The maxon catalog contains a large number of brushless motor types that are called EC motors. This article briefly describes their properties and possible areas of application
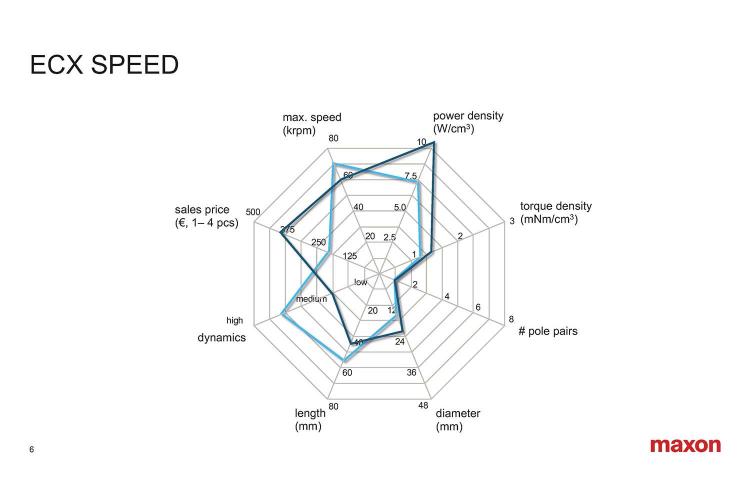
ECX SPEED
- Ironless maxon winding with low inductance
- 2-pole magnet on internal rotor
- Standard and high-performance versions with various magnet strengths
- Sterilizable versions with hybrid ball bearings (ceramic balls) for even higher speeds
- Combination with GPX gearheads and ENX encoders
- Configurable output shaft and electrical interface
Characteristics
As the name suggests, the main feature of this motor range is the high speed that can be achieved. This gives extremely high power density (power per unit volume) despite relatively low torque density. However, this seemingly high power cannot be utilized with standard gearheads and mechanical devices, due to their limited input speeds. Operation with both high torque and high motor speed is only possible with the special GPX SPEED planetary gearheads with input speeds of 50,000 rpm and more. The relative dynamics are in the medium range. Incremental or single-turn absolute encoders can be integrated into ECX SPEED motors, even in sterilizable versions.
Applications
Typical applications for the ECX SPEED motors are handheld tools with high speeds, such as grinders. Sterilizable versions of the motors and even of the motor-gearhead-encoder combinations allow the products to be used in surgical tools. Here the configuration with pluggable connections is an attractive option.
Special point of note:
ECX SPEED motor windings have very low inductance because of their ironless design. Supplying such a motor with a PWM power stage, as with most modern controllers, results in current ripple. Various applications have shown that such current ripple can lead to undesired heating of the motor by 40 degrees or more. Losses of this kind can even become the dominant heating factor in no-load operation. Increasing the PWM frequency helps, but the best way to eliminate current ripple is to add inductors.
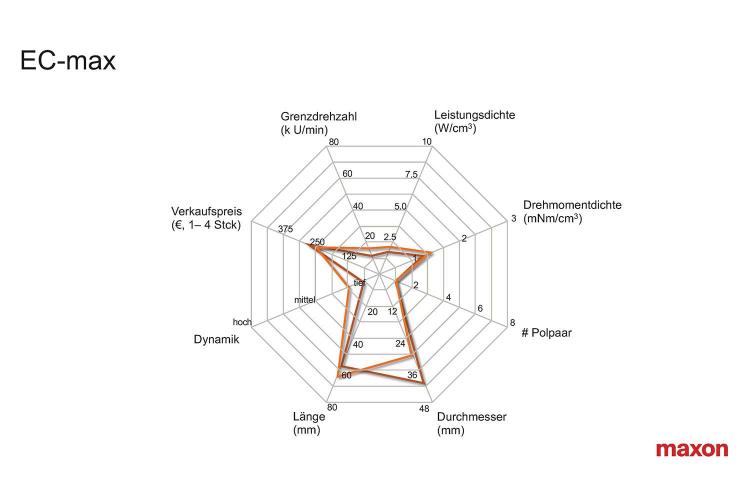
EC-max
- Ironless maxon winding with low inductance
- 2-pole magnet on internal rotor
- Range of diameters: 16 mm, 22 mm, 30 mm, and 40 mm, each in a short version and a long version
- Standard combinations with gearheads in ceramic versions and encoders. Holding brakes are also possible.
Characteristics
The EC-max range offers cost-optimized motors for standard applications that require a brushless motor with long service life. Since the focus is on cost, their torque and speed attributes are moderate, with low power density and low dynamic response. EC-max motors can be combined perfectly with maxon’s ceramic gearheads to create gear motors with long service lives. The relatively low motor speeds match the limited input speeds of standard gearheads, which raise the moderate motor torques to a usable level.
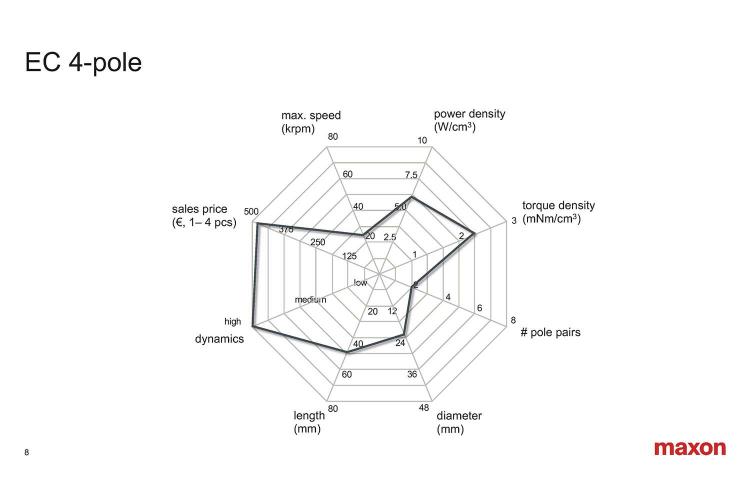
EC 4-pole
- Ironless hexagonal maxon winding with optimized winding segment arrangement for 4 magnetic poles
- 4 magnetic poles (2 pole pairs) on internal rotor
- Range of diameters: 22 mm and 30 mm, the latter also in sterilizable version.
- Combinations with high-precision optical and robust ENX encoders. Holding brakes are also possible.
- Combinations with gearheads are possible
Characteristics
The EC-4pole has a power-optimized motor design, delivering both high torque and a relatively high speed (25,000 rpm) at the same time. The result is a highly dynamic motor with high power per unit volume. The use of high-performance magnetic materials, the complex winding arrangement, and the optimized commutation result in a complex design.
Applications
The EC-4pole is a motor for dynamic, high-precision direct drives. Its relatively high torque can render additional mechanisms and gearheads superfluous. The high-resolution optical encoders are perfect for precise and stiff positioning and for controlling low speeds.
Special versions
The 30 mm motor forms the basis of several more specialized versions that are used in the aerospace industry. Special models in 4-pole design include the 32 mm heavy-duty motors for extremely tough environmental conditions (in terms of temperature and pressure), or even immersion in an oil bath.
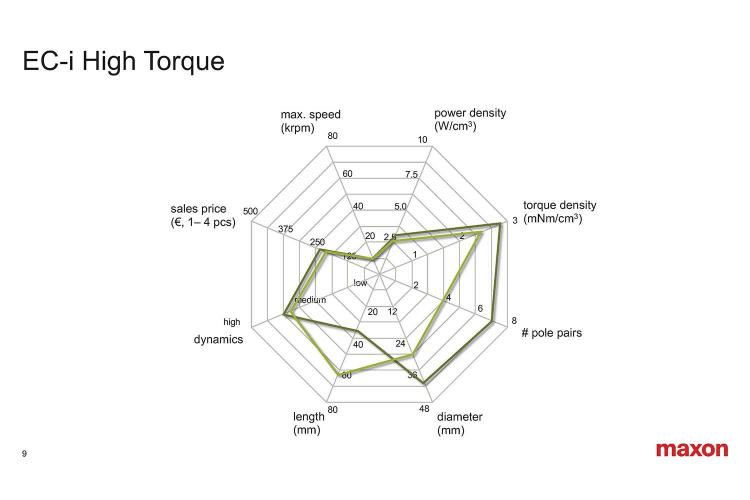
EC-i, IDX
- External iron core winding with relatively high inductance
- Multi-pole internal rotor with up to 8 pole pairs
- Range of diameters of EC-i: 30 mm, 40 mm, and 52 mm; various lengths
- EC-i 52 available with open housing and ventilation
- IDX: square cross-section with integrated encoder in industrial housing, with electrical connections, 2 lengths (M,L)
- All kinds of combinations with encoders, brakes, and gearheads
Properties and applications
EC-i is a range of powerful motors with especially high torques. This is achieved with a high number of pole pairs and a relatively large diameter. You could say they are the big brothers of the ECX TORQUE models. The small diameter of the rotor results in a medium to high dynamic response. EC-i motors are typically used in automation and production systems, and in relatively large laboratory devices. The IDX is a motor for industrial use. In these larger models, note the substantial deviation of the motor parameters from a simple linear relationship. This is due to the high inductance of the iron core.
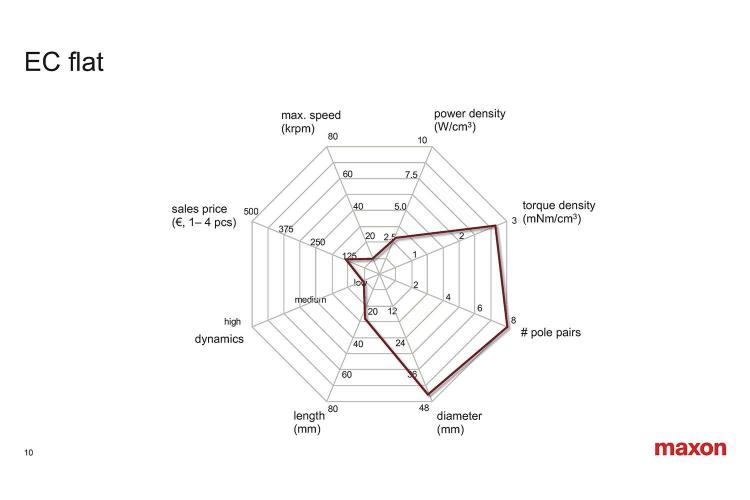
EC flat
- Internal winding with iron core
- External multi-pole rotor with high mass inertia
- Open design for improved heat dissipation by airflow through the motor at high speeds. Can be improved further by an open rotor design and additionally by the use of a fan
- Combinations with all kinds of gearheads. Integrated MILE encoder
- Frameless versions available, with separate rotor and stator for integration into the application
Characteristics
As their name implies, these motors are short but have relatively large diameters. The combination of the large external rotor with a high number of magnetic poles gives them high torque. However, the high mass inertia results in comparatively low dynamic response. Flat motors are cost-effective: They are the most economical maxon motors by far. Note the deviation of the motor parameters from a simple linear relationship, due to the high inductance of the iron core.
Applications
Flat motors are the perfect cost-effective solution for all applications where installation dimensions (especially length) are critical, and where the dynamic response does not need to be extremely high. Pumps are a good example. The flat motors often do not require an additional gearhead. However, combinations with standard planetary gearheads result in relatively short units with high torque. For robotic joints and exoskeletons, these motors are often combined with short, specialized gearheads (such as Harmonic Drive®) to meet high torque requirements and length constraints.
ECX TORQUE
- Iron core winding with relatively high inductance
- Multi-pole internal rotor with 4 magnetic pole pairs (8-pole)
- Only 22 mm diameter, with 3 different lengths (M, L, XL)
- Same or similar configurable shaft and electrical interfaces as ECX SPEED
- Combinations with configurable GPX planetary gearheads
- Integrated incremental or single-turn absolute encoders (EASY)
Properties and applications
The name itself indicates the characteristic feature of this motor: It is developed for relatively high torques and moderate speeds. Its long and slim design makes the ECX TORQUE a perfect motor for handheld tools that require higher torques but not very high speeds, such as power screwdrivers.
EC frameless DT
- External iron core winding with relatively high inductance
- Multi-pole internal rotor
- Flat, short, frameless design, with separate rotor and stator for integration into the application
Characteristics
The EC frameless DT design combines high torque with dynamic response. It is a further step toward so-called “torque motors” that are integrated into the applications and provide direct, stiff, backlash-free control. The first standard model will be presented in the course of 2021.
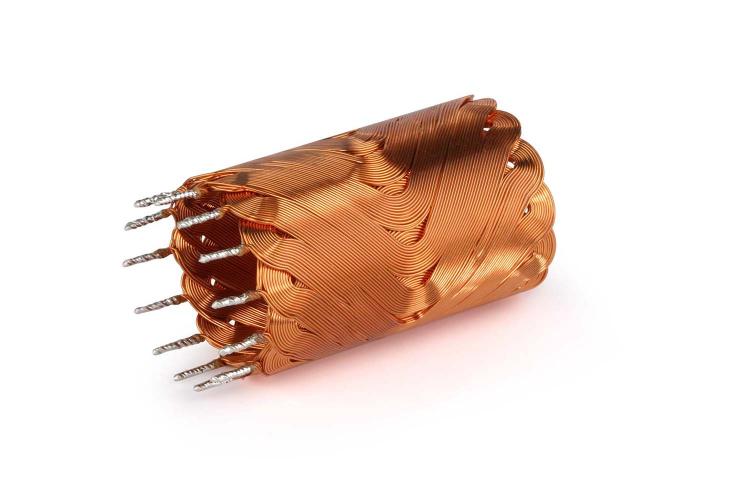
Comparison of design options
Iron core or ironless winding
maxon motors are customarily made with a self-supporting, diamond-shaped winding without an iron core, which enables cogging-free motor operation. Ironless windings are best suited to long motors that run at high speeds. They are used in maxon’s ranges of long-design EC motors with 1 or 2 pole pairs, such as the ECX SPEED, EC-max, and EC-4pole.
Shorter motors in multi-pole designs for high torques use windings with iron cores, such as the ECX TORQUE, EC-i, and EC flat ranges. The additional iron losses in the core put a limit on the top speed of these motors.
Multi-pole or 1 pole pair
One of the main questions when designing motors is whether the motor is to be designed for high speed or high torque. A higher or lower number of magnetic poles can be selected accordingly. Generally speaking, the more magnetic poles, the higher the motor’s torque and the lower the speed. Consequently, maxon’s EC motor ranges for high speeds – especially ECX SPEED – have only 1 pole pair, or a maximum of 2 pole pairs, as in the case of the EC-4pole. maxon’s high-torque EC motors, such as the ECX TORQUE, EC-i, and EC flat ranges, are equipped with 4 or more magnetic pole pairs.
So-called “torque motors” often have an even higher number of magnetic poles. They are often designed for a specific application, in the form of high-torque direct actuators that do not require any additional gearheads or mechanisms. This enables stiff and highly precise control without any disruption from mechanical backlash. maxon’s frameless motors are a first step toward such torque motors.
Internal or external rotor
The dynamic response of a motor depends on the ratio of the torque to the rotor inertia, and is expressed by the mechanical time constant. The rotor inertia, in turn, is heavily dependent on the rotor diameter. The smaller the diameter, the lower the inertia and the more dynamic the motor, meaning a shorter response time.
Therefore, for a highly dynamic response, the diameter of an EC motor must be small. To achieve this, the magnetic rotor has to be close to the shaft inside the stationary winding. If multiple magnetic poles are used, such a design with an internal rotor can still generate high torque.
In products with an external rotor, such as the EC flat motors, the magnetic rotor surrounds the winding from the outside. This results in high inertia relative to the generated torque. Accordingly, the mechanical time constant is considerably higher.
Note that there are other important factors influencing the motor’s dynamic response besides the rotor inertia: the strength of the magnet, the available current, the dynamics of the current rise (i.e. the electrical time constant), all kinds of losses, etc.