Requirements: Compact multi-axis system concepts
Products such as surgical robots, analytical instruments for medical devices and laboratory technology, as well as multileaf collimators for radiation technology need miniaturized drive systems that can be tightly packed into an installation space. An ideal drive package includes not only electric motors, but also compact, networking-capable motor controllers that can be integrated directly into the device, close to the motor and sensors.
Focus: Miniaturized motor controllers
The key properties of the motor controllers are high energy efficiency and high power density to allow space-saving integration of all components. Connectors for various sensors and actuators, as well as a fast bus interface, are equally important. The EPOS4 Micro modules offer a large standardized function range, leading-edge control algorithms, a compact power stage, as well as a CANopen or EtherCAT interface – and yet are no larger than a postage stamp (from 32 × 22 × 7 mm). Device manufacturers can integrate the plugin modules into their own electronics for the required number of axes. This makes it possible to produce a cost-optimized multi-axis system with ultra-compact dimensions.
Bus interface as spinal cord of the entire system
Via the bus interface, each drive unit exchanges command and access data with the master controller (e.g. PLC or maxon MasterMACS) in a fast cycle. Common fieldbus systems used for this are CANopen and EtherCAT. EtherCAT’s very high transmission rates offer advantages for complex multi-axis applications in particular, but it has the disadvantage of requiring additional hardware and the large, standardized RJ45 connector for coupling individual axes. The size of the controller and bus connector can sometimes be the deal breaker for the use of EtherCAT in handheld devices and robotics.
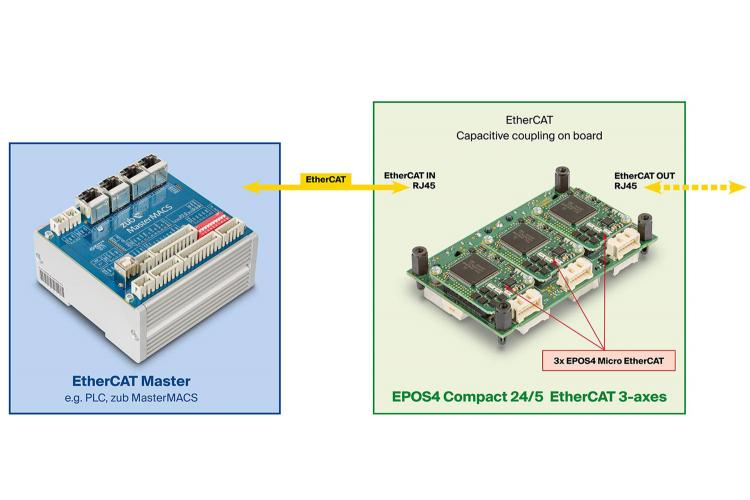
Coupling via external RJ45. Internal capacitive coupling on 3-axis board.
Micro, even with EtherCAT
EtherCAT makes use of inductive transducers to shield DC signal components based on potential differences, suppress interference, and ensure signal integrity. However, these components and the RJ45 connectors need a lot of space on the printed circuit board and increase costs if they have to be integrated separately for each drive controller. When several EPOS4 Micro units are integrated into the same electronics board, it is alternatively possible to internally connect the EtherCAT ports using a capacitive coupling. This is a highly compact and cost-saving solution. RJ45 connectors are then only needed for the external EtherCAT connection. Based on this principle, maxon offers an extremely compact multi-axis controller with an installation size of 90 × 56 mm (the size of a business card), equipped with three EPOS4 Micro 24/5 EtherCAT modules.
Micro, and easy to integrate
The data exchange and command functions of the EPOS4 Micro via CANopen or EtherCAT make use of the CiA® 402 protocol (Device Profile for Drives and Motion Control). The following standardized operating modes are supported: “PPM – Profile Position Mode,” “PVM – Profile Velocity Mode,” “HM – Homing Mode,” “CSP – Cyclic Synchronous Position,” “CSV – Cyclic Synchronous Velocity,” and “CST – Cyclic Synchronous Torque.” As a standardized motion control slave, the EPOS4 Micro (like all EPOS4 versions) can be integrated into the system manager tools and motion libraries of various PLC manufacturers. Applications that are commanded by a PC or Raspberry Pi via maxon’s EPOS Command Library are also possible.
Micro, and ready for IIoT
The EPOS4 is the bottommost information supplier in the IIoT (Industrial Internet of Things) environment of a machine or of the drive train. Via the EPOS4 bus interface, it is possible to access motor currents and torques, position values, error statuses, temperature and load values of the controller and motor, as well as external sensor and actuator statuses, or data can be cyclically transmitted.
Micro, yet multifunctional
With a 25 kHz current controller cycle and 2.5 kHz speed/position control cycle, the cycle rates of the EPOS4 Micro are identical to those of all other versions of the EPOS4 product line. State-of-the-art controller concepts such as Field Oriented Control (FOC), Feed Forward and Observer Control, as well as Dual Loop Control enable the EPOS4 Micro to provide maximum motor performance and precision of movement. The dual loop control with an incremental encoder on the motor shaft and an SSI encoder on the output shaft enables precise positioning of the load, even on drive systems with backlash, or elastic drive systems.
Micro, but versatile
EPOS4 Micro supports brushed and brushless DC motors with Hall sensors, digital incremental encoders, and SSI absolute encoders. A total of 5 digital inputs, 3 digital outputs, 2 analog inputs (+/–10 V), and 1 analog output (+/–4 V) make connection and evaluation of additional actuators and sensors possible.
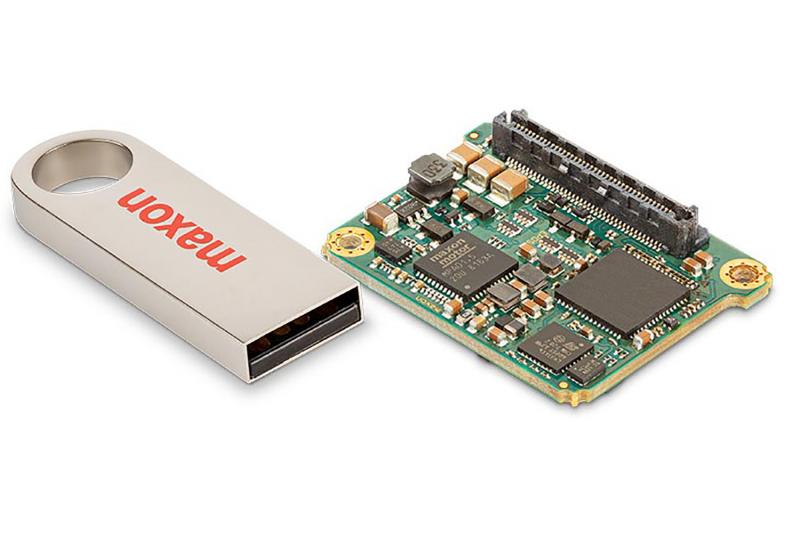
Size comparison: EPOS4 Micro and USB stick.
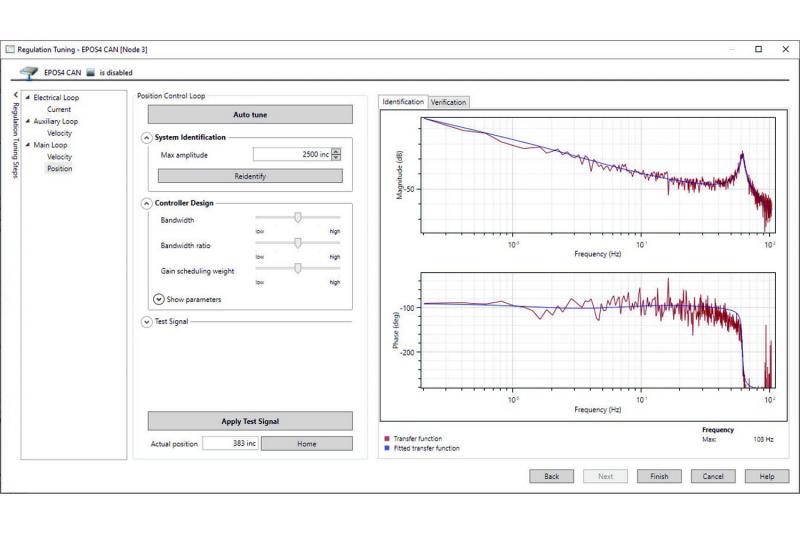
EPOS Studio: Dual loop control tuning.
Micro, but powerful
The EPOS Micro offers a power density of more than 50 W peak power per cm2 installation size without additional cooling in ambient temperature conditions of –30° C to 45° C. In practice, this means a continuous output power of 120 W and peak power of 360 W for 10 seconds, with the controller and power stage requiring an installation area of just 32 × 22 mm (“EPOS 24/5 Micro CAN”) and a thickness of 7 mm.
Micro, also during commissioning
The intuitive EPOS Studio commissioning software includes the Startup Wizard, which guides the user through the basic configuration and provides automatic tuning of all controller parameters, even for complex dual loop controller structures.
More than just products: maxon as system partner
With its support portal support.maxongroup.com and various services, maxon offers a lot more than just catalog products. For the integration of the EPOS4 Micro in customer-specific electronics boards, maxon is also available as development and production partner. In such cases, maxon is not only the product supplier, but also takes responsibility for the entire system as competent engineering partner in the field of drive technology. Early information exchange and idea finding in cooperation with maxon is the first step toward a solution that is optimal from both a technical and a commercial point of view.
In a nutshell:
Competent and goal-oriented – the EPOS4 Micro and maxon services power success.