The advantage of the fixed wing vertical take-off and landing (VTOL) aircraft, commonly referred to as a tiltrotor, is that it can be launched from an area as compact as a building roof - much like a helicopter - yet its conventional aeroplane wings enable it reach high speeds.
Although concepts began in the 1940s, this flight technology is envisioned for the future. While tiltrotor models like the V-22 Osprey and the AW609 are in operation today, forecasts predict the prospect of electric VTOL aircraft operating in our skies within 10 years, as taxis and for delivery vehicles.
A challenge to tiltrotor aircraft design is the phenomenon of whirl flutter. Whirl flutter is an instability that occurs via elastically mounted propeller rotors, causing the entire wing-rotor system to vibrate. This phenomenon kicks in when a critical speed, specific to the design of each individual aircraft, is reached. Beyond this critical speed, whirl flutter can create vibrations strong enough to shake the wing apart.
Current tiltrotors typically use thick wing sections to increase the rigidity of the wing-rotor system and push whirl flutter to higher critical speeds. This, however, comes with a cost of increased structural weight, and higher aerodynamic drag, requiring more power to lift the aircraft in helicopter mode and more power to overcome aerodynamic drag in aircraft mode.
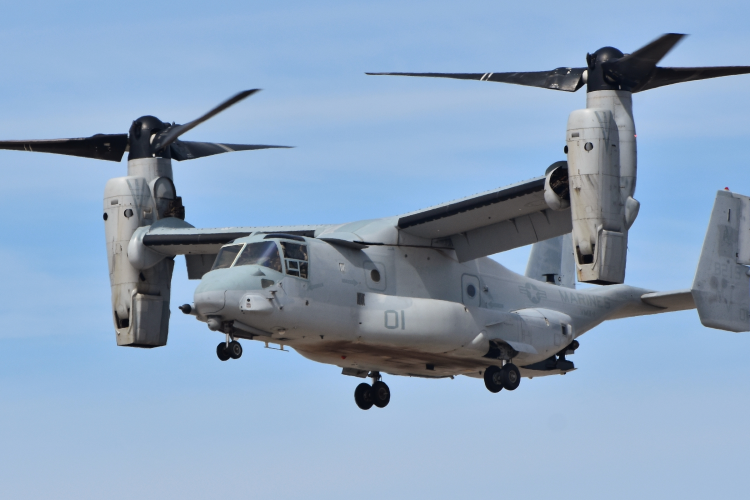
Active control of whirl flutter
An attractive solution is the use of active aerodynamic control devices that can alter the wing loads in real-time to counteract vibrations. If successful, such a control system would relax the need for thick wings and allow the aircraft to push past the critical speed where whirl flutter occurs.
With the aim of developing a new aerodynamic control technique to tackle whirl flutter, researchers at the Institute for Propulsion and Mobility (IPM) at the University of Bath have designed and built a novel wind tunnel experiment to simulate whirl flutter vibrations, while simultaneously deploying an aerodynamic control strategy.
“Testing aerodynamic control strategies for whirl flutter is not a simple process. Not only do we have to assess their performance across a wide range of deployment speeds, we also have to observe how that performance changes on a vibrating wing – similar to what would occur on the real aircraft undergoing whirl flutter,” says the Institute’s Dr. Sam Bull.
With a team at IPM, Sam is investigating an aerodynamic control device known as a mini-tab, which is a miniature spoiler that deploys above and below the surface of the wing to alter the aerodynamic load. The theory is that when an aircraft approaches its critical speed, the mini-tabs deploy at high speed, protruding above and below the wing by up to 2% of the wing width - 10 mm in their experiments - to calm whirl flutter vibrations.
“On an aircraft, conventional control surfaces, known as a flaperon or aileron, deploy to change the loads around the wing. However, the size and weight of these control surfaces mean you can't move them very fast. Mini-tabs, on the other hand, have a relatively low mass, meaning you can deploy them much faster, giving the potential to counteract the effect of whirl flutter,” says Sam.
To achieve this, the team has developed a wing model with integrated mini-tabs for wind tunnel testing. The wind tunnel can recreate unsteady conditions that simulate a tiltrotor wing undergoing whirl futter. As this concept has never been tested before experimentally, the aim of the study is to gain fundamental knowledge on the effectiveness of counteracting whirl flutter. If successful, IAM, or third-party developers, could investigate turning the principle into a reality for use on real life tiltrotor aircraft.
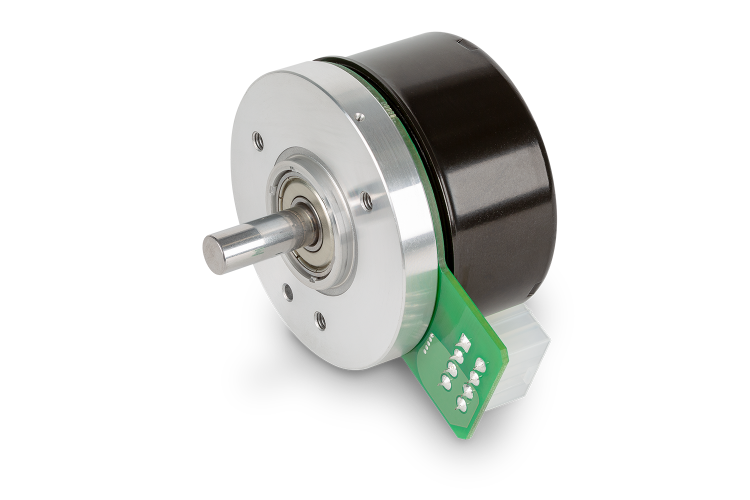
Mini-tab experimentation
For the experiments, the mini-tab device was installed towards the rear of the wing, ahead of the hinge line where an aileron would be located on a real aircraft. The wing was suspended from the ceiling of the wind tunnel, where a set of hydraulic actuators drove oscillations in three degrees of freedom – parallel to the airflow (known as surge), perpendicular to the airflow (known as plunge), as well as rotation (known as pitch). Meanwhile, the team monitored mini-tab performance via an array of pressure sensors located within the wing model.
Powering the mini-tab is a motor mounted within the wing. To achieve accurate test results in a wind tunnel environment, the team required a motion solution that could deploy the device at high frequencies, with high precision and low latency.
The university’s Dr Ioannis Georgilas, who had previous experience working with maxon motors, recommended the motion solution provider. Along with the control system expertise of PhD student, Dominic Wilson, the team developed an updated motor specification.
The mini-tab device is driven by a maxon EC 60 brushless 200W motor with integrated Hall sensors for position feedback.
“After running the autotune feature, which took less than a minute, the motor performed with the control we needed, straight away,” says Sam.
The motion system is driven with both feedforward and feedback control. The combination of the two reduces lag time and helps oppose the acceleration effects of the wing vibrations, which would otherwise cause the mini-tab to drift from the intended deployment position.
“What we were most concerned about was accurate position feedback,” says Sam. “We needed really clean feedback signals so we could achieve high positional accuracy at a given deployment frequency. The maxon motion system gives us this performance.”
Result
With early stages of experimentation completed, what do the results show so far?
“Our experimental pressure data shows that when you start deploying a mini-tab, it changes the pressure field around the entire wing. Already we know that you can use these devices to augment the pressure and the loads around the wing to counteract whirl flutter vibration.”
Nobody has experimentally tested this concept before on a moving wing, so with this set-up, Dr. Sam Bull and the IPM team are the first in the world to achieve this. So what could the discovery mean for the future of tiltrotor aircraft design?
“The aerodynamic response from the mini-tab is nonlinear, so it’s difficult to predict. This adds to the challenge of designing a controller that can effectively deploy the mini-tabs to counteract whirl flutter. We’re currently at the stage where we’re understanding and characterising the aerodynamics, but if we could develop a model of this in the future, we could potentially design a controller to tame whirl flutter vibrations: that would be the next stage.”
With a technological push towards the next generation eVTOL aircraft, research led by Dr. Sam Bull and the IPM team at the University of Bath is set to be increasingly important.