We’ve checked in, the smell of kerosene is in the air, a quick look at the boarding pass confirms the seat number. Passengers are standing in the aisle, placing their carry-on bags in the overhead compartments. Invisible to the eye, powerful micromotors assist as a cabin crew member pushes the compartment’s lid upward to close it. Welcome on board, and welcome to the invisible world of electric drive systems.
Automatic aviation systems
The pilot steers the plane to the runway, pushes the thrust lever forward, and takes the machine into the air. His control joystick is equipped with small electric motors that create a force feedback. This lets the pilot know effectively and in real time what is going on at the wings on the outside of the plane. Long gone are the times when the control stick was connected directly to the flight control surfaces via cables. When cruising altitude is reached and the autopilot is activated, the throttle lever moves automatically (auto throttle), controlled by a DC motor.
At the back of the cabin, the plane’s air conditioning is working hard to ensure that passengers are feeling well at an altitude of 10,000 meters. Temperature, oxygen, and air are controlled via numerous small valves and actuators, most of them brushless flat motors. The air conditioning system of a Boeing Dreamliner for example contains nearly 50 maxon EC 45 flat motors.
When nature calls
It’s a fact of life that sooner or later, every passenger needs to visit the bathroom. Electric drive systems in the background ensure clean processes, regulating for example the water supply and the flushing. In the future, touchless functions are planned for even more convenience.Leaving the lavatory, an envious glance strays to the business and first-class sections. We get the idea: The more electric motors, the higher the level of comfort. In practice, this can be experienced in the seats. They can be adjusted and even extended to form a bed at the push of a button – electrically driven and automatically. A recent feature is the ability to adjust the seat cushion hardness by changing the air pressure, to make even long-haul flights pleasant. The manufacturer Lantal uses brushless maxon motors for the relevant valve. If sunlight in the face disturbs a nap, the window blind can be lowered by pushing a button. This again is accomplished by – you guessed it right – maxon precision motors.
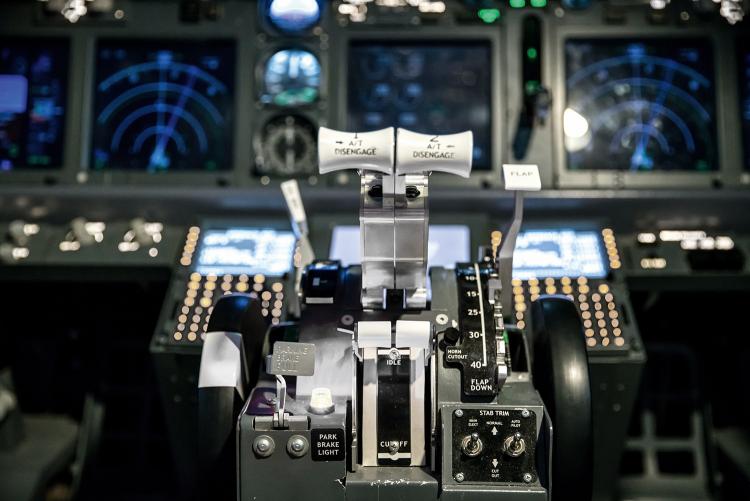
Seamless Internet connection
Back in the economy class, passengers at least don’t have to go without entertainment. The screens above the seats are extended simultaneously to show safety instructions or movies. For those who prefer to surf the Internet instead, an increasing number of passenger aircraft is equipped with communication antennas that continuously and automatically direct themselves to capture the best satellite signal. Each antenna requires three EC-4pole drives with matching HD gearheads.
Then the plane descends for landing, and the landing gear is extended. To ensure it remains extended, a motor-gearhead combination of a DCX 22 and GP 32 HD operates a locking pin. Like so many functions on board an airplane that are powered by electric drives, this too remains invisible to the passengers. Medium and long-haul aircraft contain several hundreds of such drives, and their number is constantly on the rise as higher quality standards permit the replacement of hydraulic or pneumatic systems with electric actuators. At the same time, electric drives are used in new applications that improve the comfort of passengers.
Electrical systems save a significant amount of weight compared with hydraulics. This is why they play an important role in making passenger planes more environmentally friendly and cost-effective. Other approaches include more energy-efficient engines and lightweight fuselage construction techniques. Electrical engines won’t be available any time soon, and the traffic in the skies is increasing continuously by 5 percent per year. To keep pollution from increasing at the same rate, tomorrow’s planes need to be fast, quiet, and environmentally friendly. Engineers are working on it.
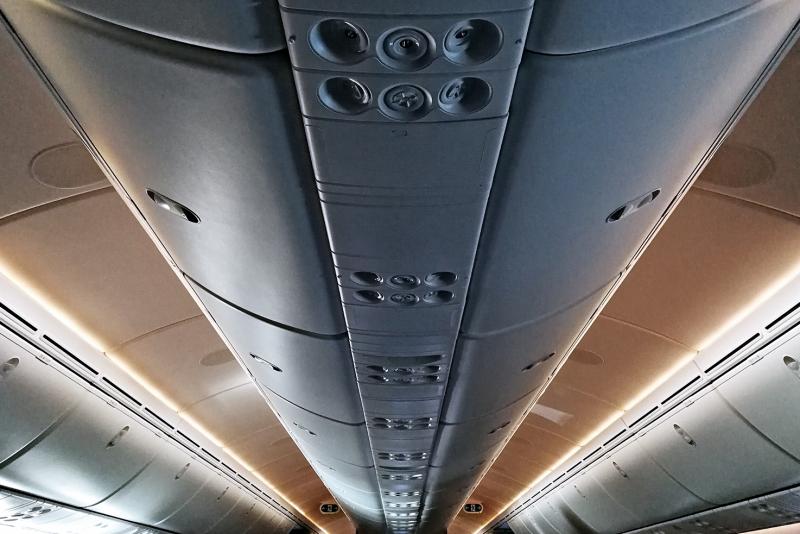
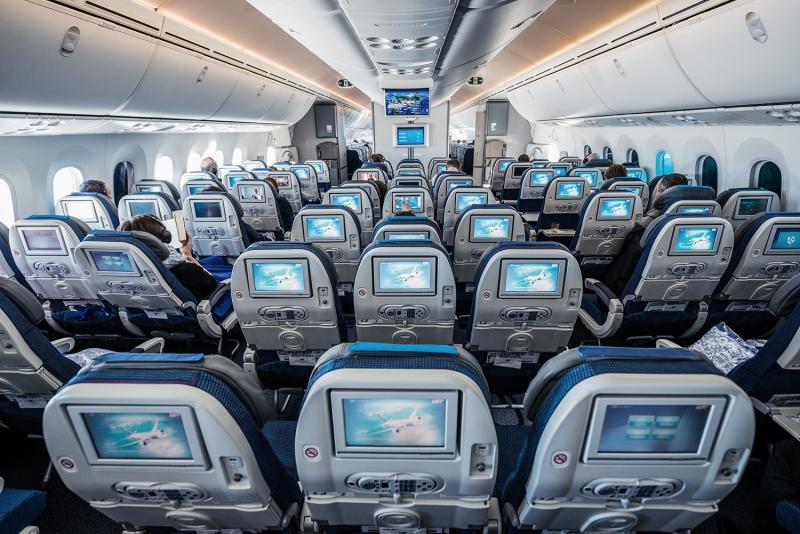
Electrical actuators are everywhere on board – for example in the air conditioning system, where they ensure pleasant temperatures and fresh air (top). In addition, they are also used in handy closing aids for the overhead baggage compartments.
The long road to electric airplanes
It will probably take decades before we will travel in fully electrically powered airplanes. While both major manufacturers and start-ups worldwide are working on concepts and prototypes for electric planes, there is no machine on the market yet that could carry several passengers.
Insufficient energy density of batteries is usually the main constraint. It would have to be five times higher to bring even a small passenger plane into the air. This is why many developers focus on hybrid engines that are powered by batteries on one hand and jet fuel or gas turbines on the other.
Nonetheless, there are fully electric projects for microplanes, such as by Joby Aviation or Ampaire. Both companies have announced prototypes and test flights for the coming two years.
maxon drives in aviation
maxon has a great selection of standard products at a high level that are easy to integrate into a wide variety of aerospace applications. At the same time, the company offers help with custom solutions and complete mechatronic systems. maxon has been certified under aerospace standard ISO 9100 since 2012. Drives are tested in in-house laboratories for vibration, shock, cold, heat, and vacuum.
For more information, visit: aerospace.maxongroup.com