The goal of our project is to create a dual-arm collaborative robot with a humanoid shape entirely designed, made, and built at Polytechnique Montréal (Canada). Robotics, being at the heart of the new 21st century industrial revolution, is a field which echoes with both fear and hope in our society. Taking these concerns in mind, we aim at building a “collaborative” robot which means that it will be able to safely interact with humans without any risk of hurting them. Contrary to classic robots that can be found in most factories, the goal of a collaborative robot is not to replace humans but to support and assist them during repetitive and/or dangerous jobs.
The human teaches the robot how to complete its task and then, the robot will repeat it. This human operator is still needed to supervise the robot and provide his/her intelligence to interpret and react to various situations. Indeed, despite the recent progresses made by A.I. general situation awareness and interpretation still requires skills that are far beyond what common robots can do. Our solution to this challenge is to combine both man and machine in harmony using the robot for strength and endurance while the human provides intelligence. A practical example would be a situation where the robot lifts heavy objects that need to be moved but the human guides the arm of the robot and places the object at the precise spot it needs to be.
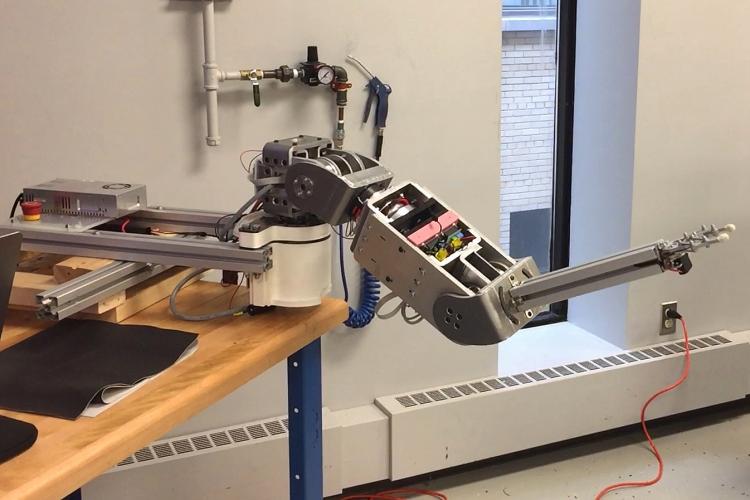
Collaborative robots will one day also be able to assist people in their house, in case of a physical disability, to complete different tasks from everyday life as well as provide aid and assistance in case of emergency. Collaborative robots must be designed to be intrinsically safe and be able to detect possible collisions with the user to avoid any contact forces that could harm him or her. We also want to make our robot look like us so it can interact in an environment that was originally designed for us. Therefore, it will have two arms, two hands, one head, etc. Building such a complex mechatronic system is of course a significant endeavor, both from a time and monetary perspective.
Our project is a long-term one, of at least 5 years, during which every group of students enrolled in this capstone project will work on designing, fabricating and testing various parts of the robot one step at a time. Each group will need to integrate the work that was made the previous year, improving and completing it to go further every year. To this aim, we have been using Maxon EC 90 brushless motors with high resolution MILE optical encoders in every joint of the robot so far. We are targeting very demanding requirements with a payload of 5 kg and a repeatability of less than 0.1 mm. These Maxon actuators can provide us with the high torque and precision we need to achieve this. The small size and large power-to-weight ratio of the motors also make them ideal for our design. Preliminary results using a first prototype of an arm indicate that we made the right choice as we were able to measure a repeatability of less than half our requirement.
Lionel Birglen, Professor at Polytechnique Montréal