“We initially purchased the laser for a project where the tiny components were almost impossible to produce with mechanical means. Today the laser is our all-rounder with which we were able to apply several principles normally used in steel processing to ceramics – and to practically any other material,” Michael Streicher summarizes the benefits of the laser. Streicher heads the laser processing department at maxon.
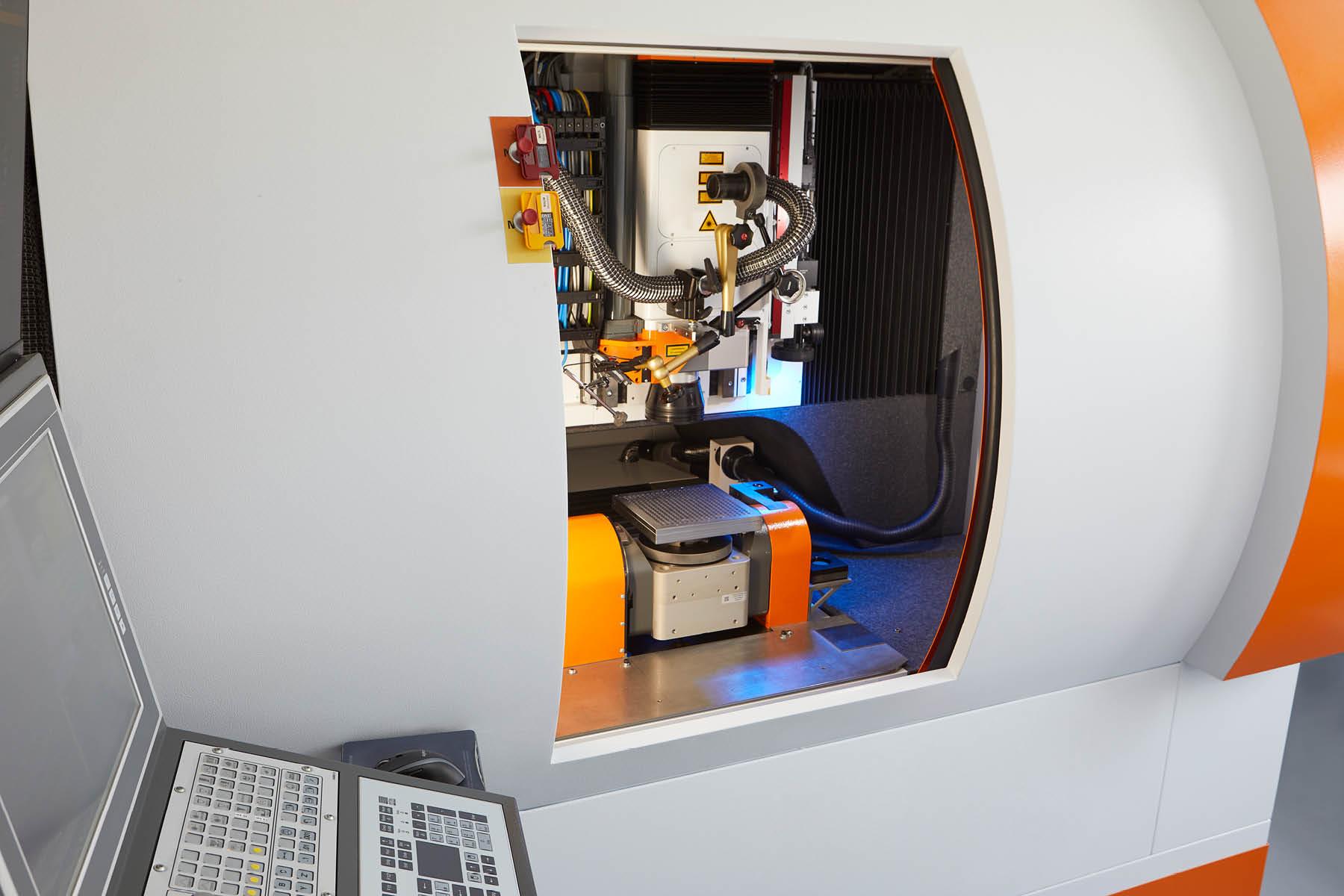
Damage resulting from heat input used to be a concern, until the latest developments in the field of pico- and femtosecond lasers, which can help prevent such damage, became suitable for use in industrial products. maxon’s own system is configured by a commissioned special system integrator. “Here we have found a development partner with whom we were able to cooperate to integrate an additional laser source; to the best of our knowledge, this is the first machine with this configuration in the free industry,” reports Streicher.
Laser opens new doors
It quickly became apparent what new doors the laser can open. The thinner ceramic is, the more elastic it is. “With wall thicknesses of one to two tenths of a millimeter, we can produce tiny solid-state hinges or springs, for example for use in watches.” Independent of the material of the components, the laser can be used to label, engrave and structure them, to selectively remove material, to cut and turn them, and for other modifications.
Streicher and his team are further advancing the development. One example is a project for an own gearhead that requires absolutely vertical walls in processing. In principle, this is where the traditional laser with its conical beam – which is even more pronounced in ceramic than in metal – would normally reach its limits. However, maxon cooperated with the system integrator to apply its know-how to the new laser technologies, with the result that not only vertical walls, but even undercuts are now possible.
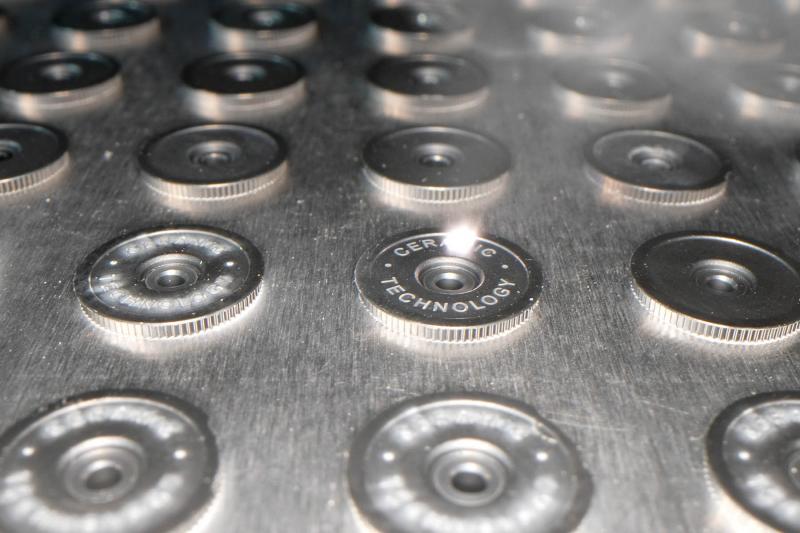
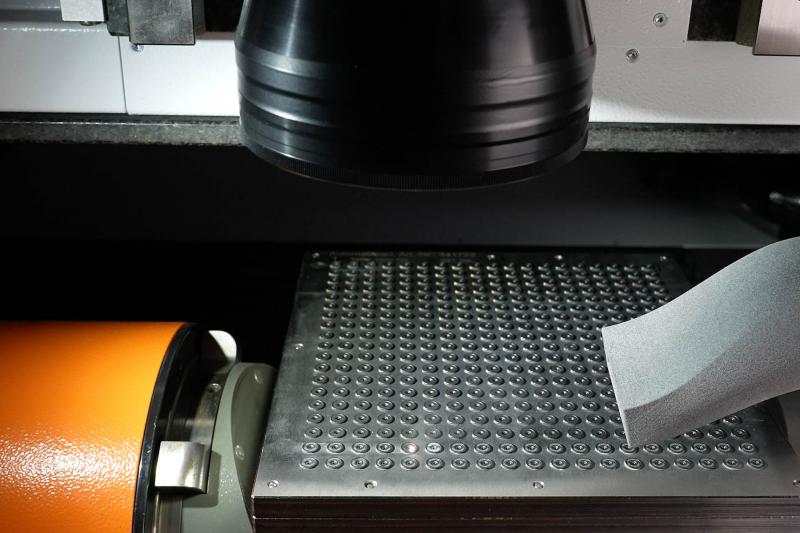
Laser scanning or engraving: Selective ablation with the highest precision.
The method is rather complex, as Streicher describes: “We have an optics box that is comprised of just under 100 optical elements. Some of these can be moved and turned to rotate the beam.” This causes a kind of controlled “tumbling” around the focal position, and, depending on the material, the physical effects involved causes a vertical wall to form. This makes it possible to produce spring-loaded components with a constant cross section or tooth geometries with vertical surfaces, such as those needed in the watch industry. But maxon isn’t resting on its laurels. The development of the laser application is being pushed further – true to the motto: “The sky isn’t the limit and the universe beyond Mars beckons.”