The CEO of Blueprint Lab, Paul Phillips has combined his passion for mechatronic engineering with his love of surfing and diving in the ocean. The company, located in the Sydney, Australia suburbs, designs and manufactures products that operate in the harsh environment of the ocean floor. According to Paul, “I realized at an early stage that subsea vehicle manufacturers were in need of specialized hardware for performing remote manipulation tasks. Developing such tools themselves was prohibitively expensive and complex. The Blueprint Lab team “love tech more than anything else” which is why we are intent on inventing technically innovative products. We love what we do,” he explains.
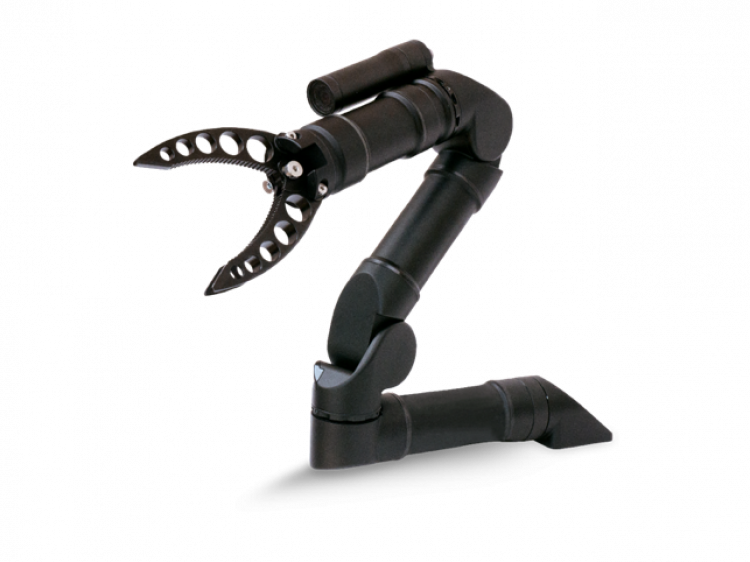
The Reach Alpha 5 is the world’s lightest underwater five-function manipulator.
The unique selling point of the company’s robotic manipulators and grippers is size. The Reach Alpha 5 is the world’s smallest ROV manipulator, according to Paul. When curled up, it’s only ~23x15x4cm (~9x6x1.5-inches)—and is ~58cm (~23-inches) at full extension with a dynamic reach of ~40cm (~16-inches). The arm is able to life 2kg (~2 pounds) of weight at full reach and an axial load rating of 100kg (~220 pounds). End-effector closing force is about 600N. The units are designed to operate at depths of up to 300 meters (nearly 1000 feet).
As a usable addition to any ROV, the Reach Alpha 5 is an all-electric device that runs off of 18-30 VDC. The system is fast and easy to integrate through standard RS232/RS485 protocols. The unit offers leak detection for peace of mind prior to vehicle launch. Interchangeable end-effectors include standard pincer grips as well as quad jaws, specialized recovery jaws, needle nose grippers, soft jaws, parallel jaws, and rope cutter jaws. The units are primarily made of hard anodized AL6061aluminum. Both arms and end-effectors can be made from stainless steel for harsher environments and where increased strength is needed.
The Reach Alpha 5 is driven by maxon DCX 16mm motors and planetary gears. The motors are integrated in a side-by-side arrangement so that they are able to drive in both directions efficiently. An in-house designed controller fits between the motors to maintain a compact arrangement. A spiroidal gear assembly, also designed in-house, is used as the final drive element. Feedback for the system is supplied by a built-in hall-effect absolute position encoder. “For the higher torque joints, we use high-torque gearboxes due to their increased load capacity. For other joints, such as the grabber and the inline rotation motors, the standard DCX components were sufficient,” Paul said.
“Because we developed the hardware, firmware, and software for our products in-house, we were able to deliver much higher levels of optimization, serviceability, and support to our customers,” Paul said. The biggest challenge for the company has been taking a product from the prototype to production stage of development. The need to get everything perfect every time is essential in order to provide the conformance, process capability, and repeatability in production that customers require. Because of this, Blueprint Lab sees one of maxon’s major advantages is their online configurator for customizing motors—with production in 11 days—which allows customers to order motors 24/7. And then deliver the product in production level quantities as the market demands.
The maxon DCX program includes motors that offer high power density, high efficiency and are a smooth-running line of motors. The motors are available for online configuration in sizes from 6mm to 35mm. Customers can choose between precious metal or graphite brushes, ball or sintered bearings, and much more in a contained or frameless package. maxon allows users to configure and combine DC or BLDC motors and planetary gearheads and sensors according to their individual specifications. Through the different generations of the product the motor and gear ratio changed to better meet customer requirements and improve robustness. According to Paul, “The DCX range allowed for these changes to be seamless without requiring any mechanical design.
During the development stage for an actuator, for example, the company might order as many as 20 motor variations online before settling on the right product. This actually saves the company money, since research time is so much more expensive. Plus, it allows Blueprint to test all available options prior to selection.
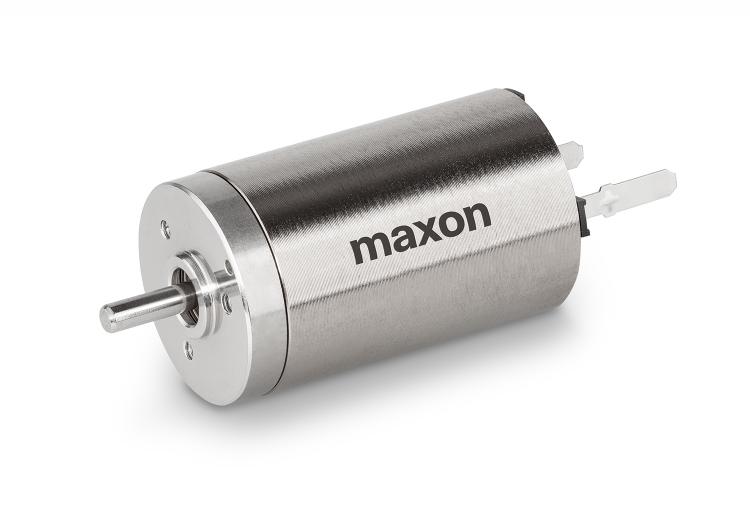
During a brainstorming session with maxon’s Bianca Braun and Brett Motum, additional ideas were offered. During the session, Paul and his team turned to maxon controllers as a subject. One initial desire for the company would be to incorporate a stripped-down version of maxon’s ESCON servo amplifier to suit motor diameters. The conversation further drifted into methods where a controller could be configured by an engineer. The designer would select from features already resident in the motor controller hardware and then configure the shape of the controller online. “maxon’s openness to new ideas is important,” Paul said.
Most applications for the company’s robotic manipulators are in hard to reach or dangerous locations. Units are used on ROVs for search and recovery operations, conducting offshore infrastructure inspection for oil and gas operations, collecting samples for marine science research, as well as in Special Recovery Operations by the military and civil first responders. Besides operating under the ocean for research, the Reach Alpha 5 can be used for police and military operations such as bomb disposal robots and for close visual inspecting in petrochemical and nuclear operations.

The build-up of core technologies in-house for the Reach Alpha 5 provides Blueprint Lab with a strong technical advantage over other companies while they expand into broader markets, such as nuclear, petrochemical, land, and aerospace applications. “We are always thinking of the next developments,” Paul explained. For example, machine learning algorithms are a hot topic at the company as they are implementing hardware in their latest products that will help lead them into the AI future.
Blueprint Lab is a forward-thinking, tech-savvy company operating with over 20 creative engineers who love what they’re doing. Paul admits that he’d like to see more women engineers applying at the company. “It would be great to see more female mechatronic engineers in Australia,” he said. “We are always looking for dynamic people and there are simply not enough female graduates for the robotic industry right now.”
It’s amazing what can be done when you put together the right engineers and the right products. Blueprint Lab has made it their mission to incorporate precision components such as maxon motors in their products. With the growth in remotely operating vehicles of all kinds that are using robotic arms and grippers, there will be a place for companies like Blueprint Lab for years to come.