Firstly, the difference between ambient temperature and winding temperature. Input supply is divided into voltage (V) and current (A). The voltage determines the speed, and the current determines the torque. When the motor is in use, the current will generate heat in the winding. This means that when a motor is specified for operation at high ambient temperatures, it cannot be worked as hard as if it was at regular workshop temperatures; otherwise, it will burn out.
What are the problems associated with heat?
Inside the motor, there is a magnetic circuit generated by the permanent magnet and the electromagnet – the motor winding. Both the permanent magnet and the winding are affected by heat. The neodymium magnets start to demagnetize at around 160⁰C, and they become weaker. Unfortunately, cooling the motor does not reverse the effect; it is a permanent degradation. The winding is encased in an insulating varnish, which provides stability as well as insulation. As the temperature increases above 160⁰C, the varnish softens, and the winding can deform, resulting in rubbing which wears away the insulation and causes a short circuit and motor failure. Very high temperatures can cause the varnish and insulation to melt, again resulting in a short circuit. The results are always the same: the motor is ruined.
maxon high-temperature motors
Not surprisingly, in some environments where people want to use motors, the temperatures are higher, for example when drilling into the Earth’s core for oil, gas or geothermal energy, or in valve actuators on an aircraft engines. maxon has a range of DC motors designed for these environments. The brushless HD (Heavy Duty) range can operate in ambient temperatures of up to 200⁰C, with a maximum winding temperature of 240⁰C.
How do these motors operate in such high temperatures?
The magnets in the maxon HD motors are manufactured from samarium cobalt (SmCo). Samarium-cobalt rare earth magnets can reach much higher temperatures before they start to demagnetize. The insulation of the copper wire used in the winding also has a higher temperature rating. Finally, the impregnation varnish is rated to a much higher temperature, which ensures that the winding remains stable throughout the operating temperature range.
Why not make all motors capable of reaching higher temperatures?
It is not easy to manufacture a high-temperature motor; the enhanced insulation on the copper wire is very rigid, which makes it much more difficult to wind. It also doesn’t work with all winding patterns. Another reason is cost, more specialized materials cost more. Why would people want a more specialized, higher-priced motor for an application where it isn’t needed?
In high-volume applications, maxon can upgrade standard motors for projects where higher temperatures are needed, if there is no suitable motor in the limited HD range. maxon will investigate the feasibility of producing the winding and create a production-size batch of windings to ensure there is high enough yield from the wire. Finally, if the yield is sufficient, sample motors will be manufactured, and the technical specification validated.
What do you do when your application is pushing the ambient temperature boundaries?
Contact your maxon technical sales engineer. We are all trained to specify the right product for the right application in the right environment.
First, we will ask a series of questions about the application. What speed and torque are needed at the output? What duty cycle will the motor see? What is your input supply? We then look at the environment, temperature, shock/vibration etc. We will also enquire about other restrictions, space envelope, mass etc. Once we have collected all the data, we start examining the possible options to provide a solution.
When there are high temperatures, we must carry out a thermal analysis to ensure the motor is not going to burn out in service. We analyse the speed and torque profile over the duty cycle, based on the specific ambient temperature. The maxon-developed software we use gives us crucial information, including the winding temperature. Is it reaching or passing the maximum winding temperature? Is there enough time in the duty cycle to allow it to cool down? After multiple cycles, is it remaining below the maximum winding temperature?
With our training and the tools available, we will only specify a solution we are confident will meet the requirements.
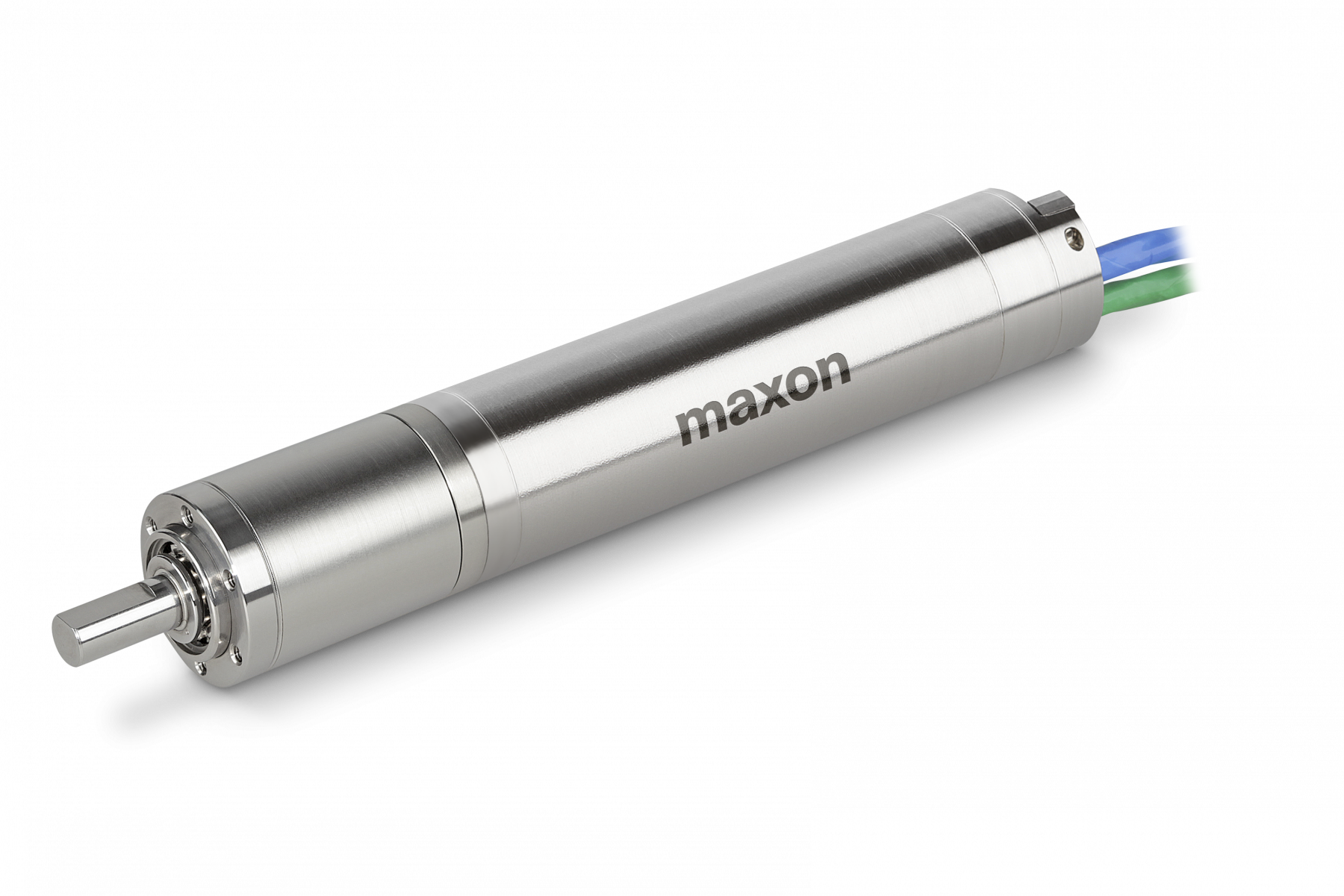