RockÉTS, a Canadian engineering design team from the École de Technologie Supérieure, located in Montreal, is dedicated to the creation, manufacturing and the launching of a high power sounding rocket. Every year, the team participates in the Intercollegiate Rocket Engineering Competition (IREC), where they, usually, launch two prototype rockets. One of the goals of the competition is the accuracy of the flight. As a matter of fact, all the parameters of the flight that can be determined and proven before a flight with accurate prediction being a plus. This allows RockÉTS to score as many points as possible since engineering is proving what we know before it happens.
The rockets must reach a certain target altitude with minimum error. Once the rocket reaches apogee, a parachute is deployed to ensure a safe descent and the recovery of the scientific experiment. In the past during the falling phase, RockÉTS was using a reefed system. This system was a regular round parachute that was kept closed until it reached a lower altitude. The aerodynamic of the rocket was broken and some additive drag was created with this system allowing the rocket to slow down. At lower altitudes, the round parachute was fully deployed allowing recovery within descent tolerance.
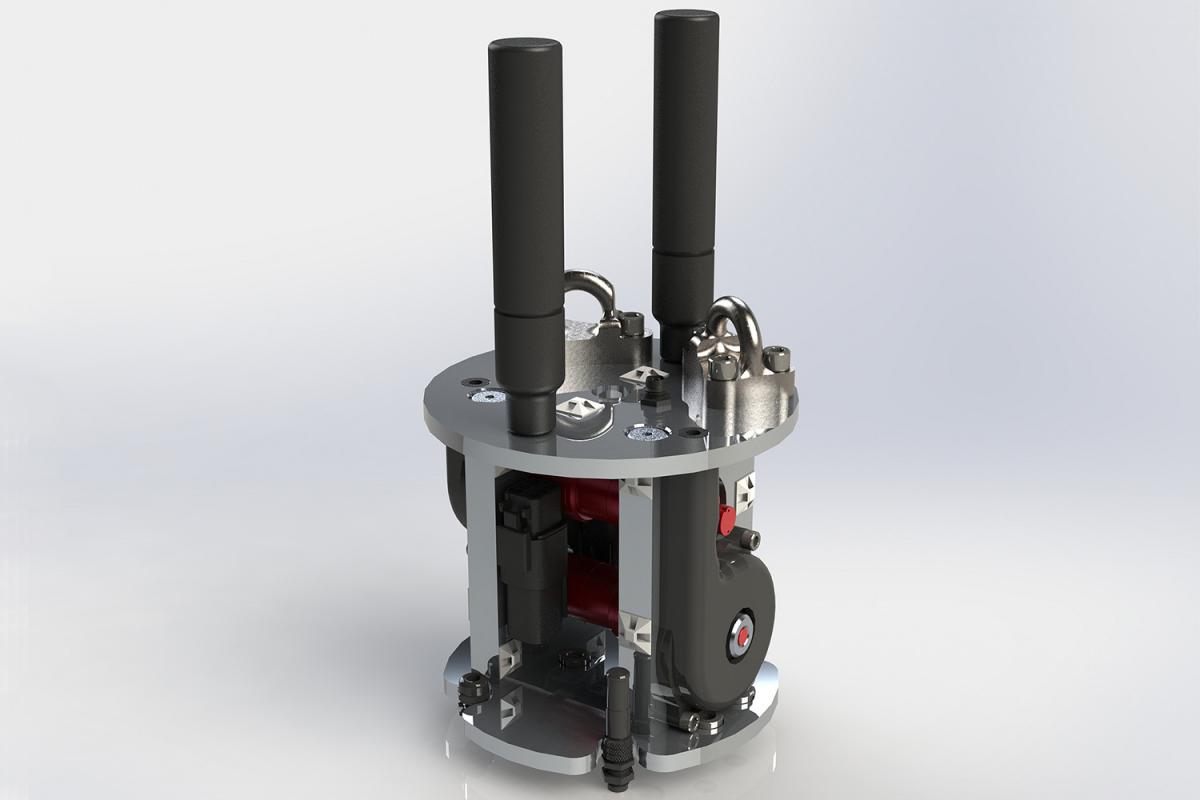
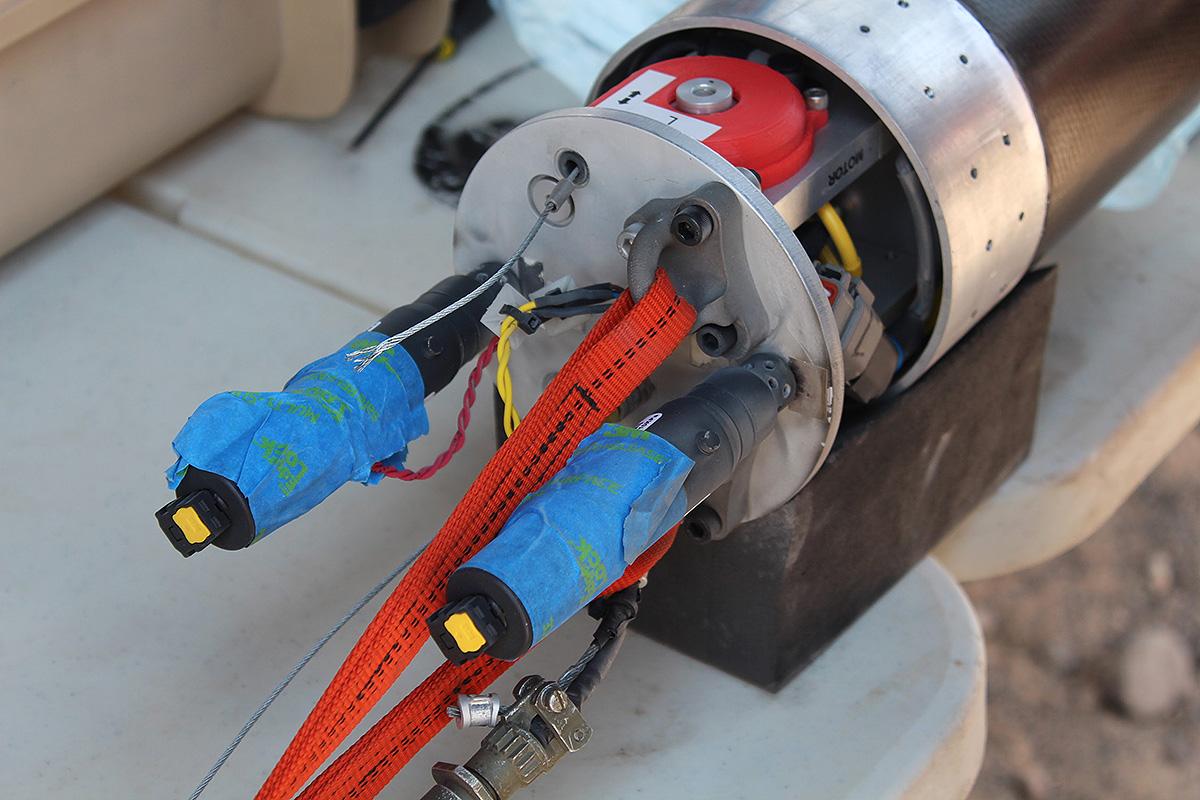
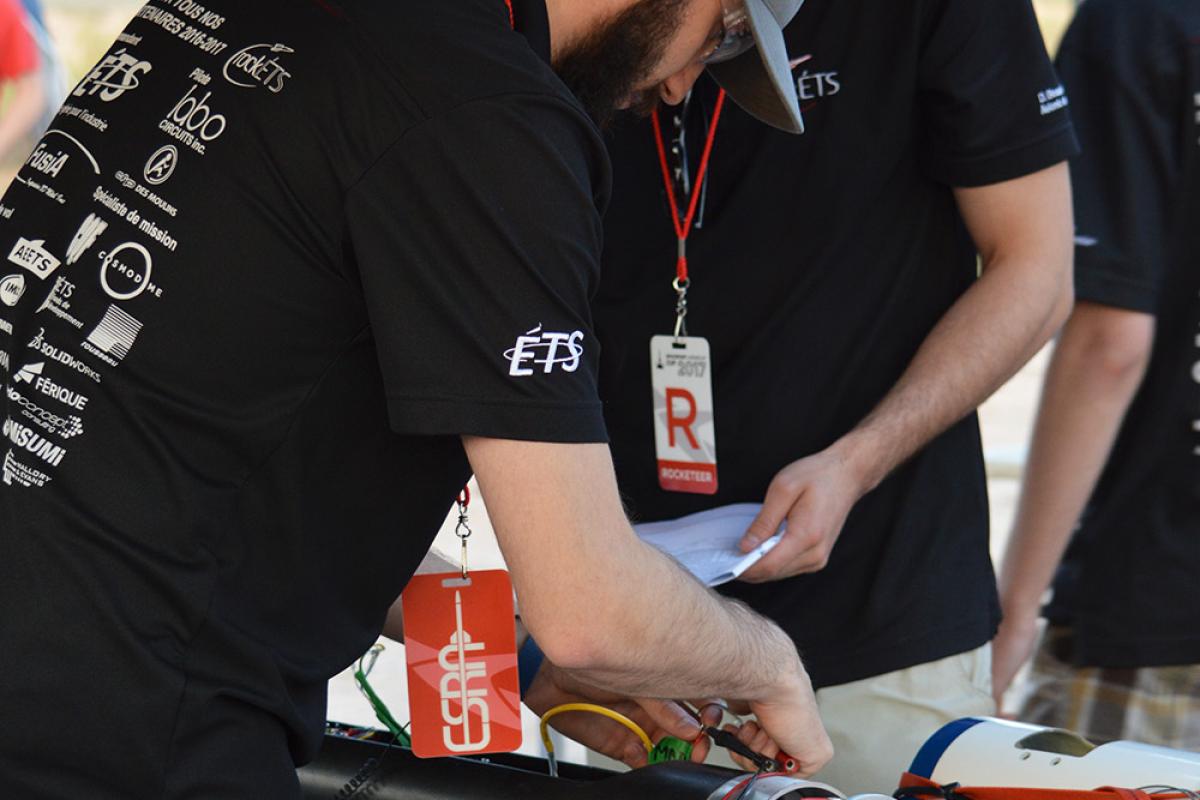
The control system for returning the rocket.
The entire descent is random because it is subject to winds and altitude. The maxon motor technology is required to control the rocket’s descent path with an autonomous system. The project concentrated on optimizing the system by reducing its overall volume, reducing its weight and implementing a new path planning algorithm using a parafoil.
The control system can return the rocket as close as possible to a landing target fixed by a GPS coordinate prior to the launch. Guidance is done autonomously during the recovery phase of flight with the on-site weather conditions. The control mechanism uses two pulleys on which are two fixed steel cables that are connected to the control lines of the parafoil. A custom avionic electronic system was designed to control the motors and to provide a trajectory solution. This system is made for a 5 inch diameter rocket and only occupies 4.5 inches in length. It uses maxon DC-max drives not only because they are fully integrated with gearbox and encoder but because they are small and able to offer incomparable torque relative to its size.
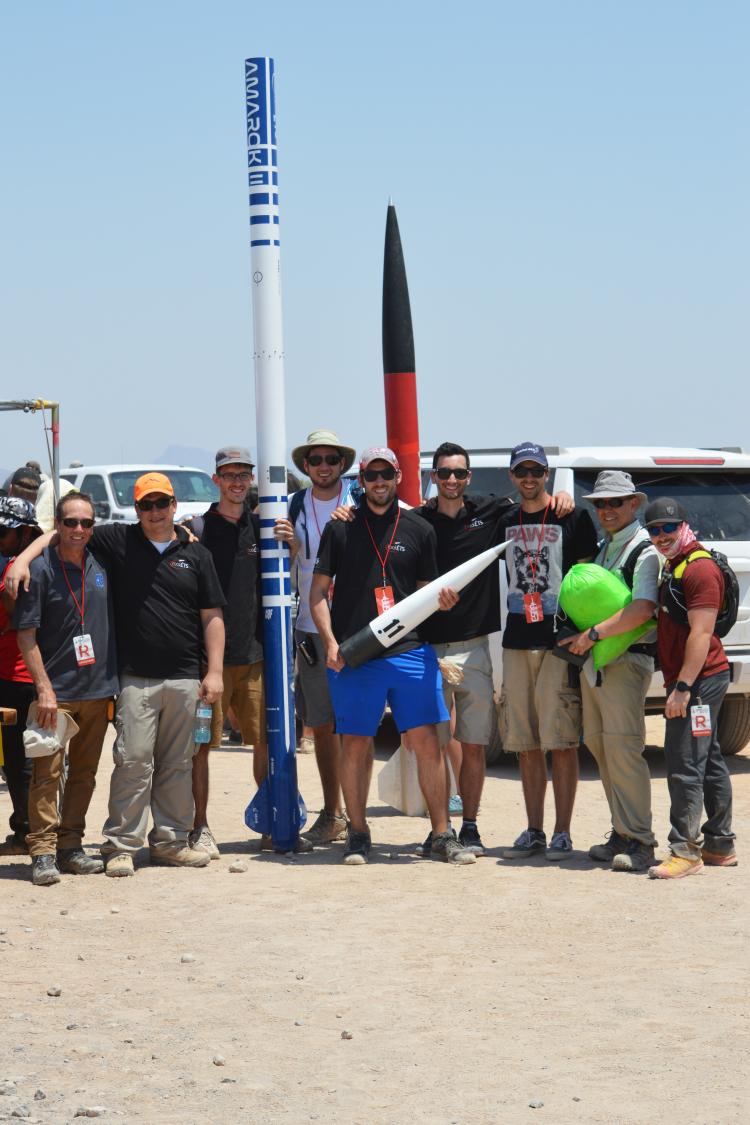
The team had the opportunity to present the project at the 2017 IREC competition in June where they performed their first flight test. Judges were impressed by the quality of the assembly but also the performance of the system in flight. The team demonstrated how they controlled the descent and got the rocket closer to a GPS point and recovered it. The project received the 2017 Dr. Gill Moore Innovation Award and the team intends to continue the development of this technology for the next rocket prototype.