The cold water of the ocean floor is an inhospitable environment for humankind, yet key infrastructure is operating down here. These subsea installations help provide us with vital resources such as oil, gas, and renewable energy, but meanwhile, their structures are in a constant fight against the hostile sea. This means that finding and repairing corrosion that can develop on essential components, such as pipelines and manifolds, is a crucial and regular requirement.
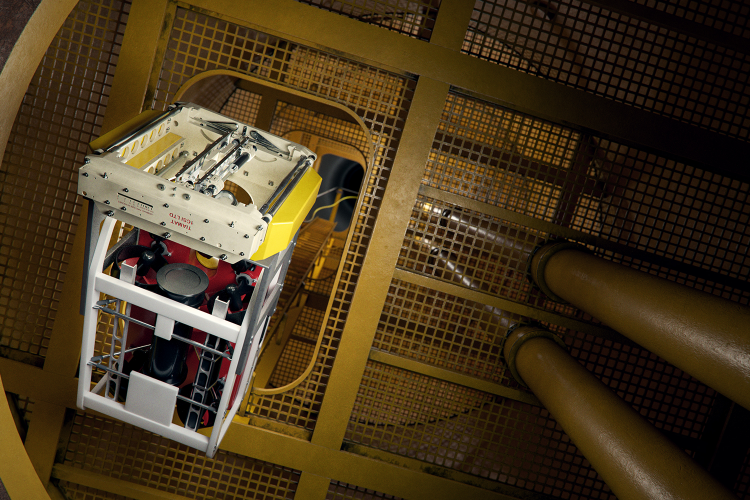
At depths of up to 3,000m, this is beyond the limits of divers. To carry operatives down requires specialised submersibles, making subsea inspection very costly and highly time consuming. But, propelled through the murky depths, a remote operated vehicle (ROV) removes human risk and significantly speeds up the operation. The ROV itself is just one component; it relies on an inspection system that must be able to collect data in order to provide an accurate assessment of the situation. As the ROV operator’s time at sea is a high expense, precision inspection has to be carried out quickly.
Inspection technology
Deliverable from any size of ROV, Tiamat, named after the Mesopotamian goddess of the sea, is a subsea inspection technology that can detect wall thickness, cracks, and flaws on complex subsea infrastructure - even including submarines and inside windmill monopiles. Crucially, the device achieves this with 200 times faster data collection than existing subsea scanners. Currently undergoing deepwater trials, Tiamat has been created by subsea inspection experts 1CSI.

Providing precise data collection is achieved with a full HD camera image, as well as an ultrasonic inspection mapping resolution of 1mm by 1mm with a +/-0.3mm field measuring accuracy. Tiamat’s ultrasonic weld inspection involves phased array transducers comprising as many as 250 elements.
With the ROV guided onto the desired inspection area, Tiamat goes to work. Its wide A4-size scan footprint sweeps forward and backwards across the infrastructure, in an arc of 312 mm by 154mm in 10 seconds, before the ROV guides Tiamat onward to the next inspection area. It’s this relatively large scale of data capture, combined with the video and transducer array, that helps Tiamat achieve such high-speed scanning coverage.
Precise motion control
The smooth and stable travel of Tiamat’s sensors, running on a track that adapts to flat or curved surfaces, is fundamental to the speed and quality of scanning. High performance motion control is vital to manage the position and velocity of the inspection probe carriage, and this is achieved thanks to a pair of maxon MA30 subsea actuators. This underwater drive system is designed specifically to provide control at extreme depths. The compact, low weight actuators are fully sealed and are highly resistant to corrosion, ensuring reliability and long-life operation in the tough marine environment.
maxon’s engineers specified the motion solution to provide precision control. To enhance capabilities for smooth motion, maxon’s engineers customised the motor and gearbox, reducing speed and increasing torque to achieve the optimal rating to suit the application’s requirements.
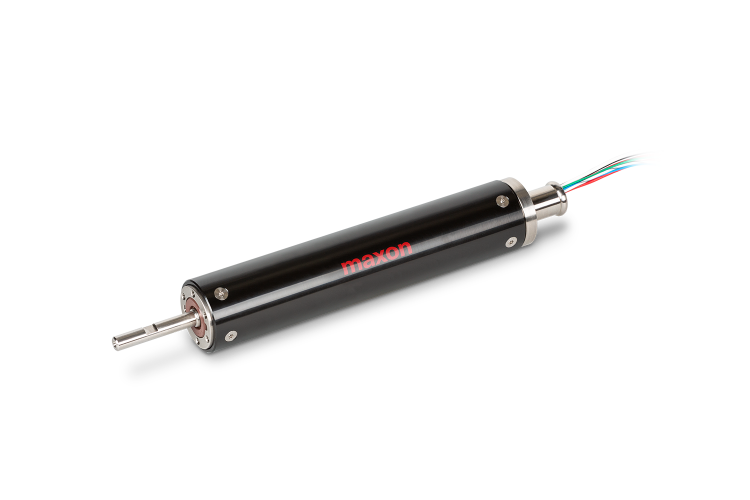
“The motors are absolutely crucial, because scanning demands smooth, frictionless motion,” says Matthew Kennedy, CEO, 1CSI. “While the phased array transducers are collecting data, movement of the carriage needs to be seamless and repeatable, including when scanning a changing diameter asset. We chose maxon because their motors give us the precision we need.”
Subsea operation is one of the most challenging arenas for motion control. With an ROV and its crew located potentially hundreds of miles from resupply, it’s vital that the motors powering Tiamat’s probe carriage are highly reliable and continue to operate efficiently whatever the depth and conditions. This includes overcoming pressure and buoyancy forces.
Deep sea operation
“The motors need to work perfectly at depths down to 3,000m and 300 bar pressure, in a very hostile, cold environment. We wanted a motor that we knew was going to keep working reliably in those conditions, time after time, and the maxon motors achieve this,” says Matthew.
Tiamat is small enough to be carried by observation class ROVs, and measuring just 665mm by 672mm, it can even scan within the most space-restricted locations. 1CSI’s scanner can be used to inspect a submarine’s internal air tanks, accessed from outside the hull even when the vessel is at sea, and it can also enter within the monopile base of an offshore wind turbine.
To achieve this compact footprint, the motion solution had to be small enough to fit within the pre-designed housing, while still delivering the required torque and power. A multi-stage gearbox increased overall length, but careful engineering specification, along with the motors’ high power density, enabled use of a shorter motor design to compensate.
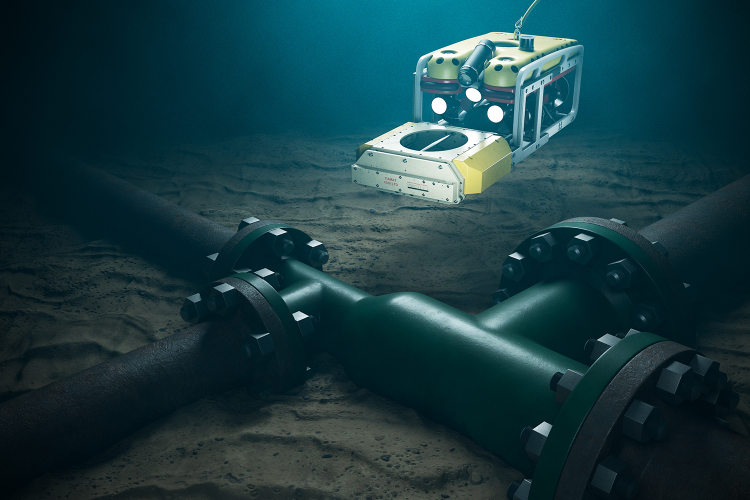
1CSI has completed final testing of Tiamat at its Aberdeen facility and is now moving to deep sea trials in the southern hemisphere. Completing a live test off the west coast of Africa using a previous ROV system, Matthew and his team are already satisfied with the performance of the maxon motors at depths down to 3,000m.
In mythology, Tiamat was a powerful goddess of the sea, and amongst the challenging marine environment, faith needs to be strong. But, thanks to 1CSI’s innovation, ROV operators and subsea infrastructure management teams have state-of-the-art technology on their side to reduce the time and cost of inspection.