Since 2010, maxon has had a dedicated aerospace organization (a business unit by now) that takes care of specialized projects in space and aviation. The best-known ones are the applications for Mars, such as NASA’s and ESA’s rovers. However, the civilian aerospace applications are just as exciting. They are changing the way airplanes are built.
Robin Phillips, why does maxon need a dedicated aerospace business unit?
The aerospace industry has special expectations and requirements to its electric drive technology. This is why our developers and salespeople need to be specialists and focus completely on these customer expectations. This is an important part of our success. Today, eleven people are working full-time on aerospace projects at the maxon headquarters, and about 25 worldwide. Aerospace is still a small market for maxon, but it’s growing continuously. The projects fit well with our philosophy – after all, we want to develop products that push the envelope with regard to power and size, at the highest possible quality. These characteristics are in high demand in airplane production.
What other requirements apply to electric drives in airplanes?
Electric motors need to function reliably across wide temperature ranges from – 55 to + 85 degrees Celsius, for thousands of cycles. In addition, quality requirements are very high because our drives are being incorporated into applications that are relevant for flight safety, such as the safety valves that cut off the fuel supply in an emergency. At the same time, the industry is under heavy cost pressure, as is evidenced by the low flight ticket prices.
What does this mean for maxon in practice?
We are providing focused training for our employees, for example in soldering techniques. At the same time, we are automating high quality standards in production processes with the relevant tools and processes. This enables us to reliably deliver large quantities. As an example: We supply about 10,000 drives per year for the Boeing 787, or Dreamliner.
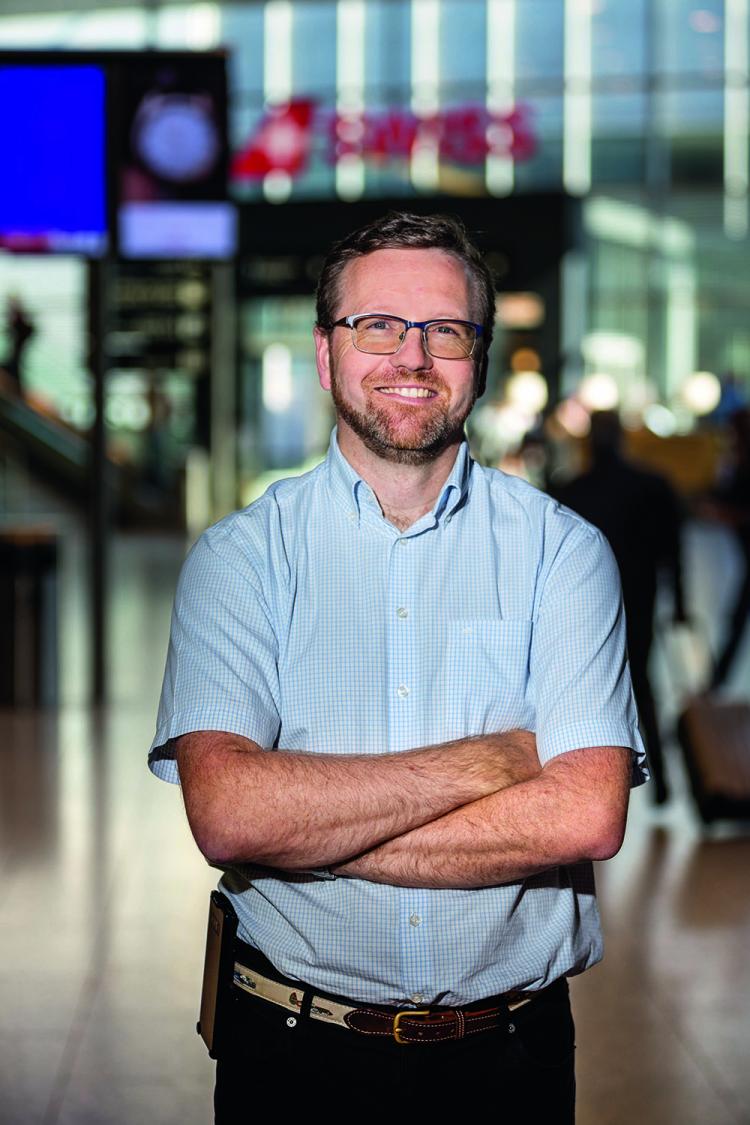
The aviation industry is currently undergoing a migration from hydraulic and pneumatic systems to electrical solutions. What’s the reason for this?
Hydraulic systems are quite maintenance-intensive, and leaks keep popping up. Their fluid-filled lines are also quite heavy. Electric actuators save weight, because they require only a cable for control. They also require very little maintenance.
Why hasn’t this change happened earlier?
Electric motors simply weren’t reliable enough in the past. However, the continuously increasing requirements in various industries have driven companies like ours to become better and better, so that today, even our standard products meet the highest quality requirements. The differences are huge if you compare our current DCX motors with motors from the 1970s.
When will hydraulic systems vanish from passenger aircraft completely?
Smaller planes are already being designed as All Electric Airplanes – except for the jet engines. It will probably take a few decades until this will be the case for large airliners. Flight-critical applications continue to use hydraulic solutions as primary systems, while the redundant systems are already electrical. This is true for example for the actuation of flight control surfaces, or for extending the landing gear. Electric motors come into play only if the primary system fails. However, in the future, even such flight-critical applications will be controlled by two electric drives – so that if the first motor fails, the second motor can take over.
Over the past two decades, maxon has gathered a lot of experience in space applications, with Mars rovers, satellites, private rocket builders. How does the aviation industry benefit from this?
The great learning effect is one reason why we go on such missions. The space industry forces us to examine our motors down to the last detail, running test after test to find and eliminate even the smallest weaknesses. Many of these improvements are then implemented in the standard industry solution. As a result, the aviation industry benefits from our know-how gained in space.