A motor might not just consume energy. It can also generate energy when it comes to the point that a load has to be decelerated. During deceleration a 4-quadrant servo amplifier takes energy from the drive. Because the amplifier cannot store this energy, it is fed back to the power supply. If the power supply is not capable of taking up this energy (e.g. in an output capacity) the output voltage increases. First of all internal capacitors might take and buffer the energy but finally this can increase the DC supply voltage level and trigger some “Overvoltage” protection of the power supply or motor controller.
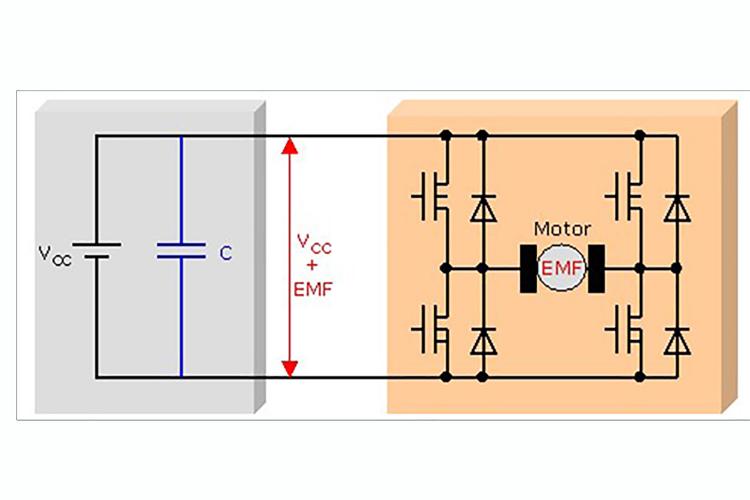
The maximum occurring voltage depends to a high degree on the supply voltage Vcc and the speed n(0) at the beginning of the braking. Further influencing factors are the total mass inertia Jtot and the achieved deceleration rate abrake.
- n(0): Speed at start of deceleration
The speed at the beginning of the braking process defines how much energy must be dissipated. Problems arise in situations, where the speed is very high. In most cases this also means that the supply voltage is high as well. - Vcc: Supply voltage vs. motor voltage
There is a small reserve if the difference of the actual supply voltage and the maximum supply voltage is small. Overvoltage of the controller supply can occur very rapidly. - Jtot:Total mass inertia
On one hand, the total mass inertia is part of the kinetic energy which has to be braked. the higher the kinetic energy, the higher the supply voltage increase. On the other hand, a high mass inertia also means that the deceleration cannot take place too rapidly: To a great extent the energy can be dissipated in the motor winding. - abrake: Deceleration ramp
The achieved deceleration rate depends strongly on the maximum current of the amplifier and on the mass inertia. The deceleration can be reduced by setting a current limitation or by setting the "maximum acceleration" parameter in digital amplifiers such as the ESCON or the EPOS.
The biggest problems arise, where high speeds and high supply voltages are required in in highly dynamic applications with fast set value changes.
Especially in case of vertical applications (e.g. cranes, lifts) without sufficient friction or self-locking gears or in case of a high mass inertia (e.g. centrifuge) a remarkable amount of energy can be generated during a downwards movement or deceleration phase until standstill.
There are different measures to cope with reversed energy. One challenge is quite often that it is difficult or even impossible to estimate the amount of reversed energy and the system’s reaction. Finally there is always some testing required to prove that one single measure or a combination of different measures can solve the “Overvoltage” issue focused on the concrete application.
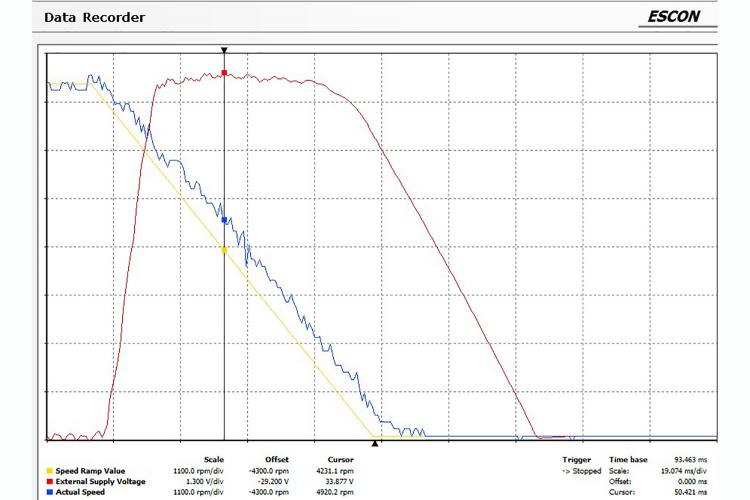
Conclusion:
Supply voltage increases from 24V DC up to 34V DC during deceleration due to reversed energy.
Find more information in Part II.