The motors used in artificial limbs can serve a wide range of functions: For the movement of a gripper, an individual finger, or even the movement of an entire arm or leg. Accordingly, a range of different motor shapes and sizes come into use. For instance, the motor on the main joint of the arm needs to be relatively strong and big. The motor in the hand, on the other hand, should be small and lightweight, in order to keep weight and inertia down to a minimum.
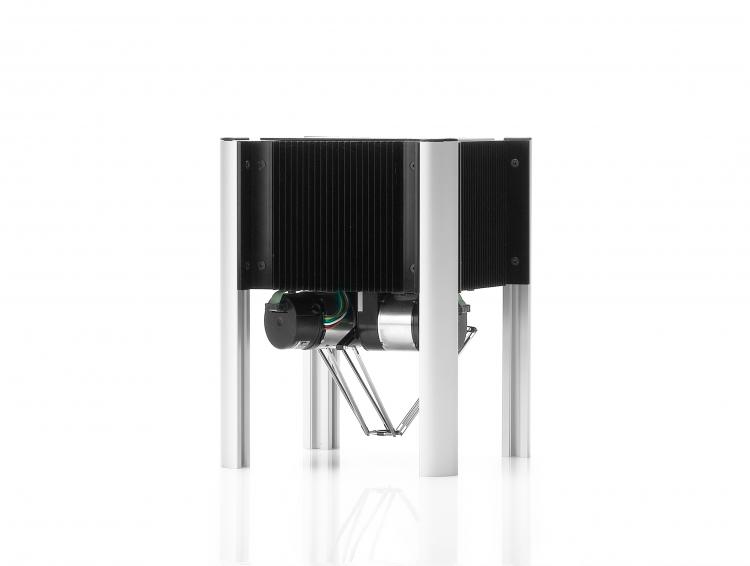
Pocket Delta robot
Flexibility through modularization
For drives, modularization means that every motor is locally controlled by an intelligent controller. A central computer issues the movement commands via a field bus. This decentralized strategy provides high flexibility as well as additional advantages.
In the simplest case, there are multiple individual axes that are controlled independently of each other. One example of this is a gripper hand, mounted to a rotating joint (the wrist). Gripping and releasing a cup (finger movements) is performed independent of the actual position of the wrist. The movements are carried out one after the other as a sequence of individual movements. In this “loosely coupled” system, the axes receive movement commands via a field bus from a central master system. The movements are autonomously carried out and controlled in the modules.
Among the products in maxon motor's portfolio, the EPOS product family in positioning mode are an example of loosely coupled, decentralized modules. EPOS products are controlled via a CANopen fieldbus, which is affordable and compact, but at 1 Mbit/s, not particularly fast.
Interpolation – synchronization in advance
A first step for synchronized control of multiple drives is the use of Interpolated Position Mode (PVT: Position and Velocity versus Time). The machine controller (master) calculates the motion of all of the drives in advance, based on the position and speed of the existing interpolation points, and saves these to the buffer memory of the individual positioning controllers, which calculate the set values for the positioning control loop. The movements of the individual axes are started synchronously. The periods between the interpolated points of the Interpolated Position Mode are typically 10 – 100 ms, minimizing the load on the bus and the real time load on the bus master.
The Interpolated Position Mode is useful for applications such as the automatic repositioning of telescope or solar mirrors or the control of machine tools with set defined axis movements. A disadvantage of this operating mode is that fast changes in a movement are not possible. For instance, if the movement will also be synchronized using external sensors (vision, encoders from a conveyor belt), this type of movement planning and control is simply too slow.
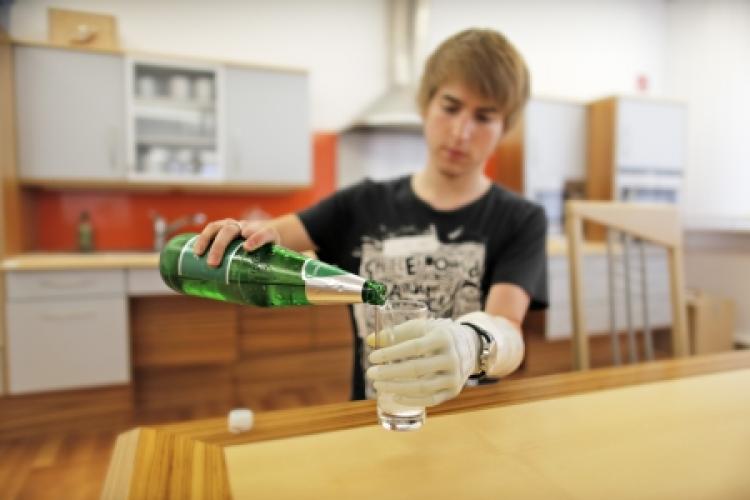
High complexity requires centralized control
In the case of more complex applications, the axes have to be centrally controlled. In the arm prosthesis that brings a full cup of water to a person's lips, the axes in the shoulder, elbow and wrist are controlled synchronously – they are interdependent. In these strongly coupled axis systems, the positioning control loop is no longer enclosed in the module, but instead in the master. The modules serve either as speed controllers or, for applications with extremely complex dynamics, simply as current controllers.
The information on the movement status of each axis is routed to the computer. The central path planning and control uses this information to generate set current values for the remaining motion and sends these to the individual axes. These strongly coupled systems require a bus system with sufficient capacity, and the path planning has to occur in real time.
The EPOS positioning controllers by maxon motor can also be operated as torque controllers. The current control mode in these applications is very dynamic; however, the communication via the CANopen runs up against its limits. Nevertheless, the example of the PocketDelta robot shows that if developers put their minds to it, these limits can be pushed quite far.

Conclusion: Robotics is mechatronics in its purest form
To be successful and economical, mechatronic applications require the right balance between integration and modularization. Integration results in the success of the total package, modularization allows the economical use of standard components.
But don't forget: The quality of motion depends on the successful coordination of all the components involved: controllers, power elements, sensors, mechanisms, and load characteristics. There's no use in simply optimizing a single element.