One of the fastest growing markets for the maxon is the aerospace market, no doubt through the push to COTS (Commercial Off The Shelf) products. maxon is aware though that the demands of this market mean that often the standard products require modifications to meet the specification criteria for the challenging environments. Through this article it is aimed to promote the diversity of the modifications that maxon can carry out on their products from simple to complex.
Lubrication
maxon has a wide variety of lubricants available for differing temperature environments be that cold temperatures or high temperatures. By working closely with the customer maxon engineers can optimise the lubrication to maintain life and efficiency at the extremes of temperature.
Cables
The standard insulation on the cables on maxon motors is PVC which is often not acceptable to certain industries. maxon have a variety of cable insulations available such as PTFE, ETFE and Kapton to ensure that the finished product is suitable. Lengths of cables can also be altered to avoid excess cable or tight cables. A wide range of connectors can be fitted onto the ends of the cables, maxon has a standard range that are used but are willing to fit customer specific connectors.
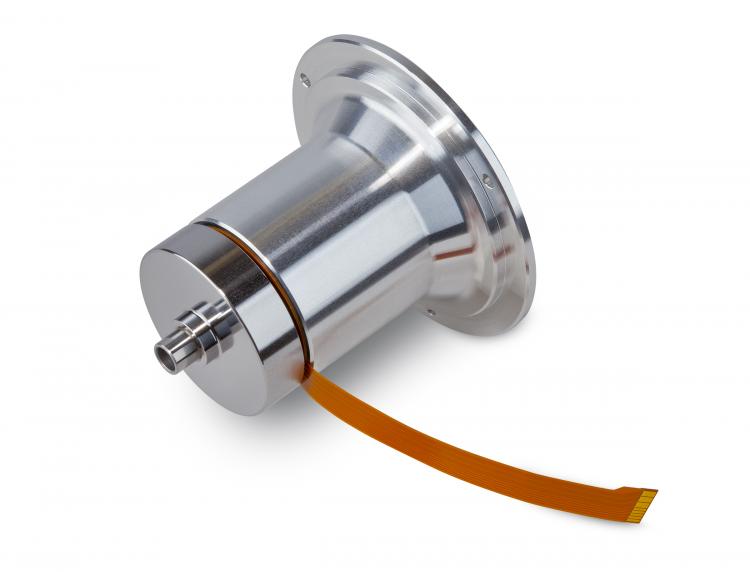
Shaft Modifications
Another of the more standard modifications that maxon carries out is to modify the shaft. Both the main shaft and the back* shaft (* motor dependent) can have modified length either shorter or longer. Flats can be machined onto the shaft, either a single flat or multiple flats at varying angles of relation. A little more difficult is a change in shaft diameter, but this can also be accommodated. Also threads and cross holes can be machined onto the shafts.
The above fall into what maxon like to call standard modifications and are regularly used to adapt motors and gearboxes. These are not the only modifications that maxon carry out, but the complexity is now increasing. It is now more important to work closer with the engineers to ensure the end result meets the specification.
Bearing Changes
When applications see higher shaft loads either axial or radial and a larger unit cannot be used, a change in bearing can be adopted. Replacing the standard bearing with a larger one allows the units to cope with higher shaft loads but changing the bearing may end up resulting in a slightly longer unit with a larger diameter output shaft.
Integration of Non maxon sensors
maxon has its own range of sensors (encoders and resolvers). Some customers however have specific sensors that they need to use for controller compatibility or environmental reasons. maxon can modify shafts and housings so alternative sensors can be integrated.
High Temperature Modifications
At high temperatures the magnets degrade (lose magnetism) and the windings become unstable and the insulation can break down. To resolve this high temperature options are available for certain motors, so they can cope with high temperatures similar to the HD motor range that has been developed. If your application does require higher temperatures it is important to have open dialogue with maxon engineers.
Off Axis Mounting of Gearboxes
maxon motors and gearboxes have been designed for easy axial integration which produces a long unit. When designing for small space envelopes it is not always easy to integrate a long cylindrical object. maxon have supplied motor gearbox combinations where the gearbox has been mounted off axis in a ‘U’ configuration where the gearbox sits alongside the motor. This requires some extra housings and gearing to transfer the rotary motion.
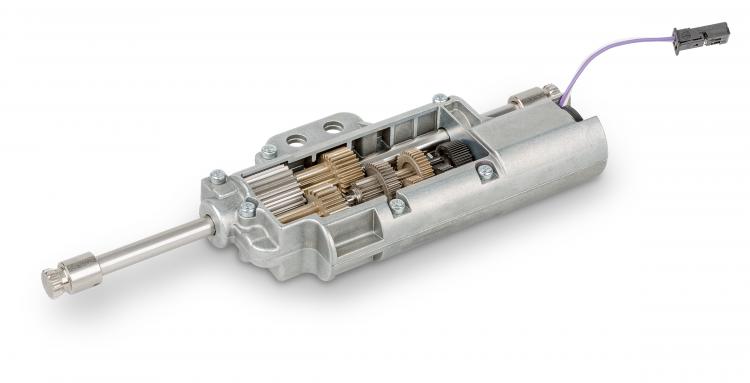
Integration of Bespoke Motion Devices
Firstly, what is meant by a motion device. This is a component or assembly connected to the motor to convert the shaft motion into either linear motion (ballscrews, leadcrews) or slower, higher torque rotary motion or rotary motion through an angle (gearboxes).
When integrating ball and lead screws it is usual to also require some form of thrust bearing arrangement to cope with the axial forces transmitted by the load being moved. Gearboxes can also be used between the motor and screw to fine tune the linear speeds.
Although at the start of this article we were talking about the use of modified standard products and now we have mentioned bespoke gearboxes. maxon has a large range of standard gearboxes and the result is a wide variety of gears in differing sizes and pitches. This gives the ability to utilise these in more bespoke solutions, particularly if the motion is transferred through a 90 ⁰ angle. By utilising the standard gears that are manufactured in volume maxon can deliver cost competitive bespoke solutions.
Modifications for Space
maxon’s space heritage has been published widely in the media. With product used in satellites, on the moon and on Mars, maxon has built up a large amount of technical knowledge in what is required to take the standard products to space rated products. Working in vacuum and at temperature extremes, often having to cope with extreme cold and extreme heat on the same product, coping with high vibration and shock has all become second nature to maxon.
During manufacture there are also some relatively easy to integrate modifications that are used readily in the aerospace industry. These include the use of leaded solder, use of conformal coatings on PCB’s, potting of wire taps and the use of wide temperature Hall Sensors.
So how does maxon give you the confidence that the product they supply to you is up to the job whether it is under the sea, on the ground, in the air or in space? Quality Assurance to EN9100 and investment in a wide variety of test capability including temperature and humidity (-130 to +500 ⁰C, 98% relative humidity), shock (4,000G) and vibration (5 to 5,000Hz, 5,000N), pressure (2,500bar) and vacuum (10 -5 milibar). You can be sure that your requirements will be validated in the lab before any product is delivered.
Author: Andrew Gibson, maxon UK
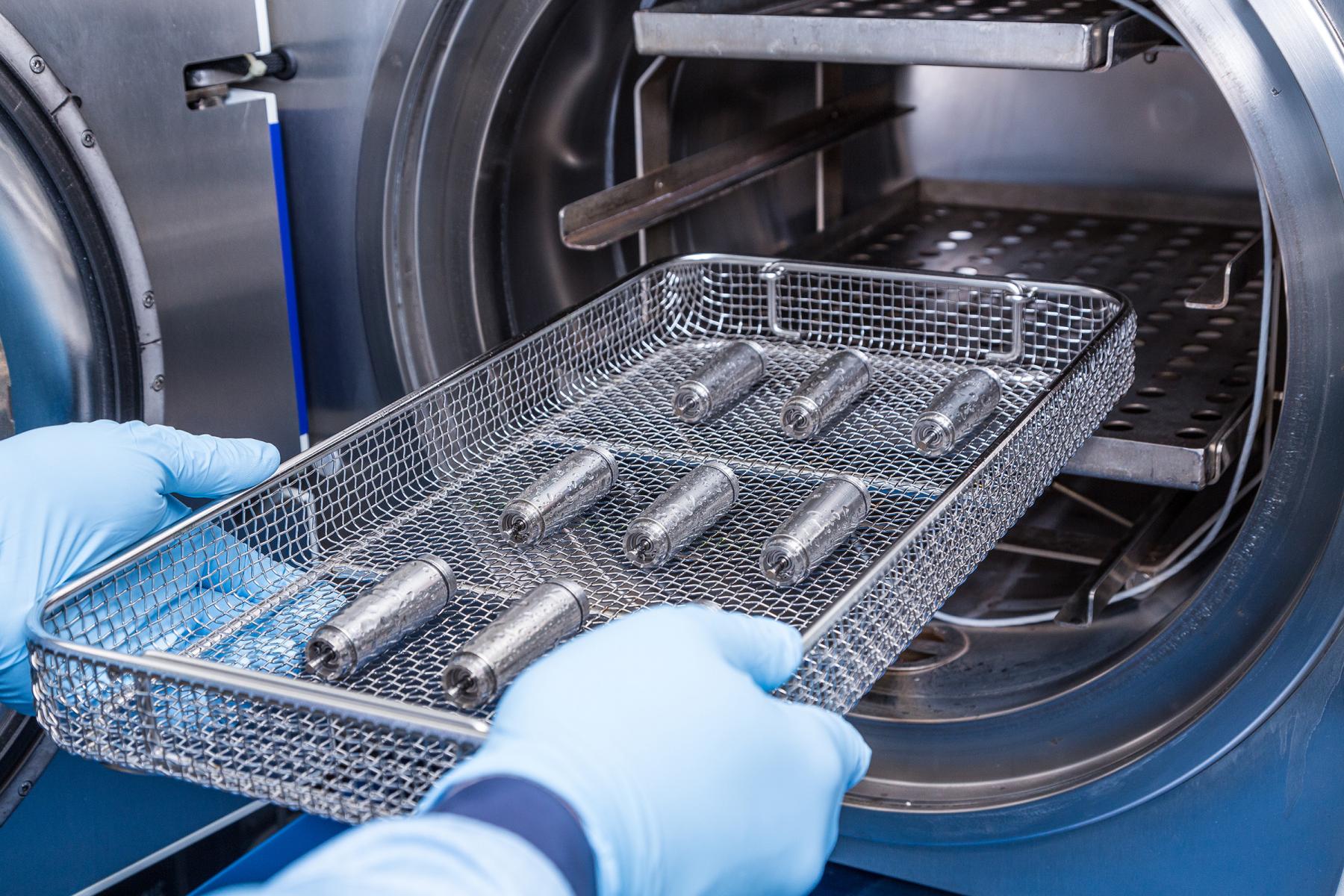