range of applications using the latest technologies by employing vision-based AI. This includes mapping, localization, and navigation systems as well as machines that interact with real world objects. The AI involves various machine learning techniques including deep learning and modern controls for motion components such as dynamic arm control. The company’s robust and cost-effective approach to solutions enables their robots to autonomously create three-dimensional maps of unknown areas of interest whether this is mapping a building or modeling a grapevine. The maps and models enable robots to perform a myriad of tasks intelligently and accurately whether it is vacuuming a floor or pruning a grapevine.
The experience and creativity the Vision Robotics team brings to its customers makes them excellent partners in developing robotic systems. The next generation robots require mobility and the ability to interact with the changing world. VRC’s software and supporting technology enable robots to explore, understand, and work autonomously and reliably in complex environments. Coupling VRC’s technology with the current generation of high-performance, low-cost microprocessors, solid-state cameras, high-tech motors, and other essential components make affordable, high performance, vision-based mobile robots practical.
Design Challenges for Crop Cultivators
Cultivators traditionally comprised blades or other implements towed behind a tractor to break up the soil in a field. In the recent past, cultivators and other weeding machines incorporated a secondary side shift so that its accuracy was not tied to the quality of the driver or the planting—the weeding plow stayed relatively on target with the plant even if the driver weaved slightly. Even still, there was a minimum clearance required between the plow and the crop so it didn’t cause leaf damage because of the tolerance for these large systems. Also, these traditional cultivators did not work the soil between the plants along the row.
Inline cultivators have existed for a few years. Competitors use a hydraulic control system that operated symmetrically. These systems required that the width of operation and speed of the cultivating blades as they opened and closed had a specific set point that was determined up front. Because the blades on both sides of the row opened and closed symmetrically plants could easily be damaged if the plants or field conditions strayed too far from typical (see Figures 1A and 1B).
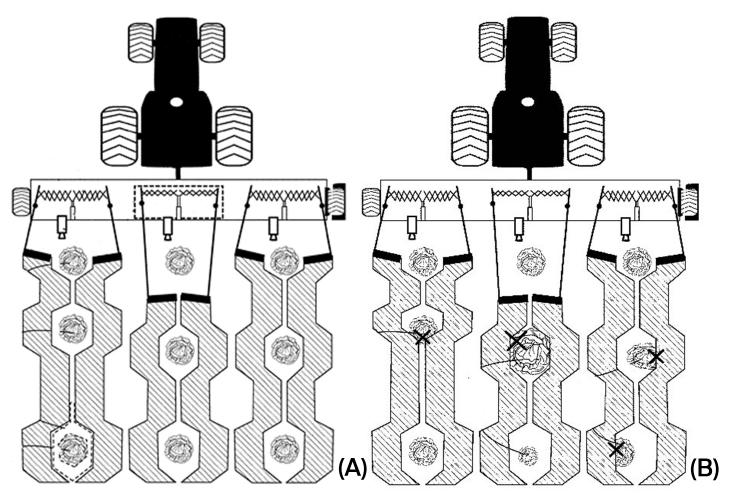
The VRC Crop Cultivator
The latest design from VRC took advantage of using independent electric motors for the cultivating operation. This meant that the blades on each side of the plant could make a completely custom contour, which enabled better precision around the plants (see Figure 2). This application strategy meant that the VRC team needed to find motors that had the torque and acceleration required to handle such tough operating conditions for long periods of time and in every imaginable environment. In addition, the company need the AI and neural nets capable of enabling the system. In this case, the company lumped the plant detection into the deep learning bucket, which made it simpler to create a training set of images of both the crop and the weeds.
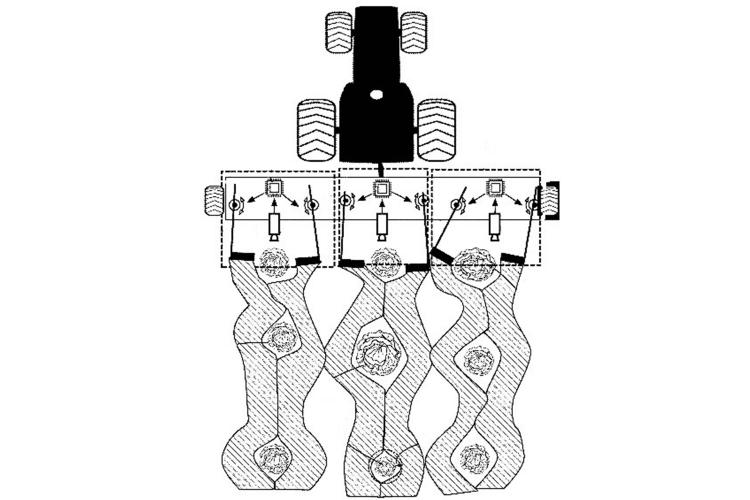
Figure 2: The added value from using an electric motor driven system instead of a hydraulic system can be seen by the way the independent arms are better able to maneuver around the plant.
The VRC Cultivator is an in-line cultivator that aerates the soil as it weeds between rows of plants whether lettuce, broccoli, cauliflower, or any other. The system is trained on 100s to 1000s of photographs of healthy plants, dead plants, and common weeds to create the perfect algorithm for the operation. The system incorporates a vision system to capture images of plants. The camera system automatically “recognizes” different plant sizes, types, and soil coverage under a wide variety of lighting conditions. Images are processed in real time by the AI deep learning circuitry. Deep learning is used instead of other machine learning techniques because of its flexibility and ease of adapting for future conditions. The system identifies each plant as well as its precise size and location for both the crops and weeds. The resulting algorithms converts these inputs into timing data used for dynamic arm control of the precision operated blade actuators (see Figure 3).
Software is used to calculate the open and close trajectories required for each plant group. The operator determines how much clearance to give the blades around the plants including reaching under the canopy. The system can operate up to 3 mph but is typically around 1 mph. The operator determines the speed based on environmental and crop conditions. The faster the speed, the more and further dirt is thrown, which can damage or contaminate the crop. For example, lettuce grows leafy and close to the ground. Too high a speed can cause dirt to collect on the plant unnecessarily, therefore a lettuce weeding robot must operate slowly enough as not to kick up a lot of dust. Typically, a lettuce weeding machine can operate at about one mile per hour and still provide clean healthy product in its wake.
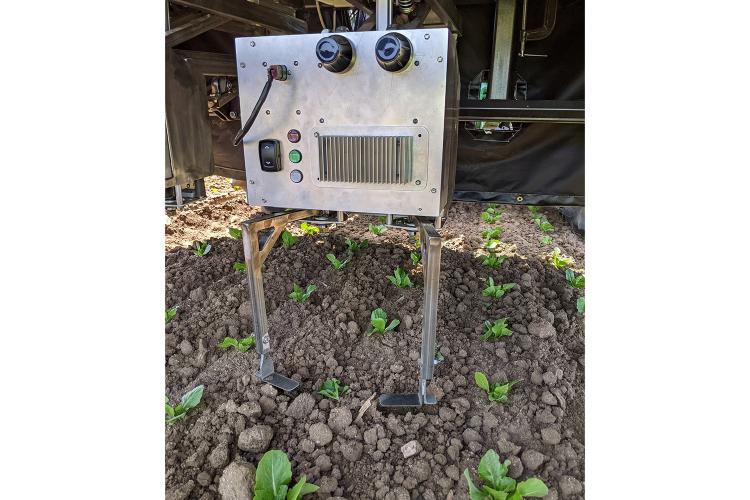
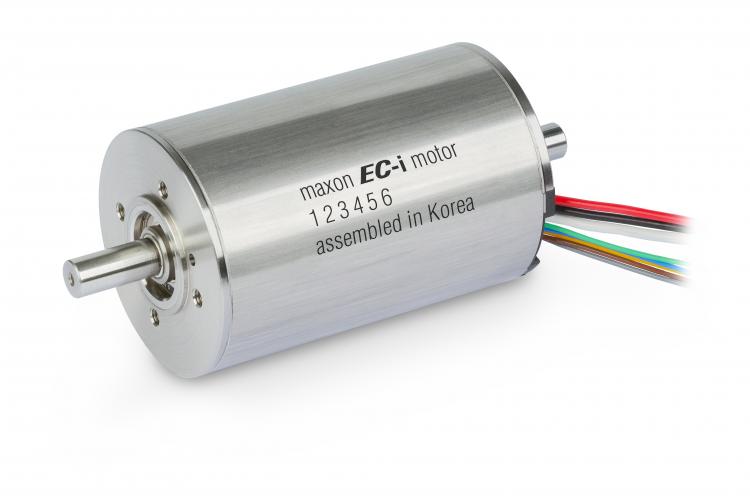
maxon’s brushless EC-i motors with iron windings offer a very high torque density and a low cogging torque. The multi-pole internal rotor is extremely dynamic. Its solid design with a steel flange and housing make this motor suitable for a wide range of applications.
Motion System Components
As indicated above, independently operated electric motors were incorporated for the weeding operation so that the blade on each side of the plant could make a completely custom contour around the plant, which enabled better precision during operation. The knife blades could get closer to the plant and provide a cleaner removal of weeds for a significant performance advantage over other systems. The team’s application strategy meant that they required motors that had the torque and acceleration necessary to handle such highly dynamic motion.
The motors selected by the VRC team included two EC-i 52 motors designed and manufactured by maxon. The EC-i 52 is a 420 watt electronically commutated brushless DC motor with a built in Hall sensor for feedback. The motors react quickly and are able to guide the knife blades close to each plant without harming it. Key features that set maxon's electronically commutated EC motors apart include their excellent torque performance, high power, extremely wide speed range, and unrivaled service life. The outstanding controllability of the motors permits the creation of high-precision positioning drives.
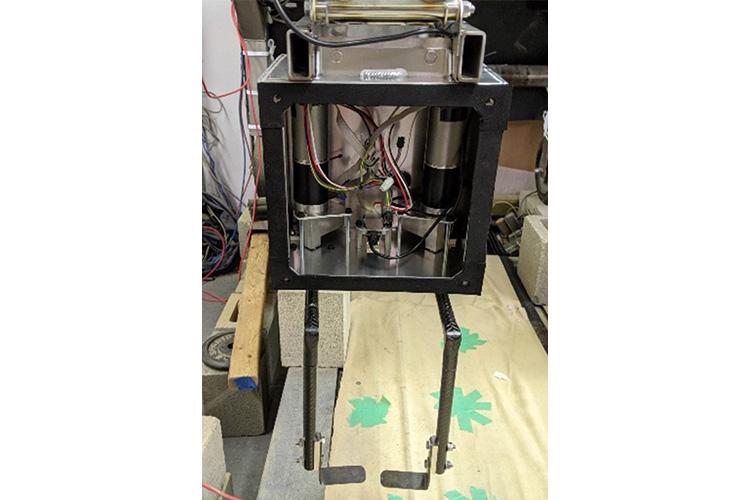
Figure 4: Notice the location of the two high-torque EC-I 52 maxon motors and GP52 gearheads inside the enclosure for the VRC cultivator.
In addition to the motors, the VRC cultivator’s motion system incorporates two GP52 gearheads also designed and manufactured by maxon (see Figure 4). The gearheads are required for the high torques that are needed to break up dirt clods while in the process of weeding around plants. These ceramic components offer up to 30 Nm of torque depending on which model is used. Design calculations needed to consider the length of the robotic arm, the speed of operation, and the torque specification necessary to operate through the ground during its normal functioning.
Conclusion
Robotics Vision Corporation approaches each application with creativity and experience. When they needed to improve on the capabilities of the latest cultivators for commercial farms, they turned to maxon. maxon components were able to meet the high standards for torque and speed that allowed the company’s cultivator to maintain its precision and accuracy while in operation, as well as to withstand the harsh environments found in the commercial farming business.